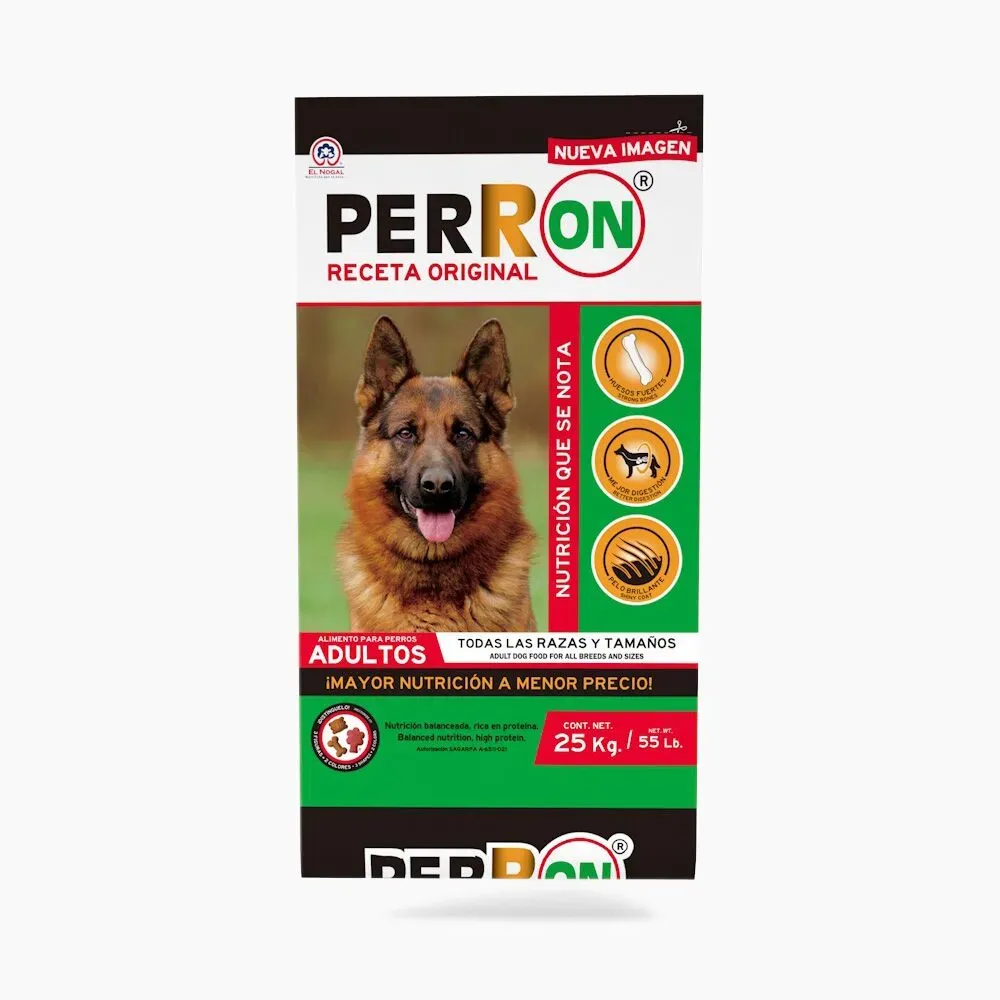
- What Are Laminated Woven Bags?
- Types of Laminated Woven Bags
- Material Selection in Laminated Woven Bags
- Characteristics and Benefits of Key Materials in Laminated Woven Bags
- The Production Process: Multi-layered Co-extrusion Blown Film
- Advantages of Using Laminated Woven Bags
- Applications of Laminated Woven Bags
- Environmental Considerations
- Conclusion
In the packaging industry, Laminated Woven Bags stand out for their versatility, durability, and adaptability to various applications. From food to industrial goods, these bags offer a secure and reliable solution for packaging needs. One of the most advanced processes for producing these bags involves the multi-layered co-extrusion blown film process, which ensures high strength, moisture resistance, and excellent print quality for effective branding. This article explores the materials best suited for Laminated Woven Bags, including PP, HDPE, PE, and aluminum foil, examining their unique characteristics and functions.
For more on the advancements and benefits of laminated woven bags, check out this detailed guide.
What Are Laminated Woven Bags?
Laminated woven bags consist of woven polypropylene (PP) fabric with a laminated layer, which adds strength and water resistance, making them ideal for products like grains, chemicals, and construction materials. The multi-layered co-extrusion process used in the production of Laminated Woven Bags involves extruding several layers of film to create a robust structure, making these bags suitable for heavy-duty use and demanding storage conditions.
Types of Laminated Woven Bags
- BOPP Woven Bags: These are polypropylene woven bags laminated with BOPP film, known for their excellent printability, which allows for high-quality branding.
- Laminated PP Bags: These bags use a laminated layer of polypropylene for added durability and are commonly used for packaging agricultural products.
- Multi-wall Woven Bags: These bags are made using multiple layers of laminated material, providing extra strength for heavy loads and are often used for industrial goods.
Material Selection in Laminated Woven Bags
Material choice is critical in determining the functionality and strength of woven bags. Below is an analysis of commonly used materials in Laminated Woven Bags and their unique properties.
Material | Characteristics | Functionality in Laminated Woven Bags |
---|---|---|
PP (Polypropylene) | High tensile strength, moisture resistance, lightweight, recyclable | PP is the core material for woven bags, offering structural integrity and durability. Ideal for carrying heavy loads. |
HDPE (High-Density Polyethylene) | Higher strength than standard PE, excellent chemical resistance, less flexible | HDPE adds extra rigidity and resistance, useful in multi-wall woven bags for heavy industrial goods. |
PE (Polyethylene) | Soft, flexible, moisture-resistant, cost-effective | PE liners are often used in conjunction with woven fabric to enhance moisture protection in bags like Laminated PP Bags. |
Aluminum Foil | Excellent barrier properties against light, oxygen, and moisture | Aluminum foil is ideal for products that need maximum protection from external elements, often found in multi-wall laminated woven bags for sensitive goods. |
Characteristics and Benefits of Key Materials in Laminated Woven Bags
1. Polypropylene (PP)
PP is the most commonly used material for Laminated Woven Bags. It provides excellent durability, a high strength-to-weight ratio, and moisture resistance, making it suitable for a range of uses.
- Durability and Flexibility: PP has a high tensile strength and is resistant to stretching, making it ideal for bags carrying heavy goods.
- Moisture Resistance: PP’s moisture barrier properties help protect sensitive goods, such as grains and flour, from humidity.
- Printability: The surface of PP can be laminated with a BOPP film, which enhances its printability and enables high-quality branding and design on bags like BOPP Woven Bags.
2. High-Density Polyethylene (HDPE)
HDPE is another strong, resilient material often used in combination with PP or PE for enhanced performance.
- Extra Strength: HDPE is more rigid and durable than standard PE, making it suitable for high-load packaging requirements.
- Chemical Resistance: HDPE has excellent resistance to most chemicals, making it a preferred material for industrial goods and chemicals.
- Compatibility in Multi-wall Woven Bags: HDPE’s rigidity makes it ideal for multi-layered bags, providing the structural integrity required in industries like construction and chemicals.
3. Polyethylene (PE)
PE, specifically as a liner or coating material, enhances the barrier properties of woven bags, providing additional protection against moisture.
- Softness and Flexibility: PE adds a layer of softness and flexibility, making bags easier to handle and reducing damage to sensitive products inside.
- Cost-Effective: PE is an economical material choice for basic moisture resistance without adding significant weight.
- Uses in Laminated PP Bags: Often used as a liner inside Laminated PP Bags, PE enhances moisture resistance, especially for products like grains and fertilizers that need protection from external humidity.
4. Aluminum Foil
Aluminum foil is a premium material for specialized applications where protection from light, oxygen, and moisture is essential.
- Barrier Properties: Aluminum foil provides a superior barrier against light, oxygen, and moisture, preserving the quality of contents that are sensitive to these factors.
- Ideal for Multi-wall Laminated Woven Bags: With its barrier properties, aluminum foil is often incorporated into multi-wall woven bags for high-value or perishable products.
- Enhanced Shelf Life: Aluminum-lined bags are suitable for long-term storage and export packaging, particularly for food products and pharmaceuticals.
The Production Process: Multi-layered Co-extrusion Blown Film
The multi-layered co-extrusion process is critical in producing high-quality Laminated Woven Bags. This technology enables the blending of multiple materials in a single film, enhancing each layer’s specific properties. Here’s how the multi-layered co-extrusion process works for woven bags:
- Layered Construction: Each layer serves a unique function—one may provide strength (like a PP layer), while another enhances moisture resistance (like a PE layer).
- Blown Film Extrusion: The blown film extrusion technique is used to create films with consistent thickness, providing uniform protection across the bag’s surface.
- Lamination: The multi-layer film is laminated onto a woven PP base, providing a smooth, printable surface for branding on BOPP Woven Bags and other types.
Advantages of Using Laminated Woven Bags
Laminated Woven Bags offer numerous benefits, from durability and strength to cost-efficiency and environmental sustainability. Below are some key advantages.
Advantages | Details |
---|---|
Durability | Multi-wall structure provides strength for heavy or dense products. |
Moisture Resistance | Lamination enhances resistance to water and humidity. |
Printability | Laminated surfaces support high-quality printing for branding. |
Versatility | Suitable for various markets, from food to industrial goods. |
Cost-Effective | Durable and reusable, reducing packaging costs over time. |
Applications of Laminated Woven Bags
Laminated woven bags have wide-ranging applications across industries:
- Agriculture: Used for packaging grains, seeds, and fertilizers. BOPP Woven Bags are especially popular due to their print quality and durability.
- Industrial and Chemical: Multi-wall woven bags with HDPE or aluminum foil liners are used for industrial chemicals, construction materials, and hazardous materials.
- Food Packaging: Aluminum-lined woven bags ensure longer shelf life for food items by blocking light and moisture, while PE-coated bags are preferred for less-sensitive food items.
- Retail: High-quality print on laminated bags enables branding, making them a choice for retail products such as pet food.
Environmental Considerations
Laminated woven bags are recyclable and, when constructed from PP, contribute to sustainable packaging efforts by reducing single-use plastic. Polypropylene’s recyclability makes it an attractive option in eco-conscious markets, as the bags can be reused multiple times before recycling.
Conclusion
The selection of materials and the use of advanced processes like multi-layered co-extrusion blown film make Laminated Woven Bags a standout solution for diverse packaging needs. By choosing the right materials—whether PP for structural integrity, HDPE for rigidity, PE for flexibility, or aluminum foil for superior protection—industries can meet specific packaging requirements while maximizing product protection. The evolution of these bags continues to shape the future of secure, sustainable packaging across global markets.