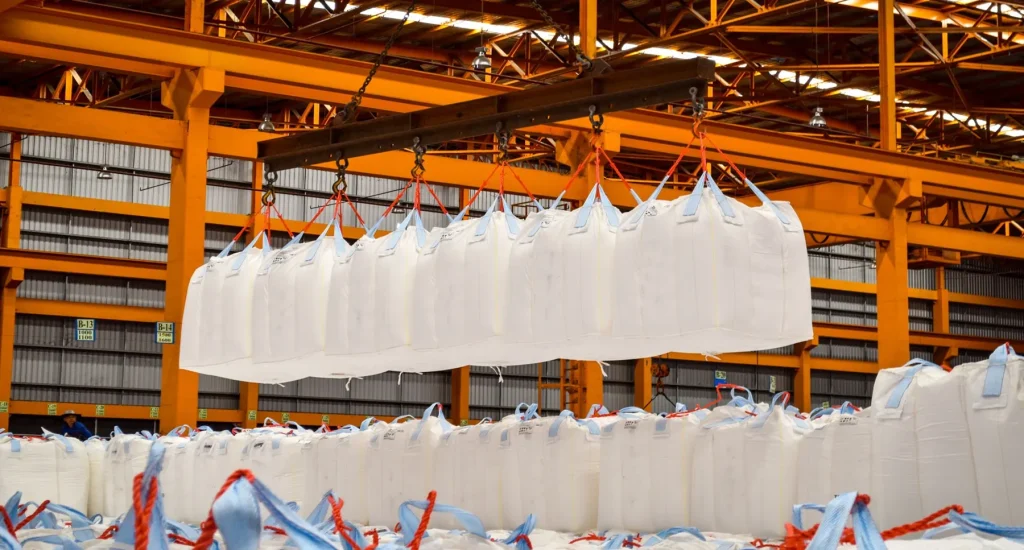
Multiwall laminated woven bags are the backbone of modern bulk packaging, offering unmatched durability, customization, and cost-efficiency for industries ranging from agriculture to hazardous material handling. At VidePak, a global leader in woven bag manufacturing since 2008, we specialize in engineering multiwall laminated woven bags that address the unique challenges of diverse sectors. With load capacities up to 2,000 kg, customizable barrier layers (PE, aluminum foil), and precision sealing systems, our bags reduce waste by 30% and improve supply chain safety for 800+ clients across 45+ countries. Supported by 30+ years of industry expertise and Austrian Starlinger machinery, we produce 100 million bags annually, ensuring compliance with ISO, REACH, and FDA standards.
1. What Are Multiwall Laminated Woven Bags?
Multiwall laminated woven bags combine layers of polypropylene (PP) woven fabric with functional coatings or liners to create a robust, adaptable packaging solution. These bags are designed for:
- Heavy-Duty Logistics: Transporting construction materials, chemicals, and agricultural products.
- Moisture/Oxygen Sensitivity: Protecting hygroscopic goods like fertilizers or pharmaceuticals.
- Branding Needs: High-resolution printing for retail-ready packaging.
Example: A 2024 study by Packaging Digest found that multiwall laminated bags reduced grain spoilage rates by 18% compared to single-layer alternatives in humid climates.
2. How to Choose the Right Packaging Configuration
Step 1: Determine the Need for Lamination
- Laminated Bags: Essential for moisture resistance (e.g., BOPP-laminated bags block 99% of water vapor).
- Non-Laminated: Suitable for dry, non-sensitive products like animal feed.
Case Study: A Vietnamese coffee exporter reduced moisture-related losses by 25% after switching to VidePak’s BOPP-laminated bags with 120 g/m² PP fabric.
Step 2: Select Inner Liner Material
Liner Type | Key Features | Ideal Applications |
---|---|---|
PE Liners | Moisture barrier, cost-effective | Fertilizers, grains |
Aluminum Foil | Blocks oxygen, UV light | Pharmaceuticals, chemicals |
Anti-Static | Dissipates electrostatic charges | Electronic components |
Why PE Liners?
- Cost Efficiency: 20–30% cheaper than aluminum foil.
- Flexibility: Withstand temperatures from -30°C to 80°C.
- Recyclability: Compatible with PP recycling streams.
Step 3: Choose Sealing Mechanisms
- Heat Sealing: For airtight closure (e.g., valve bags for powdered cement).
- Sewn Closure: Reusable options with polypropylene threads.
- Block Bottom: Self-standing design for retail displays.
3. Technical Specifications and Customization
VidePak’s multiwall laminated bags are engineered using virgin PP resin and Starlinger circular looms, ensuring:
- Grammage: 90–200 GSM.
- Burst Strength: 3,500–5,500 kPa (ISO 2758).
- Layer Count: 2–5 layers, with optional PE/aluminum interlayers.
Example: Our 3-layer laminated FIBC bags with PE liners support 1,500 kg loads for construction waste, reducing tear incidents by 40% in a 2023 UAE infrastructure project.
4. Industry-Specific Applications
Agriculture
- Breathable Designs: Micro-perforated PE liners reduce condensation in rice packaging.
- UV-Resistant Prints: Withstand 12 months of outdoor storage.
Chemicals
- HDPE Liners: Resist corrosive substances like ammonium nitrate.
- Anti-Static Coatings: Surface resistivity of 10⁶–10⁹ Ω (IEC 61340-4-4).
Retail
- High-Gloss BOPP Lamination: CMYK/PMS printing for brand visibility.
- Handle Attachments: Reinforced loops for consumer convenience.
5. FAQs: Critical Questions from Buyers
Q1: How does lamination affect bag recyclability?
A: Our BOPP and PE laminates are designed for easy separation during recycling, complying with EU Circular Economy standards.
Q2: What is the lead time for custom designs?
A: 15–20 days for orders up to 50,000 units, supported by 30+ lamination machines.
Q3: Can bags withstand maritime humidity?
A: Yes. Aluminum foil liners block 99.9% moisture ingress, as validated in a 2024 test by SGS.
6. Why VidePak Leads the Market
- Global Infrastructure: 100+ circular looms, 16 extrusion lines, and ISO 9001-certified QC labs.
- Sustainability: Solar-powered production (40% energy offset) and 100% recyclable materials.
- Customization: Tailored solutions like FIBC bulk bags with PE liners for construction debris or kraft paper laminated bags for eco-conscious brands.
References
- VidePak. (2025). BOPP Laminated Woven Bags: Branding and Market Dynamics.
- VidePak. (2025). Kraft Paper Bags Laminated with Woven Fabric: Advanced Production Processes.
- VidePak Co., Ltd. Website: https://www.pp-wovenbags.com/. Email: info@pp-wovenbags.com.
Data validated as of March 2025. Specifications subject to regional regulations.