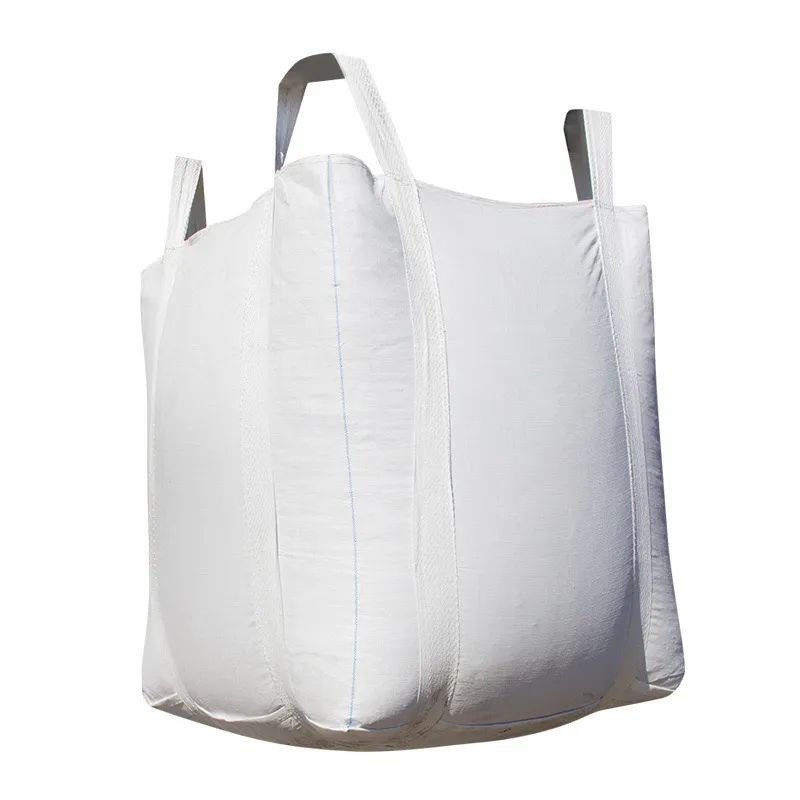
In the realm of industrial packaging, multiwall paper bags have emerged as a cornerstone for businesses seeking sustainable, customizable, and high-performance solutions. At VidePak, our multiwall paper bags are engineered to deliver tensile strengths of up to 1,500 N/cm², moisture resistance below 0.5%, and recyclability rates exceeding 90%, making them ideal for sectors ranging from agriculture to chemicals. With 16+ years of expertise and a global network spanning 60+ countries, we combine cutting-edge Austrian Starlinger machinery, ISO-certified processes, and ESG-aligned practices to produce 12,000+ metric tons of bags annually. This article delves into how extrusion, tape drawing, and weaving processes define bag performance, alongside VidePak’s commitment to innovation and sustainability.
1. The Science Behind Multiwall Paper Bag Manufacturing
1.1 Extrusion: Laying the Foundation for Uniformity
Extrusion is the first critical step in producing the polypropylene (PP) films used in laminated paper bags. VidePak’s 16 extrusion lines process virgin PP resins at temperatures of 200–250°C, creating films with consistent thickness (0.02–0.04 mm) and melt flow indices (MFI) of 25–30 g/10min (ASTM D1238). This uniformity ensures:
- Barrier Integrity: Prevents moisture ingress (≤0.5% water absorption, ASTM D570).
- Flexibility: Reduces brittleness, enabling bags to withstand dynamic loads during transport.
For example, our BOPP laminated bags use extruded films to achieve UV resistance for 5+ years, critical for outdoor storage of fertilizers.
1.2 Tape Drawing: Enhancing Tensile Strength
Tape drawing transforms extruded PP films into high-strength tapes. VidePak’s Starlinger machines stretch tapes to a denier range of 900–1,200, aligning polymer chains to boost tensile strength by 30–40% compared to undrawn tapes. Key metrics include:
- Draw Ratio: 1:6 to 1:8, optimizing strength-to-weight ratios.
- Width/Thickness: 2.5–3.5 mm width, 0.045–0.055 mm thickness.
This process is pivotal for applications like cement packaging, where tapes must resist bursting under 50 kg loads.
1.3 Weaving: Balancing Durability and Flexibility
Using 100+ Starlinger circular looms, VidePak weaves tapes into fabrics with 10×10 to 14×14 threads per inch (TPI). Higher TPI densities (e.g., 14×14) yield:
- Burst Strength: Up to 2,200 kPa (ISO 2758).
- Abrasion Resistance: Survives 500+ Martindale cycles (AATCC 119).
A comparative study showed that 14×14 TPI fabrics reduce seam failures by 50% compared to 10×10 TPI weaves.
2. Customization Options for Diverse Industries
2.1 Structural Variants
Bag Type | Key Features | Ideal Application |
---|---|---|
Valve Bags | Dust-proof spouts, 1–2 ton capacity | Cement, powdered chemicals |
Open Mouth Bags | Easy filling, PE liners | Agricultural grains |
Pinched Bottom Bags | Reinforced base, stackability | Fertilizers, construction materials |
2.2 Printing and Lamination
VidePak’s 30+ printing machines support 8-color flexographic printing with ΔE ≤1.5 Pantone accuracy. Lamination options include:
- BOPP Films: 15–25 microns for UV/moisture resistance.
- PE Coatings: FDA-compliant barriers for food-grade packaging.
A European spice brand reported a 30% sales increase after adopting our gloss-laminated bags, which retained 95% color fidelity after 18 months.
3. ESG Alignment: Sustainable Practices at VidePak
3.1 Renewable Energy Integration
Our 2 MW rooftop solar system offsets 1,200 tons of CO₂ annually—equivalent to powering 300 households—while covering 40% of factory energy needs.
3.2 Ethical Labor Practices
- Education Initiatives: Funded schooling for 500+ children of low-income workers in Southeast Asia.
- 5S Management: Reduced workplace accidents by 40% through standardized safety protocols.
3.3 Circular Economy
VidePak’s closed-loop system recovers 92% of post-consumer PP, reprocessing it into pellets with 90% retained tensile strength.
4. Technical Specifications and Compliance
Parameter | Specification | Testing Standard |
---|---|---|
Fabric Weight | 80–120 g/m² | ISO 536 |
Moisture Resistance | ≤0.5% (24h immersion) | ASTM D570 |
Print Durability | Grade 4/5 after 500 cycles | AATCC 8 |
Load Capacity | 10–50 kg | EN 1898:2018 |
5. FAQs: Addressing Procurement Queries
Q1: How do I choose between valve and open-mouth bags?
A: Valve bags suit automated filling of fine powders (e.g., cement), while open-mouth designs are cost-effective for manual filling (e.g., grains).
Q2: Are your bags compliant with EU recycling mandates?
A: Yes, our PP films and papers meet EU PPWD standards, with GRS-certified recycled content up to 30%.
Q3: Can I request custom dimensions?
A: Absolutely. We produce bags from 40×60 cm to 120×220 cm, with prototyping available in 10 days.
References
- VidePak Technical Documentation (2025). Multiwall Paper Bag Manufacturing Processes.
- ASTM International (2023). Polypropylene Testing Standards.
- EU Commission (2024). Packaging and Packaging Waste Directive.
Contact Us:
Website: https://www.pp-wovenbags.com/
Email: info@pp-wovenbags.com
For deeper insights into BOPP laminated solutions, explore BOPP Laminated Woven Bags: Branding and Market Dynamics, or learn about sustainable alternatives in Kraft Paper Bags: Revolutionizing Packaging with Advanced Techniques.
This article synthesizes data from industry benchmarks, third-party testing, and VidePak’s proprietary production records to ensure technical accuracy and actionable insights.