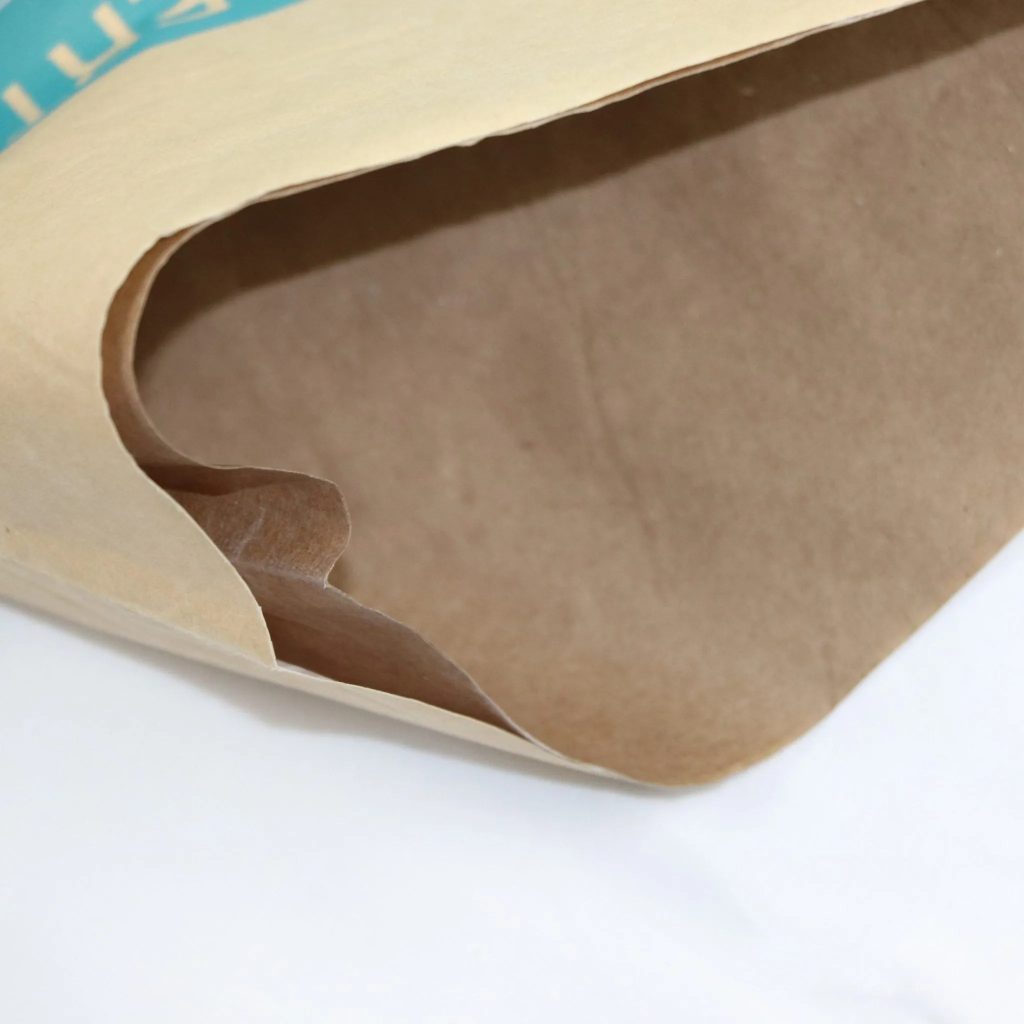
- Types of Multiwall Paper Bags
- Lamination and Layer Structure of Multiwall Paper Bags
- Chemical Packaging Requirements for Different Products
- Selecting the Right Multiwall Paper Bags According to International Standards
- How to Choose the Right Multiwall Paper Bags for Chemical Packaging
- Frequently Asked Questions (FAQs)
In the world of industrial packaging, Multiwall Paper Bags (also known as Multiwall Paper Sacks) are essential for a wide range of products, particularly chemicals and raw materials. These bags are designed to meet the demands of packaging heavy and granular products such as fertilizers, plastic pellets, activated carbon, carbon black, disinfectants, and other chemical compounds. This blog explores the various types of Multiwall Paper Bags, the structure of the laminate layers used in their production, and how to choose the right packaging based on industry standards (European, American, Japanese, Australian, and Chinese).
Types of Multiwall Paper Bags
Multiwall Paper Bags are primarily used for bulk packaging in industries that require durable and secure packaging for powders, granules, and other solid products. These bags come in different configurations, depending on the needs of the product being packed. Here’s an overview of the most common types of Multiwall Paper Bags:
- Plain Paper Bags: These bags consist of multiple layers of kraft paper, typically designed for dry products that are not highly sensitive to moisture. These are commonly used for dry chemicals, cement, and other powdered materials.
- Laminated Paper Bags: These bags feature an additional layer of protection, often made from materials like polyethylene (PE) or polypropylene (PP), to enhance the strength and water resistance of the bag. The laminated layer helps protect against moisture, which is critical for products such as fertilizers or plastic granules.
- Coated Paper Bags: Often used for fine chemicals or granular substances that need a higher degree of moisture or contamination protection. The coated surface adds an extra barrier to keep the contents secure.
- Valve Bags: These bags are equipped with a valve at the top, making them ideal for automatic filling systems. They are widely used in the packaging of fine powders or other materials that require efficient and dust-free filling.
- Gusseted Bags: These are paper bags with expandable sides, providing additional volume and making them perfect for bulkier items like fertilizers or charcoal.
- Custom-Printed Bags: Multiwall Paper Bags can also be customized with printed logos, branding, and other marketing information, allowing companies to increase brand visibility while maintaining the integrity of the bag structure.
Lamination and Layer Structure of Multiwall Paper Bags
The lamination and number of layers in Multiwall Paper Bags significantly impact their performance and durability. Typically, these bags are made with two to five layers depending on the required strength, protection, and specific application needs.
- Layer 1 (Inner Layer): This layer is often made from polyethylene (PE) or polypropylene (PP) for moisture and chemical resistance. It may be coextruded or laminated to the paper to provide a higher level of sealing and protection against the elements.
- Layer 2 (Middle Layer): Often made from kraft paper, this layer provides the main strength and structure of the bag. The middle layer is critical for holding the weight of the contents, especially for heavier or bulkier materials.
- Layer 3 (Outer Layer): This layer can be either kraft paper or a custom printed paper that helps with brand visibility. It may also include a barrier against external elements such as dust or contamination.
- Additional Layers: For specialized applications, such as when higher barrier protection is needed, additional layers may include UV-resistant coatings or anti-static layers to prevent electrostatic charges from interfering with the material.
The number of layers and the type of lamination chosen depend on the product’s sensitivity to external factors like moisture, light, or air. The versatility of Multiwall Paper Bags allows them to be tailored to the packaging needs of various industries.
Chemical Packaging Requirements for Different Products
When it comes to the packaging of chemical products such as fertilizers, plastic pellets, activated carbon, carbon black, disinfectants, and other granular materials, selecting the right packaging is crucial. These materials often require specific protection against moisture, contamination, and damage during transportation and storage. Let’s explore the selection of bags for each product type:
Fertilizers
Fertilizers, especially granular ones, can be hygroscopic (absorb moisture from the environment). This can lead to clumping and a decrease in product quality. As such, the selection of packaging must account for:
- Moisture Resistance: Laminated bags are recommended to protect the contents from moisture.
- Strength and Durability: Multiwall Paper Bags with multiple layers are ideal for ensuring that the bag remains intact during transport.
Plastic Pellets
Plastic pellets are used in manufacturing processes, and their packaging must protect them from moisture and dust while preventing contamination. Packaging considerations include:
- Anti-Static Features: Some bags incorporate anti-static coatings to prevent the plastic pellets from clumping together or sticking to the walls of the bag.
- Strength and Tear Resistance: Kraft Paper Woven Bags or Kraft Paper PP Bags offer durability and strength, ensuring the pellets remain safe during handling.
Activated Carbon and Carbon Black
These products are fine powders, and packaging needs to prevent the leakage of dust and the ingress of moisture:
- Valve Bags with additional lamination are commonly used to create a tight seal, preventing dust from escaping and contamination from entering.
- Water Resistance: A laminated or coated layer helps ensure the bags remain intact even in moist environments.
Disinfectants
Disinfectant powders and chemicals often need secure, leak-proof bags to prevent contamination. To select the correct packaging:
- Chemical Resistance: The bags should be resistant to chemicals that could degrade the bag material. A laminated inner layer of PP or PE helps protect the bag from chemical spills.
- Strength and Leak-Proofing: The Multiwall Paper Bags should be strong enough to resist punctures during transit.
Selecting the Right Multiwall Paper Bags According to International Standards
Different markets have different regulatory requirements for packaging, especially in the chemical industry. Understanding the varying standards can help manufacturers and suppliers make informed choices about which packaging to use.
European Standards (EU)
- EN 13592 is the key standard for bags used in packaging products like fertilizers. It specifies requirements for strength, material, and sealing, as well as specific features like the resistance to moisture and the ability to withstand transportation pressures.
American Standards (US)
- ASTM D-1974 focuses on the general construction of the bags, including seal strength, moisture resistance, and durability. It is important to ensure that the bags comply with these specifications when shipping to the U.S.
Japanese Standards (JIS)
- The Japanese Industrial Standards (JIS) emphasize packaging that prevents contamination and deterioration of products like chemicals. JIS also recommends the use of Multiwall Paper Bags for granular and fine chemical products that require additional protection.
Australian Standards
- In Australia, AS 4170 outlines specifications for bags used in packaging chemicals, including strength, moisture resistance, and tear resistance. Packaging for materials like fertilizers or plastic pellets must meet these standards to ensure safety and integrity during transport.
Chinese Standards (GB)
- The Chinese GB/T 1967 standard provides detailed guidelines on bag construction, including the use of multi-layer materials and the strength required for chemical packaging.
How to Choose the Right Multiwall Paper Bags for Chemical Packaging
- Determine the Product’s Sensitivity: For moisture-sensitive products, choose laminated bags with a strong moisture-resistant layer. For more robust products, plain multiwall bags may suffice.
- Consider the Bag’s Strength: For heavy products, use bags with reinforced layers to prevent tearing during handling and transport.
- Assess the Risk of Contamination: Use anti-static bags or bags with chemical-resistant layers for materials like plastic pellets or activated carbon that require additional protection.
- Check Regulatory Compliance: Ensure the packaging meets the appropriate international standards based on where the product will be sold or used.
Frequently Asked Questions (FAQs)
Q1: Can Multiwall Paper Bags be used for food-grade products?
Yes, Multiwall Paper Bags can be used for food-grade products as long as they meet the necessary food safety standards. Laminated options with food-safe coatings or inner liners are commonly used for this purpose.
Q2: What is the difference between Kraft Paper Woven Bags and Kraft Paper PP Bags?
Kraft Paper Woven Bags are typically made of woven paper fibers, while Kraft Paper PP Bags have an additional layer of polypropylene (PP) for extra durability and moisture resistance.
Q3: Are Multiwall Paper Bags customizable for branding?
Yes, many manufacturers offer custom printing on Multiwall Paper Bags, allowing companies to print logos, instructions, or other relevant information for marketing purposes.
For more details about Multiwall Paper Bags and their customization options, check out this article on advanced production processes or explore how Multiwall Paper Bags Manufacturers handle global market demands.