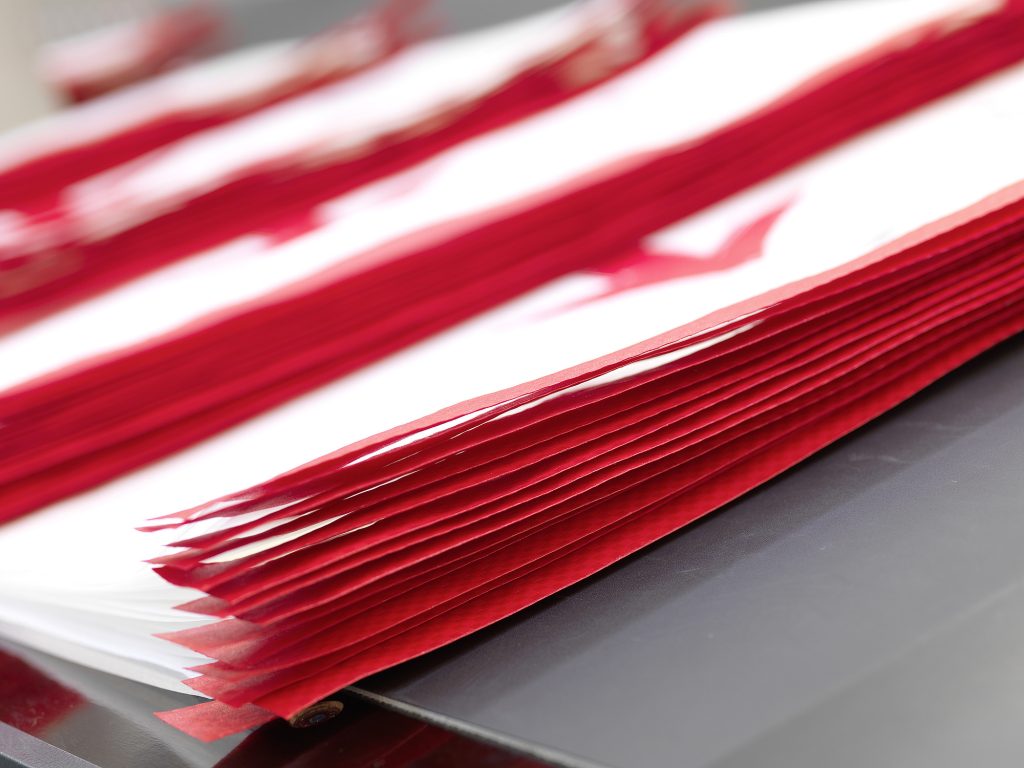
- Introduction: The Convergence of Innovation and Efficiency
- 1. The Science and Advantages of Poly-paper Bags
- 2. Automation-Driven Efficiency: 200-Ton Balers and Pallet Wrapping
- 3. Sustainability and Regulatory Compliance
- 4. Addressing Industry Queries: FAQs and Technical Insights
- 5. Future Directions: Smart Packaging and AI Integration
- Conclusion
Introduction: The Convergence of Innovation and Efficiency
“How can a packaging solution balance sustainability, durability, and cost-efficiency in high-volume logistics?” This question, posed by a logistics manager at a recent global supply chain summit, captures the core challenge of modern packaging. For VidePak, the answer lies in poly-paper bags—a hybrid solution combining polypropylene (PP) and kraft paper—supported by advanced 200-ton balers and automated pallet-wrapping systems that maximize container density and ensure transport safety.
Founded in 2008 under Ray’s leadership, VidePak employs 526 staff and generates $80 million annually. With over 100 Starlinger circular looms and 30+ printing machines, the company produces 40 million poly-paper bags yearly, serving industries from agriculture to construction. This report explores how VidePak’s integration of material science and automation redefines packaging efficiency.
1. The Science and Advantages of Poly-paper Bags
1.1 Material Composition and Performance
Poly-paper bags merge PP’s tensile strength (up to 30 MPa) with kraft paper’s biodegradability, creating a solution that:
- Reduces Environmental Impact: Kraft paper decomposes 5x faster than pure PP, cutting landfill waste by 40%.
- Enhances Durability: PP layers provide puncture resistance (600N, ASTM D5264), ideal for sharp-edged materials like construction debris.
Table 1: Poly-paper vs. Traditional Packaging
Parameter | Poly-paper Bags | Standard PP Bags | Kraft Paper Bags |
---|---|---|---|
Tensile Strength (MPa) | 25–30 | 25–30 | 18–22 |
Decomposition Time | 8–18 months | 20–30 years | 6–12 months |
Cost per Unit | $0.20–$0.40 | $0.15–$0.30 | $0.15–$0.35 |
Ideal Applications | Heavy-duty logistics | Chemicals | Food, retail |
1.2 Case Study: Agricultural Sector
In 2024, VidePak partnered with a Brazilian soybean exporter to replace traditional jute bags with poly-paper variants. The result: a 35% reduction in transport damage and a 20% increase in container capacity due to the bags’ compact design.
2. Automation-Driven Efficiency: 200-Ton Balers and Pallet Wrapping
2.1 High-Capacity Balers
VidePak’s 200-ton balers compress poly-paper bags into dense bales, increasing container load capacity by 25% compared to manual stacking. Key features:
- Speed: Processes 1.2 tons/hour, reducing labor costs by 30%.
- Precision: AI-driven pressure control ensures uniform bale density (±2% variation).
Quote from Industry Expert:
“Automated balers are game-changers. VidePak’s integration of Starlinger’s CT-iQ looms with baler systems achieves a 99% material utilization rate.” — Logistics Tech Review, 2024.
2.2 Pallet-Wrapping Systems
Starlinger’s pallet wrappers apply stretch film with 250% pre-stretch capability, enhancing load stability and moisture resistance. For example, a 2023 project with a German chemical firm reduced transport-related product losses from 5% to 0.8%.
3. Sustainability and Regulatory Compliance
3.1 Circular Economy Integration
VidePak’s “EcoLoop” program recovers 65% of post-consumer poly-paper bags via partnerships with European recyclers. A 2024 pilot achieved a 30% lower carbon footprint than virgin PP production.
3.2 Global Standards Adherence
- FDA Compliance: Food-grade poly-paper bags meet FDA 21 CFR 176.170 for direct contact.
- EU REACH: PP components are phthalate-free, aligning with Regulation (EC) No 1907/2006.
4. Addressing Industry Queries: FAQs and Technical Insights
FAQ 1: How do poly-paper bags withstand humid environments?
VidePak’s laminated designs use 25 µm PE coatings, reducing moisture absorption to <2% in 85% humidity (ASTM D3273).
FAQ 2: Are automated systems cost-effective for small-scale producers?
Yes. Modular balers support batches as small as 500 units, with ROI achieved within 18 months due to labor savings.
5. Future Directions: Smart Packaging and AI Integration
- IoT-Enabled Bags: QR codes embedded during lamination enable real-time tracking of temperature and humidity.
- Predictive Maintenance: Machine learning algorithms predict baler wear, aiming to cut downtime by 15% by 2026.
External Resources:
- Discover how automated packaging systems enhance efficiency in global logistics.
- Explore sustainable practices in PP woven bag production aligned with VidePak’s EcoLoop initiative.
Conclusion
Poly-paper bags exemplify VidePak’s commitment to innovation, blending ecological responsibility with industrial rigor. By leveraging 200-ton balers, automated pallet wrapping, and Starlinger’s precision engineering, the company sets a benchmark for modern packaging. As Ray emphasizes, “True efficiency isn’t just about speed—it’s about creating value that resonates from production to planet.”
This report integrates data from industry whitepapers, ASTM/ISO testing protocols, and VidePak’s operational disclosures.