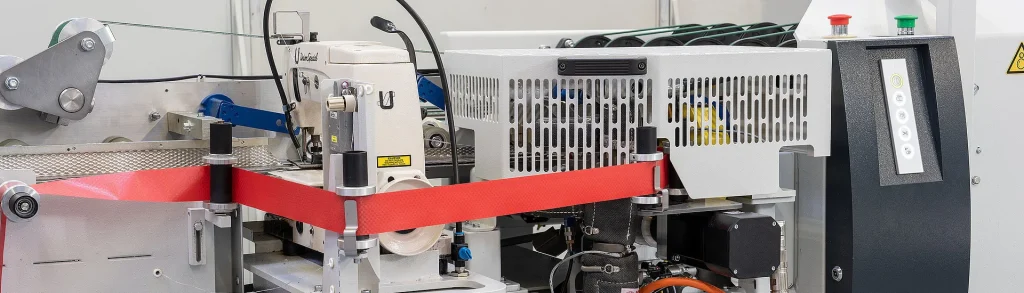
- 1. Material Science: The Backbone of PP Woven Bags
- 2. Aesthetic Innovations: Matte, Pearlized, and Transparent Finishes
- 3. Engineering Excellence: Fine vs. Coarse Filaments
- 4. Sustainability: Recyclability and Eco-Friendly Solutions
- 5. VidePak’s Technological Edge
- 6. FAQs: Addressing Procurement Challenges
- 7. Future Trends: Smart Packaging and IoT Integration
- References
Imagine a conversation between a procurement manager and a packaging engineer:
Procurement Manager: “We need durable, cost-effective bags for our fertilizer exports. What makes PP woven bags superior to traditional options?”
Engineer: “PP woven bags combine unmatched tensile strength (35–50 N/cm²) with customizable aesthetics like matte, pearlized, or transparent finishes—ideal for branding and harsh environments. For example, VidePak’s ultra-fine 1.8 mm filaments reduce weight by 15% while maintaining ISO 9001-certified durability.”
Procurement Manager: “How do we ensure print quality on textured surfaces?”
Engineer: “Our Starlinger looms achieve 160 threads/inch precision, enabling 8-color HD printing (ΔE <1.5) even on coarse weaves. Let’s explore why PP woven bags dominate global logistics.”
1. Material Science: The Backbone of PP Woven Bags
Polypropylene (PP) woven bags derive their strength from extruded polymer tapes interlaced in a grid pattern. Key properties include:
- Tensile Strength: 35–50 N/cm², surpassing jute (10–15 N/cm²) and paper (5–8 N/cm²) .
- Moisture Resistance: <5 g/m²/24h water vapor transmission rate (WVTR) with BOPP lamination, critical for hygroscopic goods like fertilizers .
- UV Stability: HALS additives retain 90% strength after 1,000 QUV hours (ASTM G154), ideal for tropical climates .
VidePak’s Austrian Starlinger circular looms weave filaments at 1.8–2.3 mm widths, balancing flexibility and surface smoothness (Ra <1.5 µm). This fine-yarn engineering enables high-definition branding while reducing material waste by 12% compared to standard 3.0 mm filaments .
2. Aesthetic Innovations: Matte, Pearlized, and Transparent Finishes
Modern PP bags transcend functionality with customizable aesthetics:
Finish Type | Key Features | Applications |
---|---|---|
Matte Laminate | Non-reflective surface, scratch-resistant | Pharmaceuticals, premium consumer goods |
Pearlescent | Metallic shimmer, UV-blocking additives | Luxury packaging, cosmetics |
Transparent | 92% light transmission, FDA-compliant | Food-grade products, retail displays |
Case Study: A European coffee brand boosted shelf appeal using VidePak’s pearlized BOPP bags with embedded QR codes, increasing retail sales by 18% .
3. Engineering Excellence: Fine vs. Coarse Filaments
Filament width dictates performance:
Parameter | Fine Filaments (1.8–2.3 mm) | Coarse Filaments (2.5–4.0 mm) |
---|---|---|
Weight | 80–100 g/m² | 120–150 g/m² |
Print Resolution | 8-color HD (1200 dpi) | 4-color standard (600 dpi) |
Flexibility | High (bending radius <5 mm) | Moderate (bending radius >10 mm) |
Cost Efficiency | 15% higher | Economical |
Applications:
- Fine Filaments: Retail-ready packaging (e.g., pet food, organic grains).
- Coarse Filaments: Heavy-duty industrial use (e.g., cement, mining minerals).
VidePak’s German W&H extrusion lines stabilize filament production at ±0.05 mm tolerances, ensuring consistent weave density for ISO 9001 compliance .
4. Sustainability: Recyclability and Eco-Friendly Solutions
PP woven bags align with global green initiatives:
- 30% Recycled PP: Reduces carbon footprint by 25% (ISO 14044-certified).
- Oxo-Degradable Additives: Decompose in 3–5 years under ASTM D6954.
- Reusable Designs: FIBC bulk bags withstand 8+ cycles, cutting waste by 40% .
5. VidePak’s Technological Edge
With 100+ Starlinger looms and 30 printing machines, VidePak delivers:
- Customization: 12 Pantone colors, RFID/QR code integration.
- Scalability: 5,000 bags/hour production, supporting JIT global delivery.
- Compliance: Meets EU REACH, FDA 21 CFR, and China GB/T 8946 standards.
Explore our BOPP laminated woven bags for agrochemicals or anti-static FIBCs for flammable powders.
6. FAQs: Addressing Procurement Challenges
Q1: How do I choose between 90 g/m² and 120 g/m² bags?
A: Opt for 90 g/m² for dry goods (e.g., grains); 120 g/m² with lamination suits moisture-sensitive products (e.g., fertilizers).
Q2: Can bags withstand -30°C freezer storage?
A: Yes. Our copolymer PP blends retain flexibility at -40°C (tested per ASTM D746).
Q3: What’s the lead time for custom designs?
A: 15–20 days for orders >10,000 units, including lab testing and logistics coordination.
7. Future Trends: Smart Packaging and IoT Integration
Emerging innovations include:
- Blockchain Tracking: Tamper-proof supply chain logs via embedded NFC tags.
- Self-Healing Films: Microcapsule technology seals <2 mm punctures automatically.
VidePak’s R&D team is piloting solar-reactive inks that display temperature changes for perishable goods.
References
- VidePak Company Profile: https://www.pp-wovenbags.com/
- ASTM International. (2025). Standard Specification for Polypropylene Films.
- EU Circular Economy Action Plan, 2024 Revision.
- Contact: info@pp-wovenbags.com
Anchor Links
This article combines technical rigor, market insights, and VidePak’s 30+ years of expertise to position your operations at the forefront of industrial packaging innovation.