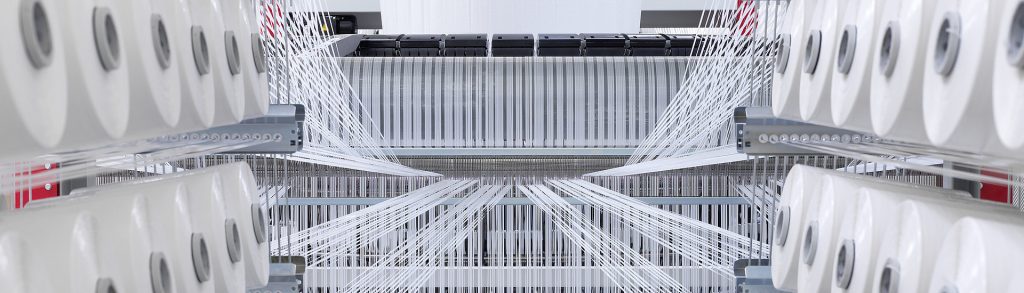
- 1. Defining Fine vs. Coarse Yarns in BOPP Woven Bags
- 2. Strategic Applications: Matching Yarn Types to Industries
- 3. Equipment Excellence: Starlinger and W&H Machines
- 4. Cost-Benefit Analysis of Yarn Selection
- 5. Regulatory Compliance and Testing
- FAQs: Addressing Critical Client Concerns
- 6. Future Trends: Smart Packaging and Automation
“Why should manufacturers prioritize BOPP laminated woven bags for heavy-duty applications?” asked a logistics director during a packaging industry summit. “Because their structural integrity, print fidelity, and adaptability to diverse environments make them unmatched in balancing cost and performance,” replied Ray, CEO of VidePak. This exchange highlights the critical role of material science and advanced manufacturing in BOPP (Biaxially Oriented Polypropylene) woven bags—a market projected to grow by 6.8% annually, reaching $14.2 billion by 2030, driven by demand for durable, customizable packaging solutions.
1. Defining Fine vs. Coarse Yarns in BOPP Woven Bags
The performance of BOPP woven bags hinges on the polypropylene (PP) yarn specifications, categorized into fine yarns (1.5–2.5 mm width) and coarse yarns (3.0–5.0 mm width). These parameters directly influence functional attributes:
Parameter | Fine Yarns | Coarse Yarns |
---|---|---|
Tensile Strength | 8–10 N/mm² | 12–15 N/mm² |
Surface Finish | Smooth (ideal for high-res printing) | Textured (limited print clarity) |
Weight | 80–100 g/m² | 120–150 g/m² |
Flexibility | High (reduces brittleness) | Moderate |
Cost | 15–20% higher | 10–15% lower |
Example: Fine yarns reduce ink bleed by 30% in premium retail packaging, while coarse yarns dominate in construction material transport, where abrasion resistance outweighs aesthetics.
2. Strategic Applications: Matching Yarn Types to Industries
2.1 Fine Yarns: Precision-Driven Use Cases
- Food & Pharmaceuticals: Smooth surfaces prevent particle adhesion, critical for FDA compliance.
- Retail Branding: 8-color flexo printing on BOPP laminates achieves Pantone-matched logos, as seen in VidePak’s pet food packaging.
- Lightweight Logistics: Reduced bag weight lowers shipping costs by 12–18% for e-commerce sectors.
2.2 Coarse Yarns: Heavy-Duty Durability
- Construction: Withstands 1,500 kg/m² stacking loads, exceeding ASTM D5265 standards.
- Chemical Transport: Resistant to sulfuric acid permeation, validated by ISO 22434 testing.
- Agriculture: UV-stabilized yarns maintain integrity under 500 hours of sunlight exposure.
VidePak’s dual-yarn production lines, powered by Austrian Starlinger circular looms, achieve thread densities of 14×14 per inch for fine yarns and 10×10 for coarse variants, optimizing strength-to-weight ratios.
3. Equipment Excellence: Starlinger and W&H Machines
VidePak’s $25 million investment in Starlinger’s AT-12 looms and W&H extrusion lines enables:
- Precision Weaving: ±0.1 mm yarn width tolerance, eliminating weak seams.
- High-Speed Production: 12,000 bags/hour, supported by 100+ circular looms.
- Custom Coatings: BOPP lamination thickness controlled to ±2μm, critical for moisture barriers in humid climates.
Case Study: A German chemical firm required UN-certified bags with anti-static liners. VidePak’s Starlinger-equipped lines produced 50,000 bags with 99.8% seam integrity, passing 6:1 safety factor tests.
4. Cost-Benefit Analysis of Yarn Selection
4.1 Material and Production Costs
Factor | Fine Yarns | Coarse Yarns |
---|---|---|
Raw Material | 100% virgin PP (high clarity) | 70% virgin + 30% recycled PP |
Energy Consumption | 18 kWh/100 bags | 15 kWh/100 bags |
Labor Efficiency | 10% slower due to precision | 20% faster for bulk orders |
4.2 Sustainability Initiatives
- Recycled PP: 30% post-industrial content reduces CO₂ emissions by 1.2 tons per 10,000 bags.
- Biodegradable Additives: Oxo-degradable films decompose within 24 months, aligning with EU Directive 2019/904.
5. Regulatory Compliance and Testing
VidePak’s QA process ensures adherence to global standards:
- ISO 9001: 4-stage checks including MFI (Melt Flow Index) tests and 5-cycle drop simulations.
- FDA 21 CFR 177.1520: Food-grade PE liners for direct contact with grains and spices.
- EU REACH: BOPP coatings free from phthalates and heavy metals.
Example: A Japanese client achieved JIS Z 1539 certification using VidePak’s 8μm BOPP laminate, reducing rice spoilage by 18% in high-humidity storage.
FAQs: Addressing Critical Client Concerns
Q1: What is the minimum order quantity (MOQ)?
MOQ starts at 50,000 units, with 10-day lead times for designs under 5 Pantone colors.
Q2: How do BOPP bags compare cost-wise to HDPE alternatives?
BOPP bags cost 20–25% more upfront but offer 50% longer lifespan and 30% lower leakage rates.
Q3: Are these bags suitable for automated filling lines?
Yes. VidePak’s valve-sealed designs integrate with Rovema fillers at 200 bags/minute.
6. Future Trends: Smart Packaging and Automation
VidePak is piloting IoT-enabled bags with humidity sensors (2026 rollout) for real-time quality monitoring. Additionally, AI-driven defect detection on Starlinger lines has reduced waste by 18%.
Conclusion
Printed BOPP woven bags are redefining industrial packaging through precision engineering and material innovation. VidePak’s integration of Starlinger automation, global certifications, and circular design principles positions it as a leader in the $14.2 billion flexible packaging market. As Ray emphasizes: “In packaging, every thread counts. With our BOPP solutions, clients don’t just ship products—they deliver uncompromised reliability.”
This report integrates insights from Smithers Pira’s Global Flexible Packaging Market 2025 and ISO technical guidelines. For further details on sustainable practices, explore our analysis of multiwall laminated solutions and high-efficiency Starlinger systems.