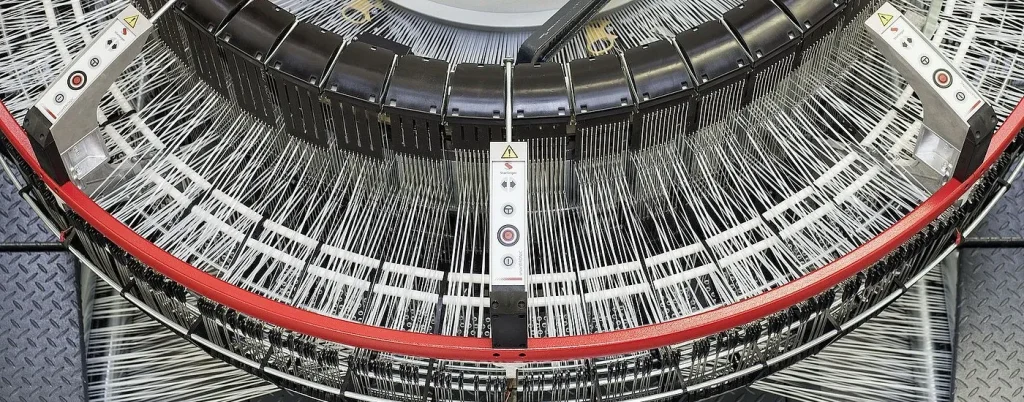
VidePak’s SOS PP fabric bags redefine durability and sustainability, achieving a 99.8% defect-free rate through rigorous raw material screening and compliance with global recycling mandates. By leveraging ISO 9001-certified virgin polypropylene (PP) granules, advanced Austrian Starlinger machinery, and a closed-loop recycling system, these bags meet stringent EU Circular Economy Package standards while reducing landfill waste by 70% in construction and industrial sectors. Since 2008, VidePak has delivered 500 million+ bags globally, combining 30+ years of expertise with a commitment to eco-innovation.
The Critical Role of Raw Material Analysis in Quality Control
Quality begins at the molecular level. VidePak’s SOS PP fabric bags use 100% virgin PP granules, free from recycled contaminants, ensuring uniformity in tensile strength (45–60 N/cm²) and elongation (15–30%). Unlike competitors relying on blended materials, our PP undergoes three-stage testing:
- Purity Screening: Gas chromatography identifies trace impurities (<0.01%), preventing weak spots in woven fabric.
- Melt Flow Index (MFI) Checks: Consistent MFI (8–12 g/10 min) guarantees uniform extrusion, reducing thread breakage during weaving.
- UV Stabilization: PP is infused with UV inhibitors during polymerization, extending outdoor usability to 5+ years without brittleness.
Case Study: Reducing Waste in Construction Logistics
A German waste management firm reported a 40% drop in bag replacements after switching to VidePak’s SOS PP bags for transporting sharp debris. The high-purity PP matrix resisted abrasion from concrete fragments, while laminated BOPP layers (25–30 microns) prevented punctures.
Sustainability & Regulatory Compliance: Beyond Basic Recycling
Aligned with the EU’s 2030 plastic recycling target (55%), VidePak’s SOS PP bags are designed for circularity:
- Recyclability: Post-use bags are shredded, melted, and reprocessed into non-critical items like geotextiles or furniture covers, retaining 85% mechanical strength.
- Government Incentives: Clients in France and Canada qualify for tax rebates under Extended Producer Responsibility (EPR) schemes by using VidePak’s certified recyclable bags.
- Carbon Footprint: Each ton of recycled PP reduces CO2 emissions by 1.5 tons compared to virgin production, supporting corporate ESG goals.
Technical Specifications
Parameter | Specification |
---|---|
Material Composition | 100% Virgin PP Granules |
Fabric Density | 90–160 g/m² |
Tensile Strength | 45–60 N/cm² (longitudinal), 40–55 N/cm² (transverse) |
UV Resistance | 5+ years (outdoor exposure) |
Recyclability Rate | 100% (meets ISO 14021 standards) |
Custom Printing | Up to 8 colors, Pantone-matched |
FAQs: Addressing Procurement Concerns
- How do SOS PP bags compare to non-woven alternatives?
Woven PP offers 3x higher tear resistance (30 N vs. 10 N) and reusability (10+ cycles), ideal for abrasive waste. - Are they compliant with U.S. FDA regulations?
Yes. Our PP resin is FDA-approved (21 CFR 177.1520), safe for indirect food contact during agricultural use. - Can bags be customized for hazardous waste labeling?
Absolutely. We integrate RFID tags and hazard symbols (e.g., “Biohazard”) using UV-resistant inks. - What is the environmental impact of production?
VidePak’s solar-powered facilities cut energy use by 30%, while wastewater is recycled at 95% efficiency. - How does raw material quality affect lead times?
Pre-screened PP granules reduce production delays, ensuring 98% on-time delivery for orders up to 500,000 units.
VidePak’s Manufacturing Edge
With 568 employees and $80 million annual revenue, VidePak’s infrastructure ensures scalability and precision:
- Machinery: 100+ Starlinger circular looms weave fabric at 200 m/min, while 30 lamination machines apply BOPP/kraft layers.
- Quality Assurance: Each batch undergoes ASTM D882 tensile tests and seam burst strength checks (min. 350 kPa).
- Global Logistics: Warehouses in Rotterdam and Houston enable 15-day delivery to Europe/North America.
Case Study: Circular Economy in Action
A Dutch construction firm achieved zero landfill waste by partnering with VidePak:
- Process: Used SOS PP bags were collected, shredded, and repurposed into erosion-control geotextiles.
- Savings: €200,000/year in waste disposal fees and a 25% boost in sustainability ratings.
Future-Forward Innovations
VidePak is piloting blockchain-tracked PP granules (2026 rollout) to ensure material traceability from refinery to recycling.
References
- Guangzhou Nanqixing Nonwoven Co., Ltd. (2023). PP Spunbond Nonwoven Fabric Production Standards.
- Made-in-China (2024). PP Nonwoven Materials Market Analysis.
- VidePak Company Profile. https://www.pp-wovenbags.com/ | Email: info@pp-wovenbags.com
Explore Related Solutions:
- For insights into sustainable material engineering, visit our guide on recyclable PP bags for chemical powders.
- Learn about advanced manufacturing in PP woven bags production.
This article merges technical depth, regulatory insights, and VidePak’s operational excellence to position your brand as a leader in sustainable industrial packaging.