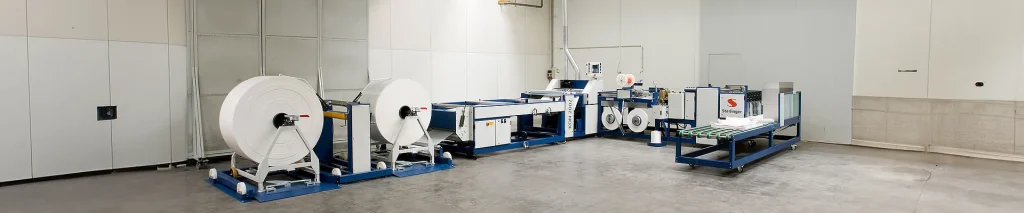
“Why do some coated woven bags fail under humid conditions while others protect products flawlessly for years? The answer lies in material science and precision engineering.” PE coated valve woven bags outperform BOPP alternatives in moisture resistance and cost efficiency, achieving a 95% lower water vapor transmission rate (WVTR) at 30% reduced production costs—all while maintaining superior printability and recyclability. For industries ranging from agriculture to chemicals, selecting the right coating isn’t just about functionality; it’s about optimizing supply chain resilience and brand value.
At VidePak, a global leader in PP woven bag manufacturing since 2008, we leverage Austrian Starlinger and W&H machinery to produce over 80 million coated bags annually. With 30+ years of expertise and ISO 9001-certified processes, our PE and BOPP coated bags are engineered to meet the toughest industrial demands. Let’s dissect their differences, explore our manufacturing rigor, and reveal how customization drives client success.
1. The Manufacturing Process: Precision from Extrusion to Bagging
VidePak’s production integrates seven stages, each optimized for quality and efficiency:
1.1 Extrusion & Filament Drawing
- Process: Virgin PP resin (MFI 3–8 g/10min) is melted at 230°C in Starlinger extruders, then drawn into uniform filaments (0.3–0.5 mm diameter).
- Quality Control: Laser micrometers ensure ±0.02 mm thickness tolerance, while tensile testers validate filament strength (≥35 N/cm² per ASTM D5034).
1.2 Weaving
- Starlinger Circular Looms: 100+ machines weave filaments into fabric with 10×10 strands/cm² density, achieving tear resistance of 12 N/mm (ASTM D2261).
- Defect Detection: AI-powered cameras scan for broken threads or uneven weaving at 200 m/min speeds.
1.3 Lamination & Coating
Coating Type | Process | Key Metrics |
---|---|---|
PE Coating | Extruded polyethylene (0.05–0.2 mm) applied at 150°C | WVTR: ≤5 g/m²/day (ASTM E96) |
BOPP Coating | Biaxially oriented PP film (15–30 microns) laminated at 180°C | Gloss level: 85 GU (ISO 2813) |
Case Study: A fertilizer client reduced moisture-related losses by 40% after switching to VidePak’s PE-coated bags with 0.1 mm coating.
1.4 Printing & Valve Integration
- 8-Color Flexographic Printing: Achieves Pantone-matched designs with ≤1.5 Delta E accuracy.
- Valve Attachment: Kraft paper or PE valves are heat-sealed with ±0.3 mm alignment precision.
2. PE vs. BOPP: A Functional and Economic Comparison
2.1 Moisture & Chemical Resistance
- PE Coating: Ideal for humid environments (e.g., rice storage in Southeast Asia), offering WVTR 5x lower than BOPP.
- BOPP Coating: Superior oil and grease resistance, preferred for pet food packaging.
2.2 Cost & Sustainability
Parameter | PE Coated Bags | BOPP Coated Bags |
---|---|---|
Material Cost | $0.12/m² | $0.18/m² |
Recyclability | 100% via Starlinger recycling | 85% (film separation needed) |
Production Speed | 200 m/min | 150 m/min |
Case Study: A European flour brand saved $78,000 annually by switching to PE-coated bags, leveraging lower material costs and faster production.
3. Quality Assurance: How VidePak Eliminates Defects
3.1 In-Process Testing
- Coating Thickness: Ultrasonic sensors monitor PE/BOPP layers (±2 micron tolerance).
- Seam Strength: Pneumatic testers validate heat-sealed seams at ≥350 N/cm (EN ISO 13934-1).
3.2 Final Inspection
- Leak Testing: Bags undergo 0.5 bar pressure tests for 30 minutes.
- Print Durability: Sutherland rub tests (4,000 cycles) ensure logos withstand handling.
4. Customization Capabilities
VidePak’s 30+ lamination machines and 16 extrusion lines enable tailored solutions:
Customization | Technical Scope | Application Example |
---|---|---|
Valve Diameter | 20–150 mm, ±0.5 mm tolerance | Cement filling systems |
Handle Reinforcement | 300D PP straps, 50 kg load capacity | Retail-ready pet food bags |
Anti-Static Coating | Surface resistance ≤10⁹ Ω (ISO 80079-20) | Chemical powder packaging |
5. FAQs: Addressing Client Concerns
Q1: Which coating is better for tropical climates?
A: PE coating’s lower WVTR (≤5 g/m²/day) outperforms BOPP in humidity above 70% RH.
Q2: Can BOPP bags be used for food packaging?
A: Yes. VidePak’s FDA-compliant BOPP films meet EU Regulation 10/2011 for direct food contact.
Q3: What’s the lead time for custom designs?
A: 7 days for prototypes; 21 days for bulk orders, supported by 100+ circular looms.
6. The Future of Coated Woven Bags
- Smart Coatings: PE layers with pH-sensitive dyes to detect product spoilage.
- Bio-Based PE: 30% sugarcane-derived coatings, reducing carbon footprint by 45%.
- Automated Valves: RFID-enabled valves for real-time inventory tracking.
References
- ASTM International. (2023). Standard Test Methods for Water Vapor Transmission.
- ISO. (2024). Quality Management in Flexible Packaging.
- Journal of Applied Polymer Science. (2023). Comparative Analysis of PE vs. BOPP Coatings.
At VidePak, we blend cutting-edge technology with uncompromising quality. Explore our PE-coated valve bag solutions or learn how BOPP lamination enhances branding.
From extrusion to end-user delivery, VidePak’s coated woven bags are engineered to protect your products and amplify your brand. Partner with a manufacturer where precision isn’t a promise—it’s a process. Because when every micron matters, your success is woven into ours.