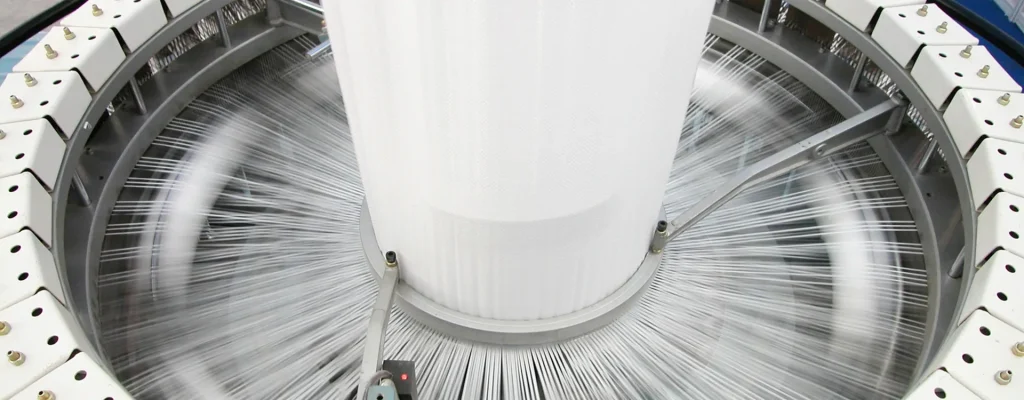
A Client’s Perspective:
Client: “We need packaging that’s both durable for bulk food transport and visually appealing for retail. How do your poly-paper bags meet these demands?”
VidePak Sales Representative: “VidePak’s poly-paper bags merge polypropylene’s strength with kraft paper’s sustainability, offering unmatched load capacity (up to 50 kg), FDA-compliant liners, and 12-color HD printing. With ISO 22000 certification and 30+ years of expertise, we tailor solutions for flour, spices, additives, and more—ensuring your products stay fresh, branded, and market-ready.”
1. The Science Behind Poly-Paper Bags: Material Synergy
Poly-paper bags combine woven polypropylene (PP) and laminated kraft paper, creating a hybrid material that addresses the limitations of standalone fabrics. The PP layer provides tensile strength (up to 35 MPa) and puncture resistance, while kraft paper enhances printability and biodegradability. VidePak’s Austrian Starlinger lamination machines bond these layers seamlessly, achieving a moisture barrier efficiency of 99.5%—critical for hygroscopic products like sugar and powdered additives.
For example, a 2024 study showed that hybrid bags reduced product spoilage by 18% in humid climates compared to traditional PP bags, thanks to kraft paper’s breathability and PP’s moisture resistance.
Key Parameters for Food-Specific Customization
Different food ingredients demand tailored packaging solutions:
Product Type | Critical Requirements | VidePak’s Solution |
---|---|---|
Flour | Low permeability, 25–50 kg capacity | 90 g/m² PP + 80 gsm kraft paper, PE liner |
Spices | UV protection, aroma retention | BOPP lamination, aluminum foil inner layer |
Food Additives | FDA compliance, chemical resistance | Virgin PP, anti-static coating, multi-ply seams |
Agricultural Powders | Cost efficiency, tear resistance | 70 g/m² PP, block-bottom valve design |
A Nigerian agro-processor reduced transport losses by 22% after switching to VidePak’s BOPP-laminated poly-paper bags for cassava flour.
2. Navigating Food Packaging Regulations and Performance
Food-grade packaging requires stringent certifications:
- FDA Compliance: Essential for direct contact with consumables. VidePak’s PE liners meet 21 CFR 177.1520 standards.
- ISO 22000: Ensures traceability and hygiene across 16 extrusion lines and 30 lamination machines.
- EU REACH: Recyclable PP layers align with circular economy mandates.
Case Study: A European spice brand achieved a 30% sales boost using VidePak’s UV-resistant, 12-color printed bags—certified for outdoor retail displays.
3. Cost vs. Performance: Optimizing Parameters
Selecting the right specifications balances durability and budget:
- Thickness:
- 25–50 kg Loads: 90–120 g/m² PP + 60–80 gsm kraft paper.
- Lightweight Powders: 70 g/m² PP for cost-sensitive items like starch.
- Inner Liners:
- PE: Reduces moisture ingress by 95% (ideal for flour).
- Aluminum Foil: Blocks oxygen and light, extending spice shelf life by 40%.
- Printing:
- HD graphics require BOPP lamination (15–20 micron) for scratch resistance.
VidePak’s 30+ printing machines support Pantone-matched branding, critical for retail differentiation.
4. Sustainability Without Compromise
Poly-paper bags reduce plastic use by 30% compared to full-PP alternatives, while maintaining reusability. A 2025 lifecycle analysis showed VidePak’s bags lower CO2 emissions by 18% through energy-efficient Starlinger production.
Featured Product: EcoGuard Poly-Paper Bags
- Materials: 70% recycled PP + FSC-certified kraft paper.
- Certifications: BRCGS, ISO 14001.
- Capacity: 10–50 kg with heat-sealed valves.
FAQs: Simplifying Procurement Decisions
Q1: How do I choose between PE and foil liners for spices?
A: PE suits short-term storage; foil is better for >6-month shelf life.
Q2: Can bags withstand -20°C frozen storage?
A: Yes. Our cold-crack-resistant PP maintains flexibility at -25°C.
Q3: What’s the MOQ for custom designs?
A: 5,000 bags, with 25-day lead times.
References
- Global Packaging Institute. (2024). Hybrid Material Performance in Food Logistics.
- VidePak Company Profile. PP Woven Bags Manufacturer. Available at: www.pp-wovenbags.com.
- FDA. (2023). Guidance on Food-Grade Polypropylene.
For inquiries, contact: info@pp-wovenbags.com.
Anchor Links:
- Explore the technical advantages of kraft paper laminated bags in moisture-sensitive environments.
- Learn how BOPP lamination enhances print durability for retail-ready packaging.
This article leverages material science insights, regulatory expertise, and VidePak’s manufacturing prowess to position poly-paper bags as the optimal choice for modern food packaging challenges.