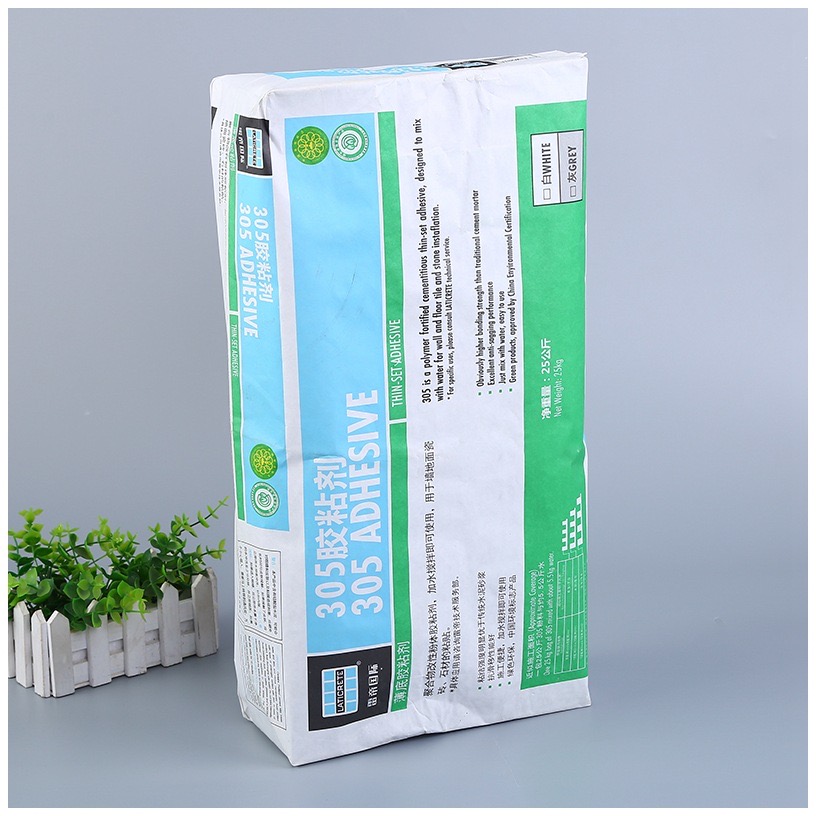
When it comes to packaging solutions, particularly in industries that deal with chemicals, food, or construction materials, the integrity of the bag’s protection properties is crucial. Among the most sought-after features for woven bags are moisture and waterproofing capabilities. Two terms often come up in the context of packaging bags—Moisture Proof Woven Bags and Waterproof Woven Bags. But what exactly differentiates these two, and which one is more effective? Additionally, how do modern manufacturing techniques, like those from Starlinger and W&H, enhance the quality of these bags?
In this article, we will dive into the differences between Moisture Proof and Waterproof Woven Bags, the materials and features that make them effective, and how advanced equipment is improving the production of these packaging solutions. Let’s explore how these bags play a critical role in industries across the globe.
The Difference Between Moisture Proof Woven Bags and Waterproof Woven Bags
To understand the key differences between Moisture Proof Woven Sacks and Waterproof Woven Bags, it’s essential to first define what each term means in the context of packaging materials.
1. Moisture Proof Woven Bags
Moisture Proof Woven Bags are designed to resist the penetration of moisture but are not necessarily fully impermeable to water. These bags typically feature an outer woven polypropylene (PP) structure, which acts as a barrier against water vapor and humidity. While these bags will protect their contents from mild environmental conditions like humidity or light rain, they may not perform well when exposed to heavy or continuous water immersion.
2. Waterproof Woven Bags
On the other hand, Waterproof Woven Bags are manufactured to completely prevent any water or liquid from penetrating the bag. These bags often feature additional protective layers, such as PE (polyethylene) coatings, or multi-layered laminations that form an impermeable barrier. Waterproof Woven Bags are ideal for industries where exposure to water or liquid is a concern, like in the transportation of chemicals, fertilizers, or food products.
Feature | Moisture Proof Woven Bags | Waterproof Woven Bags |
---|---|---|
Water Resistance | Resists moisture but not waterproof | Completely impermeable to water |
Typical Uses | Packaging of dry materials, food, chemicals | Used for products requiring full protection from water |
Durability | Suitable for mild environmental conditions | Stronger in harsh, wet conditions |
Construction Materials | Woven PP, sometimes with a PE liner | Woven PP with PE or multiple coatings |
Common Applications | Food storage, chemicals, agricultural products | Construction materials, bulk liquids, fertilizers |
As seen in the table, Moisture Proof PP Bags are excellent for environments with moderate humidity, while Waterproof Woven Bags provide a higher level of protection, making them suitable for harsher, more water-exposed conditions.
Which One Offers Stronger Functionality?
When comparing Moisture Proof Woven Bags and Waterproof Woven Bags, it’s clear that the latter offers more robust protection in terms of liquid and water resistance. However, this enhanced protection comes at a higher cost due to the extra layers and coatings required to make the bags waterproof.
For industries that do not require full water protection but are still concerned about humidity or occasional exposure to moisture, Moisture Proof Woven Sacks might be a better and more cost-effective option. These bags offer sufficient protection for many products, such as grains, fertilizers, and textiles, without the need for the extra layers involved in waterproof bags.
Conversely, industries such as construction, shipping of bulk liquids, and agricultural chemicals would benefit more from the enhanced protection provided by Waterproof Woven Bags, especially when dealing with sensitive materials that cannot tolerate any exposure to water.
Advanced Technology for Superior Bag Quality
In the modern packaging industry, the use of cutting-edge manufacturing technology plays a pivotal role in improving product consistency, strength, and performance. For example, VidePak uses advanced equipment from industry leaders such as Starlinger and W&H. These machines help in producing woven bags with a high degree of accuracy in terms of bag construction, consistency of thread width and thickness, and lamination processes.
By employing such technologies, the woven fabric’s surface is smoother and more uniform. This not only enhances the bags’ appearance and tactile qualities but also contributes to their overall durability and functionality. Here’s how:
- Precision Weaving: Modern weaving technology allows for very consistent fabric construction, minimizing inconsistencies that might weaken the bag or create areas where moisture or water could seep through.
- Lamination and Coating: The lamination process provides an additional layer of protection that enhances the strength of the woven fabric. For moisture-proof or waterproof bags, this can mean adding a polyethylene coating or other multi-layered films to make the bags either moisture resistant or fully waterproof.
- Quality Control: With high-tech systems for quality control, each woven bag can be checked for defects such as uneven weaves, inconsistencies in coating thickness, or pinholes that may compromise its moisture resistance.
VidePak’s Commitment to Quality and Innovation
At VidePak, we utilize the latest equipment from Starlinger and W&H to create high-quality woven bags that meet the diverse needs of our customers. Whether it’s a Moisture Proof Woven Bag or a Waterproof Woven Bag, the attention to detail in the manufacturing process ensures that each bag provides optimal protection for its contents.
Our bags are designed with precision, so the fabric structure is uniform, providing superior protection for the stored products. The smoothness of the woven fabric also contributes to better printability, allowing for branding and product labeling without compromising the bag’s protective qualities.
Applications of Moisture Proof and Waterproof Woven Bags
Let’s explore some common use cases for both types of bags:
- Moisture Proof Woven Bags:
- Food Packaging: Ideal for grains, powdered food items, and other dry food materials that need protection from humidity.
- Agricultural Products: Protects fertilizers and seeds during storage and transport in environments where humidity may be present.
- Chemical Packaging: Some chemicals require moisture resistance but not full water protection.
- Waterproof Woven Bags:
- Construction: Often used to package materials that could be exposed to rain or snow, like sand, cement, or aggregates.
- Bulk Liquid Transport: Packaging materials that need full water resistance for liquids, like chemicals, oils, and fertilizers.
- Waste Management: Often used for packaging waste or hazardous materials, ensuring there is no leakage or contamination from external elements.
Conclusion
While both Moisture Proof Woven Bags and Waterproof Woven Bags serve important functions in protecting goods from external elements, the key difference lies in their level of water resistance. Moisture Proof Woven Bags offer great protection against humidity and light rain, making them suitable for many industries. In contrast, Waterproof Woven Bags are ideal for harsher environments where water exposure is a concern.
With the help of advanced equipment like Starlinger and W&H, VidePak produces high-quality woven bags that excel in durability, consistency, and functionality, ensuring that your packaging solution meets the most stringent protection requirements.
For more insights on Moisture Proof Woven Bags, click here, or explore our offerings on Moisture Proof Woven Sacks and Moisture Proof PP Bags to understand how we can meet your packaging needs.
Helpful Links: