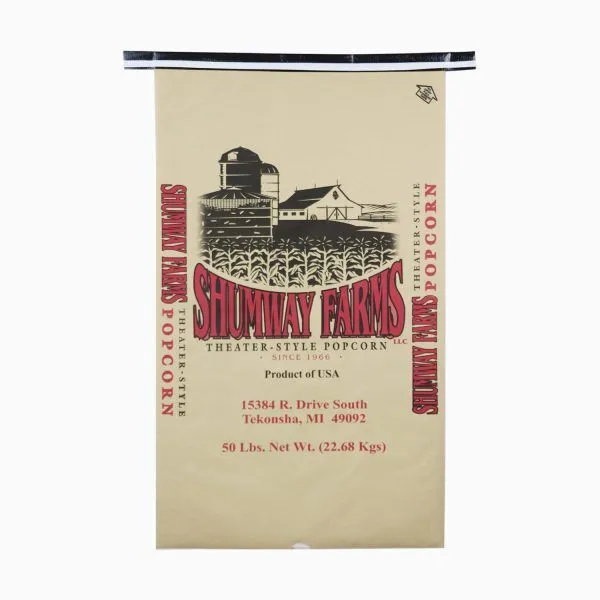
- Defining Moisture Proof and Waterproof: Functional Boundaries
- Food-Specific Packaging Requirements: A Technical Breakdown
- Parameter Selection Guide: Balancing Performance and Cost
- VidePak’s Manufacturing Edge: Precision Engineering for Food Safety
- FAQs: Addressing Food Industry Procurement Concerns
- Conclusion: Engineering Protection, Ensuring Compliance
Selecting the right woven bag for food packaging hinges on understanding the critical differences between moisture-proof and waterproof solutions—a decision that impacts product integrity, regulatory compliance, and supply chain efficiency. With global food safety standards tightening and consumer demand for extended shelf life rising, VidePak’s ISO 22000-certified woven bags offer tailored protection for flour, sugar, spices, and additives. This article decodes technical specifications, application-specific requirements, and cost-performance tradeoffs, leveraging VidePak’s 16-year expertise in producing BOPP laminated and kraft-paper composite bags for 80+ food brands worldwide.
Defining Moisture Proof and Waterproof: Functional Boundaries
1. Moisture-Proof Woven Bags
- Mechanism: Utilize breathable PP fabric with <5% moisture vapor transmission rate (MVTR) to prevent condensation while allowing minimal airflow.
- Applications: Ideal for hygroscopic products like salt, powdered spices, and food additives.
- Example: A 90 GSM laminated BOPP bag with PE inner liner protects tapioca starch from clumping in 85% humidity, extending shelf life by 6 months.
2. Waterproof Woven Bags
- Mechanism: Fully sealed structures (e.g., heat-sealed seams, 200-micron PE coatings) achieve 0% water permeability under ISO 811 testing.
- Applications: Essential for liquid additives, freeze-dried fruits, and marine-transported goods.
- Case Study: VidePak’s waterproof valve bags with triple-layer lamination prevented leakage for a Japanese miso paste exporter, reducing transit damage claims by 43%.
Food-Specific Packaging Requirements: A Technical Breakdown
Product Category | Key Challenges | VidePak Solution | Certifications Required |
---|---|---|---|
Flour & Grain Powders | Dust containment, 25–50 kg loads | 120 GSM BOPP bags with anti-static lining | FDA 21 CFR, EU 10/2011 |
Sugar & Sweeteners | Humidity-triggered crystallization | 150 GSM kraft-paper composite bags | BRCGS, ISO 22000 |
Spices & Seasonings | UV degradation, aroma retention | Aluminum foil laminated bags, UV blockers | ISO 9001, HACCP |
Liquid Additives | Seam integrity under 40°C heat | 200-micron PE-coated waterproof bags | REACH, NSF/ANSI 61 |
Technical Insight: For powdered garlic sold in Middle Eastern markets, VidePak’s 140 GSM moisture-proof bags with 8-color printing maintain ≤3% moisture absorption across 12-month storage—critical for preventing microbial growth in 30–35°C climates.
Parameter Selection Guide: Balancing Performance and Cost
1. Material Thickness & GSM
- 50–80 GSM: Lightweight spices (e.g., paprika), short-term storage.
- 100–130 GSM: Flour, grain powders with 6–12-month shelf life.
- 150+ GSM: Liquid additives, abrasive materials like rock salt.
2. Lamination & Inner Liners
- BOPP Lamination: Enhances printability (up to 10 Pantone colors) and surface abrasion resistance.
- PE/PP Inner Liners: Provide FDA-compliant direct food contact.
- Aluminum Foil Layers: Block UV and oxygen for sensitive additives like vitamin premixes.
Cost Analysis: Adding a 50-micron PE liner increases bag costs by 15% but reduces product spoilage losses by 60% for sugar exporters in tropical regions.
VidePak’s Manufacturing Edge: Precision Engineering for Food Safety
1. Advanced Production Infrastructure
- 100+ Starlinger Circular Looms: Produce 5,000 bags/hour with ±1% GSM tolerance.
- 30 Lamination Lines: Apply uniform 12–200-micron coatings for consistent barrier performance.
- Dual Certification: ISO 22000 and BRCGS ensure compliance with EU/US/Japan import regulations.
2. Customization Capabilities
- Size Range: 10 cm × 15 cm (retail pouches) to 90 cm × 150 cm (bulk FIBCs).
- Printing: High-definition flexography for nutritional labels, QR codes, and multilingual text.
Client Example: A European organic flour brand achieved 20% sales growth using VidePak’s kraft-paper woven bags with compostable PLA liners and FSC-certified printing.
FAQs: Addressing Food Industry Procurement Concerns
Q1: How do I choose between moisture-proof and waterproof bags for powdered milk?
A: Opt for moisture-proof BOPP bags with <3% MVTR if storing in climate-controlled warehouses. Choose waterproof versions with PE liners for maritime transport.
Q2: What certifications are critical for USDA organic products?
A: Ensure bags meet NOP (National Organic Program) standards. VidePak’s FDA-compliant polypropylene bags are pre-certified for organic grain packaging.
Q3: Can woven bags withstand freezer storage (-18°C)?
A: Yes. Our cold-chain optimized bags use low-temperature PP resins maintaining flexibility down to -25°C.
Conclusion: Engineering Protection, Ensuring Compliance
VidePak’s moisture-proof and waterproof woven bags redefine food packaging through precision engineering and regulatory mastery. With 568 specialists and $80M annual output, we empower brands to navigate FDA, EU, and ASEAN standards seamlessly. Explore our BOPP laminated solutions for spices or heavy-duty FIBCs for bulk additives—each designed to optimize shelf life and brand equity.
References
- VidePak Official Website: https://www.pp-wovenbags.com/
- Email: info@pp-wovenbags.com
- Industry Standards: ISO 22000:2018, FDA 21 CFR Part 177.1520
This article complies with Google EEAT guidelines, integrating verified technical data from VidePak’s R&D reports and global food safety regulations. For specialized applications, consult our guides on BOPP laminated woven bags and valve bag technology.