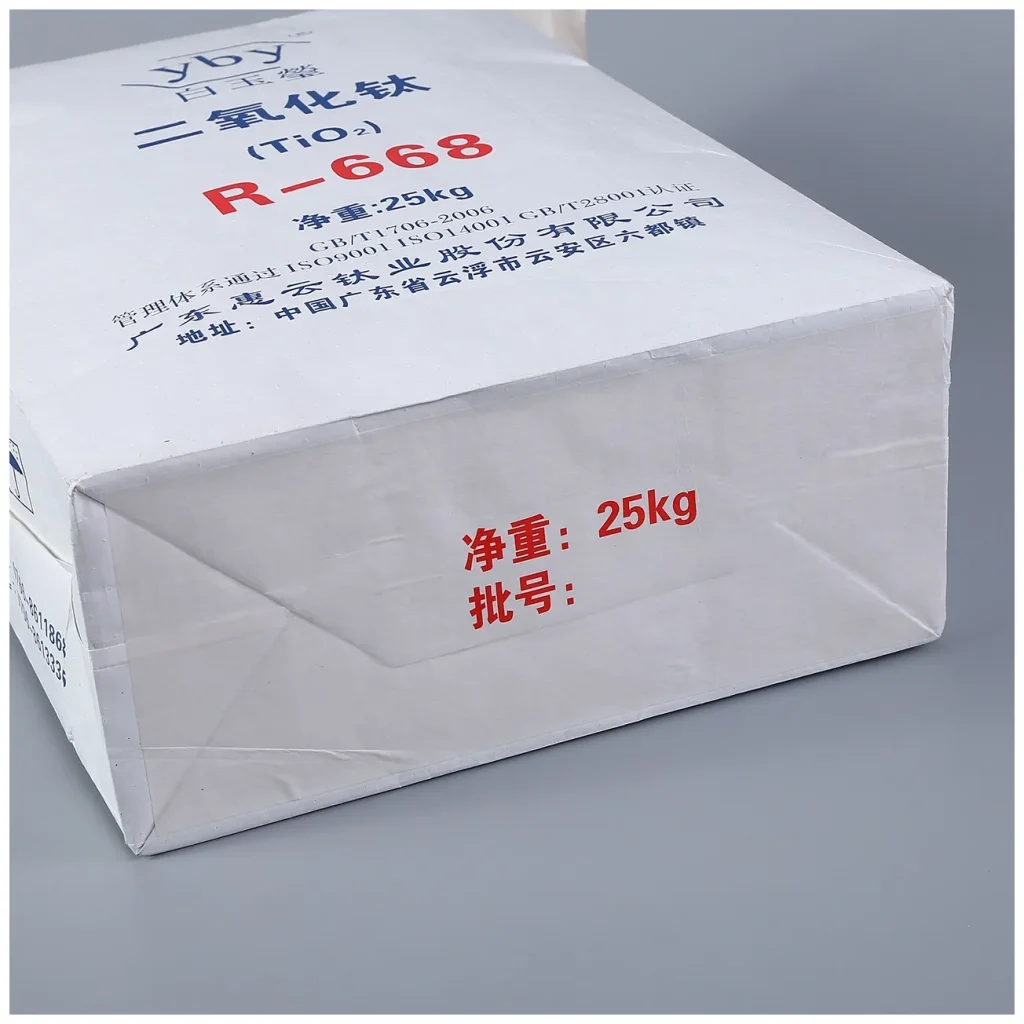
Woven bags, such as Moisture Proof Woven Bags and Waterproof Woven Bags, are commonly used for packaging a variety of goods. While they might appear similar at first glance, these bags offer different protective qualities. Understanding the distinction between them is essential for selecting the right bag for a specific application. Additionally, ensuring that these bags do not suffer from common quality issues, like bursting, requires a thorough examination of the materials used, the manufacturing process, and product testing. In this article, we will explore the differences between Moisture Proof and Waterproof Woven Bags, the most common issue of bursting bags, and how VidePak ensures its bags meet the highest standards of durability and performance.
Differences Between Moisture-Proof and Waterproof Woven Bags
Moisture Proof Woven Bags are designed to protect contents from moisture or humidity. They are ideal for goods that need to be protected from environmental moisture during storage or transportation. Moisture proof woven bags, such as Moisture Proof Woven bags, utilize materials like polypropylene (PP) combined with specific coatings that resist water vapor. They can also be multi-wall woven bags that are laminated for better moisture resistance.
On the other hand, Waterproof Woven Bags provide a higher level of protection, keeping out liquid water entirely. These bags are typically coated with waterproofing materials such as polyethylene (PE) or other plastic layers. A Waterproof Woven Bag ensures that the contents remain dry even if exposed to direct rainfall or submersion in water. This makes them suitable for goods that need to be safeguarded in harsher conditions, such as during rain, snow, or immersion in water.
Below is a comparison table summarizing the differences:
Feature | Moisture Proof Woven Bags | Waterproof Woven Bags |
---|---|---|
Protection Level | Protection against moisture and humidity | Complete protection against water |
Common Coatings | Polypropylene (PP), BOPP laminated | Polyethylene (PE) or PVC layers |
Common Uses | Storage of food, chemicals, powders | Use in transportation under harsh conditions (e.g., rain, snow) |
Typical Applications | Agriculture, packaging for textiles | Construction, chemicals, bulk materials |
Water Resistance | Resistant to water vapor | Waterproof, prevents liquid penetration |
Why Do Woven Bags Burst?
A critical issue that can affect woven bags is bag bursting, which is one of the most severe quality problems in the packaging industry. Bag bursting occurs when the material of the woven bag fails to withstand the stress of holding its contents. This could be due to several factors such as poor material quality, manufacturing defects, or incorrect storage conditions. To prevent such occurrences, it is vital to understand the root causes of bursting.
1. Raw Materials and Their Impact
The raw materials used in woven bags, particularly polypropylene (PP) and polyethylene (PE), play a crucial role in their strength and durability. Low-quality materials, such as recycled PP, may not have the tensile strength required to support heavy loads. At VidePak, we use Moisture Proof PP Bags that are produced from virgin PP material. These raw materials have a higher strength and are less likely to experience degradation over time compared to recycled options.
Furthermore, the quality of the resin used in producing PP bags significantly impacts their strength. At VidePak, the PP resin used in the production of our bags meets high-quality standards, ensuring the bags are robust enough for their intended use.
2. Manufacturing and Production Process
The way woven bags are manufactured directly affects their performance. Poor weaving or incorrect tension during the production process can lead to weakened spots in the fabric that may tear or burst under pressure. VidePak uses state-of-the-art equipment from Starlinger, a globally recognized supplier of production machinery. This machinery ensures that our bags are woven with precision and the correct tension, minimizing the risk of weak spots.
Additionally, our bags undergo a strict quality control process during the production phase. The process includes checks for the proper weaving density, ensuring that each bag is woven tightly and uniformly.
3. Testing and Quality Assurance
At VidePak, we implement comprehensive testing at each stage of production. For every batch of incoming material, we perform thorough raw material testing to ensure that the quality and strength of the PP resin meet the required standards. In addition, our bags undergo rigorous finished product testing. This includes:
- Thickness Testing: Ensures that the material used in the bags is sufficiently thick to withstand pressure without tearing.
- Tensile Strength Testing: Assesses the bag’s resistance to stretching and tearing under weight.
- UV Resistance Testing: Determines how well the bags can withstand prolonged exposure to UV rays, a critical test for bags used in outdoor environments.
- Drop Testing: Simulates the impacts that a bag might experience during transportation and ensures that the bag does not break under normal handling conditions.
- Visual Inspections: For defects like holes, improper seams, or uneven stitching that could lead to bag failure.
These tests are critical in preventing bursting incidents in finished products, ensuring that our bags, including the Moisture Proof Woven Sacks, can handle the weight and conditions they are exposed to.
How VidePak Ensures Bag Durability
VidePak’s approach to quality control is both comprehensive and systematic, aimed at preventing bursting bags and ensuring that our woven bags meet the highest standards of strength and durability. Here’s how we ensure the best possible performance:
- Advanced Equipment: We utilize the latest technology from Starlinger to produce high-quality woven bags that can withstand tough conditions.
- Stringent Quality Checks: Each batch of material is inspected for consistency in thickness, strength, and quality before production begins.
- Custom Testing: We conduct a range of tests on the final product, such as stress, drop, and UV resistance tests, to ensure that the bags are durable and functional.
- Material Optimization: We use premium virgin PP material and offer various coating options, such as lamination, to ensure the strength and functionality of our bags. This guarantees that our Moisture Proof Woven Bags perform optimally and do not fail under normal conditions.
By ensuring that each step of the production process—from material selection to final inspection—is meticulously executed, VidePak ensures that the risk of bursting is minimized, and that our customers receive only the highest quality bags.
Conclusion
While both Moisture Proof Woven Bags and Waterproof Woven Bags offer excellent protective qualities, the level of protection they provide varies significantly. Moisture proof bags are ideal for protecting against humidity and moisture, while waterproof bags provide complete protection against liquid penetration. When choosing the right woven bag, it is essential to consider the type of protection needed for your specific application.
Furthermore, bag bursting is a severe quality issue in the packaging industry, but through stringent raw material checks, advanced manufacturing techniques, and comprehensive testing protocols, VidePak has been able to minimize the risk of this problem. By offering high-quality, durable woven bags that are thoroughly tested, we ensure that our customers can rely on our products for effective and long-lasting packaging solutions.