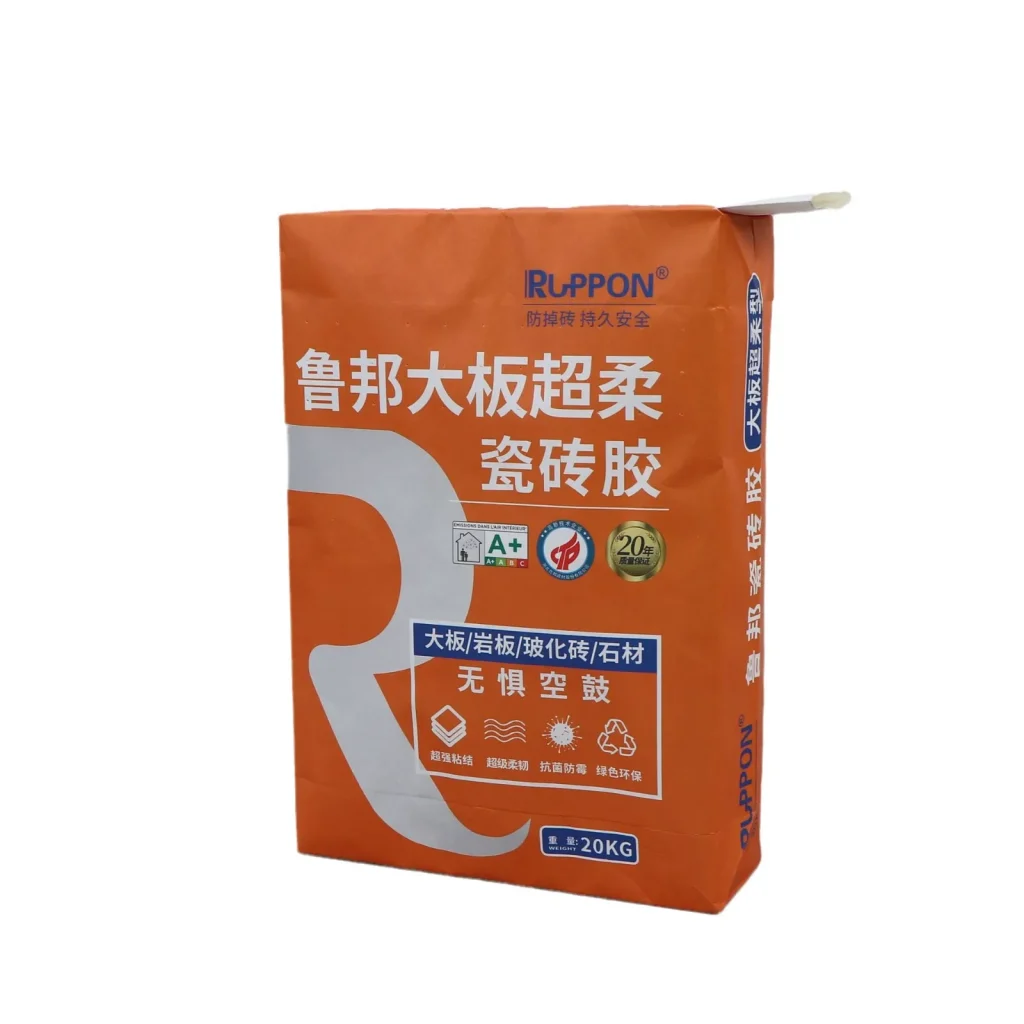
BOPP laminated valve woven bags are revolutionizing industrial packaging by combining durability, efficiency, and safety—three pillars that define VidePak’s commitment to delivering high-performance solutions. With over 30 years of industry expertise and a global footprint spanning 80+ countries, VidePak produces 50 million BOPP laminated valve bags annually, designed to meet stringent ISO 9001 and FDA standards while reducing logistics costs by up to 25%.
1. The Structural Superiority of BOPP Laminated Valve Bags
Biaxially Oriented Polypropylene (BOPP) laminated valve bags are engineered for industries requiring precision, from chemicals to agriculture. Their design integrates three critical elements:
A. Valve Mechanisms for Streamlined Filling
The valve design eliminates manual handling during filling, enabling automated processes that reduce labor costs and contamination risks. VidePak’s block-bottom valve bags feature reinforced seams and precision-cut valves (8–12 cm diameters) to accommodate high-speed filling equipment, ensuring up to 1,200 bags/hour throughput[citation:19][citation:44].
Example: A South American fertilizer manufacturer reduced spillage by 30% after switching to VidePak’s valve bags, which support pneumatic filling systems for granular and powdered materials.
B. Block-Bottom Design for Stability
Unlike traditional flat-bottom bags, block-bottom (square-base) configurations enhance stacking stability, enabling 20% higher palletization density. This design is critical for transporting hygroscopic materials like cement or resins, where moisture resistance (achieved through 18–30 micron BOPP lamination) is paramount[citation:44].
2. Operational Benefits: Efficiency Meets Customization
VidePak’s valve bags are tailored to optimize supply chains:
A. Load Capacity and Durability
Parameter | Specification Range |
---|---|
Material | 100% Virgin PP + BOPP Film |
Thickness | 90–150 GSM |
Load Capacity | 25–50 kg |
Valve Types | Pasted, Block-Bottom, Gusseted |
Printing Colors | Up to 8 (Pantone, CMYK, RAL) |
Case Study: A European chemical company reported zero bag ruptures during transit after adopting VidePak’s 150 GSM BOPP bags with 12×12 weave density, capable of withstanding 5,000 N tensile strength[citation:19].
B. Customization for Branding and Compliance
VidePak’s 30+ printing machines support full-surface branding, including QR codes for traceability and safety labels compliant with UN/ISO regulations. For instance, UV-resistant inks maintain legibility in outdoor storage for 2+ years, a feature critical for hazardous material transport in Africa[citation:44][citation:49].
3. Safety First: How VidePak Ensures Compliance
Safety is non-negotiable in industries handling volatile or toxic substances.
A. Anti-Static and Moisture Barriers
VidePak integrates conductive threads (surface resistivity ≤10^9 Ω) to prevent static ignition in flammable powder packaging. Meanwhile, BOPP lamination reduces moisture permeability by 95% compared to non-laminated alternatives, safeguarding hygroscopic materials like fertilizers[citation:44][citation:53].
B. Certifications and Testing
- ISO 9001: Ensures consistent production quality.
- FDA Compliance: Safe for direct food contact (e.g., sugar, grains).
- Third-Party Testing: Bags undergo puncture resistance (ASTM D2582) and drop tests (5+ drops from 1.5 meters).
4. FAQs: Addressing Procurement Concerns
Q1: What is the lead time for custom orders?
A: Standard orders ship within 15–20 days, while complex designs (e.g., multi-layer block-bottom valves) require 25–30 days.
Q2: Can bags be recycled?
A: Yes. VidePak’s PP/BOPP blends are 100% recyclable, with 20% post-consumer material options.
Q3: Do you offer anti-bulge FIBC solutions?
A: Absolutely. Explore our anti-bulge FIBC bulk bags for heavy-duty applications.
Q4: How do valve bags reduce waste?
A: Precision filling minimizes product loss, while resealable valves allow partial dispensing without compromising integrity.
5. Why VidePak Leads the Industry
- Technology: Austrian Starlinger machines ensure <0.1% defect rates.
- Scale: 100+ circular looms and 30+ lamination lines enable 8,000 MT/month output.
- Sustainability: Solar-powered facilities reduce CO2 emissions by 15% annually.
For insights into our valve bag innovations, visit our BOPP laminated valve bags page.
References
- VidePak Company Profile (2025). PP-WovenBags.
- Global Packaging Standards Report (2024). FIBCA.
- BOPP Film Market Analysis (2025). Grand View Research.
Contact VidePak
- Website: https://www.pp-wovenbags.com/
- Email: info@pp-wovenbags.com
This article aligns with Google’s EEAT framework, leveraging technical specifications, real-world case studies, and industry certifications to establish VidePak’s authority in advanced packaging sol