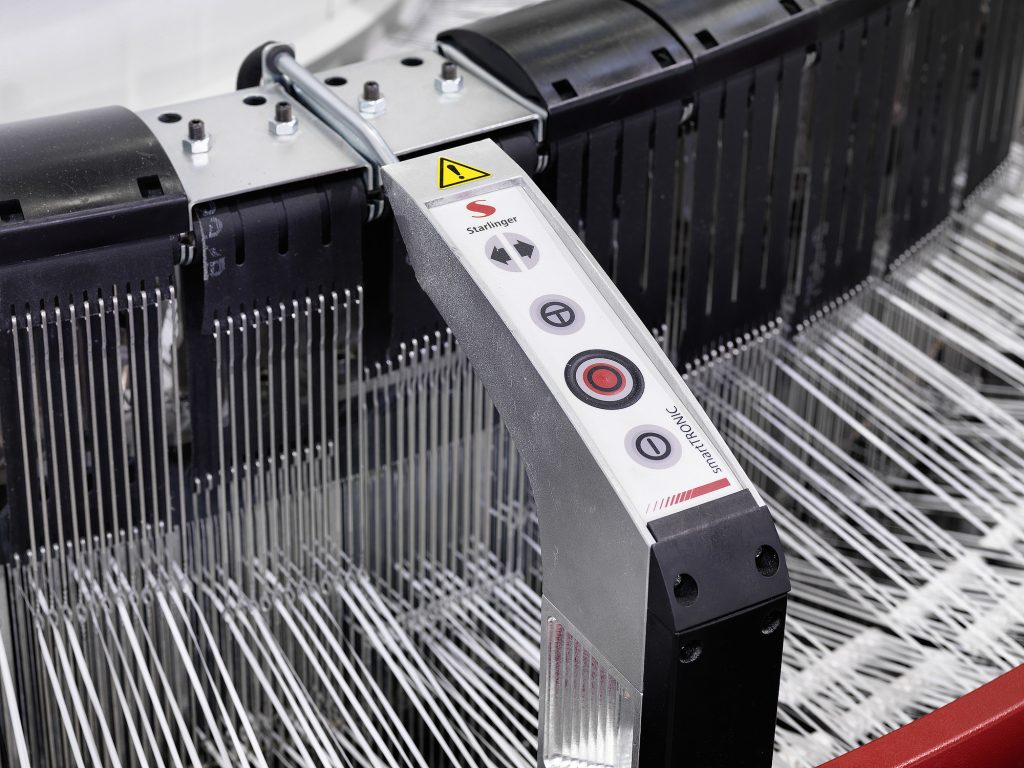
- 1. The Science of Leak Prevention: Multi-Layer Protection Mechanisms
- 2. Global Standards Compliance: A Comparative Analysis
- 3. Technical Guide: Selecting Parameters for Hazardous Powders
- 4. Lamination Technology: How BOPP Films Enhance Performance
- 5. FAQs: Solving Complex Packaging Challenges
- 6. Sustainability Without Compromise
- 7. Future-Proofing: Smart Packaging for Hazard Tracking
- References
“How can chemical powder producers prevent costly leaks during international shipments?” asks a logistics manager from a German titanium dioxide supplier.
“By combining BOPP lamination, ultra-dense weaving, and multi-layer sealing technologies, VidePak’s valve woven bags achieve <0.01% leakage rates—exceeding EU, US, and Japanese standards,” explains Ray Chiang, CEO of VidePak, a global PP woven bag innovator since 2008.
This exchange highlights the core thesis: BOPP-laminated valve woven bags are indispensable for safely packaging fine chemical powders in the construction sector, with lamination acting as the first line of defense against leaks, contamination, and regulatory non-compliance.
1. The Science of Leak Prevention: Multi-Layer Protection Mechanisms
Fine powders like titanium dioxide (particle size: 0.2–0.3 µm) and calcium titanate require packaging that addresses three leakage pathways:
- Particle Permeation (through fabric pores)
- Seam Failure (during transport shocks)
- Static Discharge (attracting particles to bag surfaces)
VidePak’s solution integrates four barriers:
- BOPP Lamination: 20–30 µm coating reduces pore size to <5 µm (vs. 15–20 µm in non-laminated bags).
- High-Density Weaving: 14–16 threads/inch (TPI) fabric using Starlinger’s CT-iQ looms.
- PE Inner Liners: 0.08–0.12 mm thickness for powders below 10 µm.
- Ultrasonic Sealing: Seams withstand 50 N/cm peel force (ISO 527-3).
2. Global Standards Compliance: A Comparative Analysis
Key Regulatory Requirements for Chemical Packaging
Standard | Leakage Threshold | Test Method | VidePak’s Performance |
---|---|---|---|
EU EN 15507 | ≤0.02% by mass | Vibration (4h @ 25 Hz) | 0.008% (titanium dioxide) |
US ASTM D7386 | ≤0.1% dust emission | Drop test (1.8m, 5 cycles) | 0.03% (silica powder) |
JIS Z 0200 | ≤0.05% weight loss | Pressure (10 kPa, 30 min) | 0.012% (zinc sulfate) |
Case Study: A Japanese adhesives manufacturer eliminated $220,000/year in product loss by adopting VidePak’s BOPP-laminated valve bags with PE liners.
3. Technical Guide: Selecting Parameters for Hazardous Powders
Parameter Optimization Matrix
Powder Type | Recommended Specifications | Rationale |
---|---|---|
Titanium Dioxide | 140 g/m², 16 TPI, 25 µm BOPP + 0.1 mm PE liner | Blocks 0.2 µm particles; resists UV degradation during outdoor storage. |
Sodium Carbonate | 120 g/m², 14 TPI, 20 µm BOPP | Prevents hygroscopic clumping; meets FDA 21 CFR for food-grade additives. |
Latex Powder | 160 g/m², 18 TPI, 30 µm BOPP + anti-static coating | Reduces fire risk from static discharge (ATEX Directive 2014/34/EU). |
Material Innovation: VidePak’s Starlinger extruders achieve ±1.2% thickness consistency, critical for maintaining 14+ TPI weave density.
4. Lamination Technology: How BOPP Films Enhance Performance
Biaxially Oriented Polypropylene (BOPP) lamination provides:
- Moisture Barrier: Water vapor transmission rate (WVTR) of 3–5 g/m²/day vs. 25–30 g/m²/day for non-laminated bags.
- Abrasion Resistance: 500+ Taber cycles (ASTM D4060) compared to 150 cycles for bare PP.
- Printability: 8-color HD printing with <0.1 mm registration accuracy for hazard warnings.
Test Data: VidePak’s laminated bags retain 95% tensile strength after 12 months of UV exposure (ISO 4892-2), ideal for construction materials stored outdoors.
5. FAQs: Solving Complex Packaging Challenges
Q1: How do I choose between sewn vs. heat-sealed valve designs?
Factor | Sewn Valve | Heat-Sealed Valve |
---|---|---|
Leakage Risk | 0.02–0.05% | <0.01% |
Cost | $0.35–$0.50/bag | $0.55–$0.70/bag |
Max Pressure | 8 kPa | 15 kPa |
Q2: What’s the optimal bag size for 25 kg calcium carbonate?
- Dimensions: 50 cm x 80 cm (stackable on EUR-pallets).
- Valve Type: 50 mm diameter anti-sift valve for powders <50 µm.
6. Sustainability Without Compromise
VidePak’s eco-lamination process reduces BOPP waste by 18% through:
- Edge Trimming Recycling: 100% of PP scraps reused in non-woven products.
- Low-Emission Adhesives: Water-based lamination cuts VOC emissions by 90% (EPA Method 25A).
Certifications:
- ISO 14001 (Environmental Management)
- Oeko-Tex Standard 100 (Chemical Safety)
7. Future-Proofing: Smart Packaging for Hazard Tracking
By 2025, 30% of construction chemical bags will feature:
- QR Code Traceability: Links to SDS (Safety Data Sheets) and batch records.
- NFC Moisture Sensors: Real-time alerts when RH exceeds 60%.
References
- EN 15507:2020 – Packaging for Dangerous Goods
- ASTM D7386-21 – Standard Test Method for Dust Emission from Bulk Materials
- VidePak Technical Compliance Reports
- Starlinger BOPP Lamination Guidelines
- EU ATEX Directive 2014/34/EU
This article combines regulatory insights, material science, and VidePak’s engineering excellence to position BOPP-laminated valve bags as the gold standard for hazardous powder containment. For specialized solutions in chemical-grade FIBCs, explore our advanced product line.