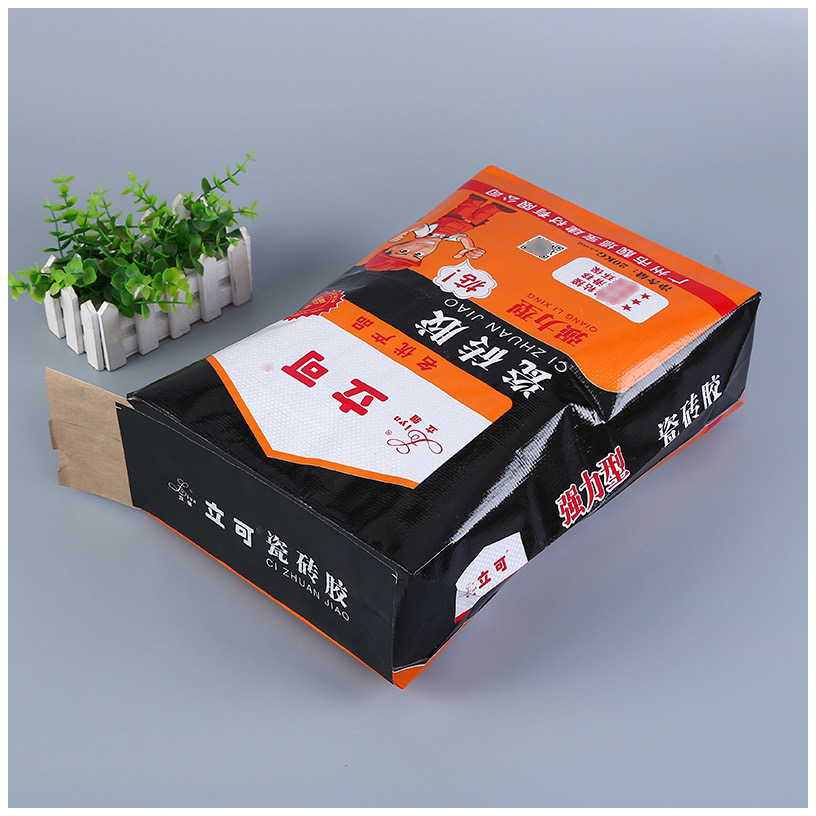
Paper Valve Woven Bags are a popular packaging solution used in various industries, offering superior protection and enhanced durability. With their exceptional strength, moisture resistance, and high customization potential, these bags are ideal for packaging products ranging from construction materials to food ingredients. In this article, we will explore the production process of Paper Valve Woven Bags, highlighting each critical step, from extrusion to packaging. This exploration will also touch on the advanced technology used, including Starlinger and W&H equipment, which significantly contribute to the efficiency and quality of production.
Key Features of Paper Valve Woven Bags
Paper Valve Woven Bags, also known as Paper Valve Woven Sacks or Kraft Valve Woven Bags, are made using a combination of paper and woven polypropylene (PP) fabric. These bags offer multiple benefits, such as:
- High Strength: The woven polypropylene provides enhanced strength and tear resistance.
- Moisture Protection: The paper layer ensures moisture resistance, making these bags ideal for storing dry and perishable products.
- Customization: Paper Valve Woven Bags can be customized in size, color, and print to meet specific needs.
- Sustainability: The use of Kraft paper and PP material offers an eco-friendly alternative for packaging.
Key Parameters of Paper Valve Woven Bags
The table below outlines some typical parameters of Paper Valve Woven Bags, which help in understanding their suitability for different applications:
Property | Paper Valve Woven Bags |
---|---|
Material | Kraft Paper + Woven PP |
Thickness | 80-120 gsm (paper) |
Weight Capacity | 10-50 kg |
Dimensions | Customizable |
Printing Options | Flexo, Gravure Printing |
Valve Type | Single Valve, Multi-valve |
Customization | Size, Print, Colors |
Laminated Layer | Optional (PP/PE) |
As evident, Paper Valve Woven Bags come with flexible design options that allow manufacturers to tailor these bags to suit their product specifications.
The Production Process of Paper Valve Woven Bags
The production of Paper Valve Woven Bags involves a complex and highly automated process to ensure efficiency and consistent quality. Each stage is crucial for creating durable, high-quality bags that can withstand rough handling and protect their contents.
1. Extrusion of Polypropylene (PP) Filament
The process begins with the extrusion of polypropylene, a plastic polymer, into thin filaments. These filaments are produced using advanced extrusion lines from leading manufacturers like Starlinger. The extrusion process ensures that the PP material is of uniform quality, which is essential for the strength and durability of the woven fabric.
The filaments are typically extruded through high-speed machines, with the capability of producing over 200 strips per minute. This high-speed extrusion ensures that large quantities of material are produced quickly, meeting the demands of various industries.
2. Weaving of the Fabric
Once the polypropylene filaments are ready, they are fed into circular looms, which are also sourced from Starlinger. The weaving process involves interlacing the PP filaments to create a strong, durable fabric. The circular looms have high automation levels, which means they can weave large quantities of fabric without manual intervention, increasing production efficiency.
The fabric’s strength is crucial as it forms the base of the Paper Valve Woven Bag. The automated nature of the looms ensures consistent weave density and uniformity, key factors in producing high-quality bags. Additionally, modern weaving machines are designed to handle the intricate requirements of creating both the main body of the bag and its valve for easy filling.
3. Cutting and Stitching
After weaving, the fabric is cut into precise sizes based on customer requirements. The cutting process uses automatic machines that ensure clean and accurate cuts, which reduces material wastage and maximizes production efficiency.
Next, the cut pieces are sewn into bag shapes. This process involves high-speed stitching machines, which are highly automated and ensure precise stitching. These machines are capable of sewing up to 200 bags per minute, ensuring that production remains efficient.
4. Printing and Coating
Once the bags are stitched, they are ready for printing and coating. Printing is done using flexographic or gravure printing technology, with options for multi-color prints. This allows for branding and customization, making the bags not only functional but also a marketing tool for businesses.
In addition to printing, some bags undergo a coating process. This step involves applying a layer of polyethylene (PE) or polypropylene (PP) film over the paper to enhance moisture resistance and strength. The coating also helps in providing a smooth surface for printing, ensuring that the logos and designs are clear and vibrant.
5. Inspection and Quality Control
Quality control is a critical aspect of the production process. During various stages, including weaving, cutting, stitching, and printing, rigorous inspection protocols are followed. Automated inspection systems check for defects such as weak spots, incorrect stitching, or printing errors.
High-tech machines equipped with cameras and sensors can detect even the slightest flaws. This ensures that only bags of the highest quality reach the final packaging stage.
6. Final Packaging
Once the bags pass inspection, they are ready for packaging. The automated packaging process ensures that bags are efficiently stacked, folded, and packed according to customer specifications. Typically, bags are bundled and wrapped into large packages, making them easier to handle during transportation.
Advanced Equipment for Enhanced Efficiency
The entire production process is driven by cutting-edge equipment from leading suppliers like Starlinger and W&H. These machines are designed with high automation capabilities, allowing for multi-machine linkage, where different machines work in sync to ensure uninterrupted production flow.
For example, the extrusion lines can automatically feed into the circular looms, which in turn connect to cutting and stitching machines. This high degree of automation allows for production speeds of over 200 bags per minute, reducing downtime and increasing output.
The use of such advanced equipment not only increases production efficiency but also ensures that the bags are produced with consistent quality. Starlinger and W&H’s equipment are known for their precision and reliability, making them ideal for large-scale production.
Why Choose Paper Valve Woven Bags?
Paper Valve Woven Bags are a robust and versatile packaging solution that is well-suited for industries that require secure and moisture-resistant packaging. These bags offer several advantages, including:
- Sustainability: Made with eco-friendly Kraft paper, these bags provide a sustainable alternative to other forms of packaging.
- Durability: The strong woven PP fabric and laminated coating ensure that the bags can withstand heavy loads and rough handling.
- Customization: These bags can be tailored to suit specific product requirements, including size, printing, and valve design.
- Moisture Resistance: The paper valve construction provides an excellent barrier against moisture, making them ideal for storing dry and perishable products.
Conclusion
Paper Valve Woven Bags are a highly efficient and customizable solution for packaging needs across a range of industries. From the extrusion of polypropylene to the final packaging, every step of the production process is designed for optimal efficiency and quality. With cutting-edge equipment from Starlinger and W&H, manufacturers can ensure high-speed production without compromising on the strength and durability of the bags. Whether it is for packaging food, construction materials, or chemicals, Paper Valve Woven Bags provide a reliable and sustainable option that meets the highest standards of the industry.
For more information, explore how Paper Valve Woven Bags are advancing moisture protection through innovative technologies like seven-layer co-extruded films here, and discover how Paper Valve Woven Sacks are evolving to meet global market demands here. Additionally, dive into the benefits of Kraft Valve Woven Bags for the chemical fertilizer industry here.