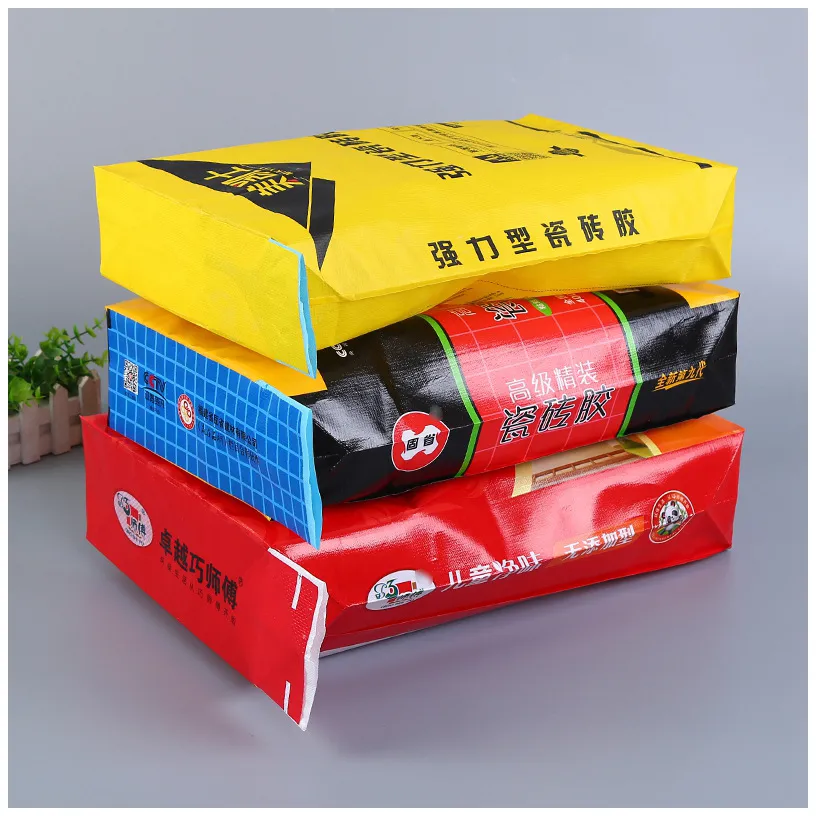
In the realm of packaging, Printed Woven Bags have gained significant popularity due to their strength, versatility, and aesthetic appeal. These bags are not only durable but also customizable, allowing businesses to use them for branding and marketing purposes. However, one of the most severe quality issues associated with Printed Woven Sacks is the phenomenon of bag bursting. This issue can lead to significant product loss and compromise customer satisfaction. In this article, we will delve into the reasons behind this problem, particularly focusing on the quality control measures implemented by VidePak to mitigate the risks associated with bursting bags.
The Phenomenon of Bag Bursting
Bag bursting, often referred to as “炸包” in the industry, occurs when a woven bag ruptures during handling or transportation. This not only leads to product spillage but can also cause safety hazards in workplaces and negatively impact the reputation of manufacturers.
The causes of bag bursting can be broadly categorized into two primary areas: material quality and product handling. Below, we will explore these categories and discuss how each can contribute to this issue.
Material Quality
The quality of raw materials used in the production of Custom Woven Bags is crucial in preventing bag bursting. Several factors influence the integrity of the woven bags, including:
- Raw Material Composition: The primary raw material for woven bags is polypropylene (PP), known for its strength and resistance to chemicals. However, the use of recycled or substandard PP can weaken the bags, making them prone to bursting under stress. At VidePak, we ensure that only virgin polypropylene is used, sourced from reputable suppliers, which enhances the durability of our Printed PP Woven Bags.
- Thickness of the Material: Thicker woven materials can resist higher stress levels. We have established rigorous standards for the thickness of our woven bags, with detailed specifications outlined in the table below:
Bag Type | Thickness Range (mm) | Tensile Strength (N) | UV Resistance | Drop Test Performance |
---|---|---|---|---|
BOPP Woven Bags | 0.05 – 0.15 | 200 – 600 | High | 2.0 meters |
Valve Bags | 0.10 – 0.20 | 300 – 700 | Medium | 1.5 meters |
Kraft Paper Woven Bags | 0.15 – 0.30 | 400 – 800 | High | 1.0 meters |
- Multi-Layer Construction: The design of the woven bags can also affect their durability. Bags with multiple layers provide additional protection against tearing and bursting. VidePak employs advanced multi-layer technology to enhance the strength and reliability of our bags, ensuring they can withstand rigorous handling.
Product Handling
In addition to raw material quality, product handling plays a crucial role in preventing bag bursting. Improper handling can lead to stress and damage, even if the materials used are of high quality. Factors influencing product handling include:
- Overloading: Overfilling bags beyond their specified capacity can lead to increased stress on seams and materials, resulting in ruptures. We provide clear guidelines on maximum fill levels for each type of bag, ensuring that our customers are well-informed.
- Transport and Storage Conditions: Environmental factors, such as exposure to UV light, moisture, and extreme temperatures, can weaken woven bags over time. To combat this, we recommend storing bags in controlled environments away from direct sunlight and moisture.
- Improper Handling Techniques: Training personnel in proper handling techniques is essential. Mismanagement during loading and unloading can result in excess strain on the bags. At VidePak, we offer training sessions for our clients’ staff to ensure they understand how to handle our Multiple Color Bags effectively.
Quality Control Measures at VidePak
To combat the challenges associated with bag bursting, VidePak has implemented a comprehensive quality control system throughout the production process. Here are some key measures we take:
- Incoming Material Inspection: Every batch of raw materials undergoes rigorous testing before production. This includes verifying the quality of the polypropylene and checking for compliance with our specifications.
- In-Process Quality Checks: During production, our engineers conduct regular inspections to ensure the bags meet the desired thickness, tensile strength, and UV resistance. This proactive approach helps identify and rectify issues before they escalate.
- Final Product Testing: Once the bags are produced, they undergo a series of tests to assess their performance. Key tests include:
- Tensile Strength Testing: Ensures that the bags can withstand the required load without bursting.
- UV Resistance Testing: Measures the bags’ ability to resist degradation from sunlight exposure.
- Drop Tests: Evaluates the durability of the bags under different handling conditions.
- Feedback Loop: We encourage our clients to provide feedback on bag performance in real-world applications. This information helps us continuously refine our products and address any emerging issues.
Conclusion
The quality and reliability of Printed Woven Bags are paramount to maintaining customer satisfaction and protecting products during transportation and storage. At VidePak, we understand the challenges associated with bag bursting and have implemented stringent quality control measures to mitigate these risks. By focusing on raw material quality, proper handling, and continuous improvement, we strive to deliver exceptional products that meet the diverse needs of our clients.
In summary, our commitment to excellence in producing Custom Woven Bags not only enhances our reputation but also reinforces our dedication to quality in the packaging industry. For more insights into the benefits of Printed Woven Bags, visit our article on Printed Woven Bags.