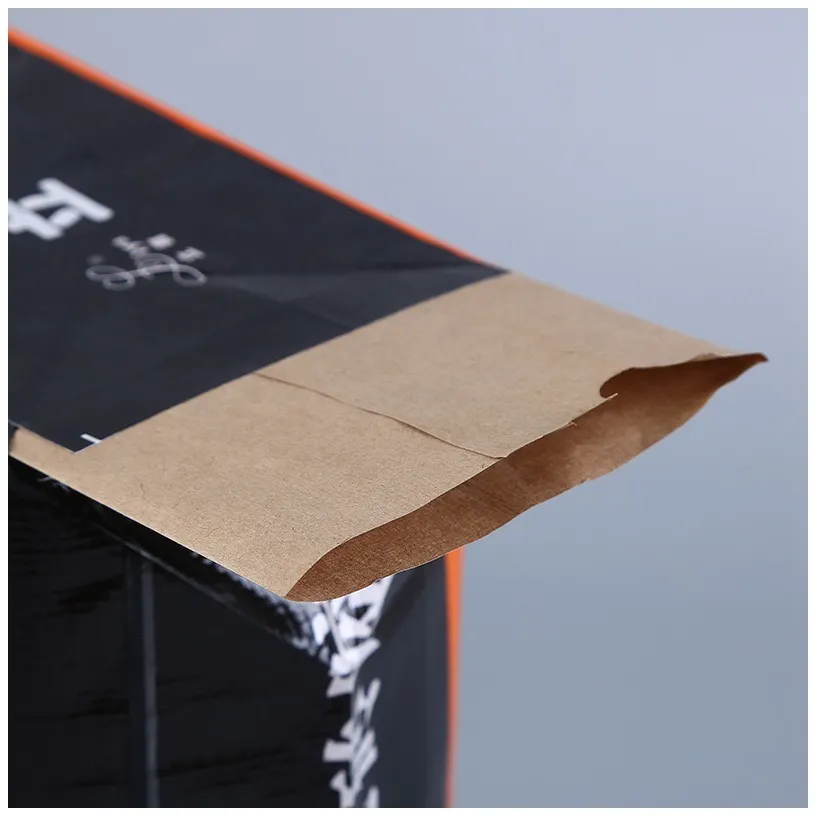
In the packaging industry, the quality and reliability of products are paramount. Among various types of packaging solutions, Paper Valve Woven Bags have gained prominence due to their durability and versatility. However, one of the most critical challenges faced by manufacturers and users alike is the phenomenon of bag bursting, which poses significant risks and impacts operational efficiency. This article delves into the reasons behind bag bursting, focusing on raw materials and finished product testing, while outlining how VidePak implements stringent quality control measures to prevent such occurrences.
The Issue of Bag Bursting
Bag bursting refers to the failure of woven bags due to excessive internal pressure or external impacts. In the case of Paper Valve Woven Bags, this issue can arise from several factors, including the choice of raw materials, production processes, and insufficient quality checks. The consequences of bag bursting are dire, leading to product loss, environmental contamination, and potential safety hazards for personnel.
Factors Leading to Bag Bursting
- Raw Material Quality
- The selection of appropriate raw materials is crucial for the performance of any woven bag. In the case of Paper Valve Woven Bags, using low-quality polypropylene (PP) or improperly processed kraft paper can lead to weak structures that are prone to bursting. High-quality PP granules ensure strong fabric construction that can withstand both internal pressure and external forces.
- Additionally, the environmental conditions during production, such as humidity and temperature, can affect the material properties. If the raw materials are not stored or handled properly, they may degrade, compromising their strength and durability.
- Manufacturing Process
- The manufacturing process plays a significant role in the quality of the finished product. If the weaving process is not executed correctly, the fabric may have inconsistencies that can weaken its structure. Moreover, inadequate sealing of the bag can lead to leakage or bursting when filled with products.
- The handling of materials during production, including the extrusion and lamination stages, needs to be meticulously managed to ensure that the bags meet the required specifications.
- Finished Product Testing
- To ensure the reliability of the bags, comprehensive testing is essential. At VidePak, each batch of raw materials undergoes a strict sampling process, which includes assessing the following parameters:
Parameter | Description |
---|---|
Thickness | Ensures that the bag material meets minimum thickness requirements. |
Tensile Strength | Tests the bag’s ability to withstand pulling forces without tearing. |
UV Resistance | Assesses the bag’s durability against UV exposure, preventing degradation. |
Drop Test | Measures the bag’s ability to withstand falls without bursting. |
Visual Inspection | Evaluates the overall appearance and any defects in the bags. |
Quality Control Measures at VidePak
To mitigate the risks associated with bag bursting, VidePak employs a comprehensive quality management system that encompasses both raw material selection and finished product testing.
- Rigorous Supplier Selection
- VidePak collaborates with reputable suppliers who provide high-quality raw materials. Each supplier is thoroughly vetted based on their track record of quality, consistency, and adherence to industry standards. This helps to ensure that the raw materials used in the production of Paper Valve Woven Sacks meet the stringent quality requirements needed for durability and performance.
- Stringent Incoming Material Inspection
- Each batch of incoming raw materials undergoes rigorous testing before production. This includes checking for impurities, verifying thickness, and conducting tensile strength tests. By implementing such strict measures, VidePak can prevent subpar materials from being used in the manufacturing process.
- Production Process Optimization
- VidePak employs state-of-the-art machinery from leading global suppliers such as Starlinger, ensuring that the production processes are optimized for efficiency and quality. Continuous monitoring during the weaving and sealing processes allows for immediate corrective actions, minimizing defects.
- Comprehensive Finished Product Testing
- After the bags are produced, they are subjected to various tests to evaluate their overall quality and performance. The finished products are tested for parameters including tensile strength, UV resistance, and drop performance. This multi-faceted approach ensures that only bags meeting the highest standards are shipped to customers.
- Feedback Loop and Continuous Improvement
- Customer feedback is crucial for identifying potential issues with the bags. VidePak actively seeks input from users and uses this data to enhance product design and manufacturing processes. This iterative approach ensures that the company continually improves its products and addresses any emerging quality concerns promptly.
- Training and Development
- VidePak recognizes that skilled personnel are integral to maintaining high quality standards. Regular training sessions for staff on quality control practices, production processes, and material handling further bolster the company’s commitment to excellence. By investing in employee development, VidePak ensures that its team is well-equipped to handle the complexities of bag production.
Conclusion
Bag bursting is a significant concern in the production and use of Paper Valve Woven Bags. Through meticulous attention to raw material quality, stringent production processes, and comprehensive testing protocols, VidePak takes proactive measures to prevent this issue. By investing in quality management systems and continuously improving practices, the company ensures that its products not only meet but exceed industry standards, providing customers with reliable packaging solutions that support their operational needs.