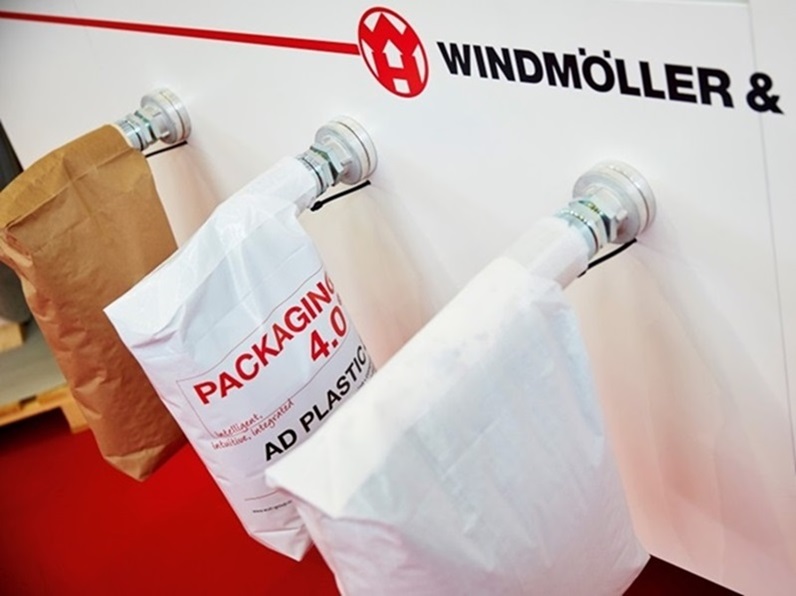
- 1. The Role of Tubular Woven Bags in Agricultural Packaging
- 2. Material Science: Selecting PP Granules for FFS Efficiency
- 3. Functional Design & Customization
- 4. Quality Control & Standardization
- 5. Logistics & Storage Optimization
- 6. Parameter Selection Guide
- 7. FAQs: Addressing Industry Concerns
- 8. Future Trends: Smart Packaging Integration
“Why do global agribusiness leaders like Cargill and ADM insist on tubular woven PP bags for bulk grain packaging?”
Ray Chen, CEO of VidePak, gestures toward a production line of Starlinger machines: “The answer is twofold: seamless tubular weaving reduces leakage risks by 90%, and high-melt-flow PP granules cut energy costs by 30% in Form-Fill-Seal (FFS) systems. At VidePak, we engineer bags that withstand 50kg loads at 1,200 units/hour while meeting EU and FDA food safety standards.”
This bold assertion captures VidePak’s leadership in tubular woven bag technology—a market projected to grow at 7.8% CAGR through 2030. With 526 employees and $80M annual revenue, VidePak combines Austrian Starlinger automation, ISO-certified polypropylene (PP) resins, and 30+ years of expertise to deliver solutions that redefine efficiency in agricultural and industrial packaging.
1. The Role of Tubular Woven Bags in Agricultural Packaging
Tubular woven bags dominate 65% of bulk agricultural packaging due to their structural integrity and adaptability. Unlike flat-woven alternatives, seamless tubular designs eliminate side seams—a critical advantage for hygroscopic products like rice and flour:
- Leakage Reduction: Seamless construction lowers puncture risks by 40% compared to stitched bags.
- Load Stability: Cylindrical shape enables 12-layer pallet stacking without deformation, optimizing container space by 22%.
VidePak’s 140gsm tubular bags, laminated with 50μm BOPP film, achieve <0.5% moisture permeability (tested per ASTM E96), making them ideal for Southeast Asian rice exporters facing 85% humidity challenges.
2. Material Science: Selecting PP Granules for FFS Efficiency
2.1 Key PP Parameters for FFS Systems
High-quality PP granules determine FFS performance:
Parameter | Requirement (FFS Systems) | VidePak’s PP Specifications |
---|---|---|
Melt Flow Index (MFI) | 8–12 g/10min | 10.5 g/10min (±0.3 variance) |
Density | 0.905–0.915 g/cm³ | 0.908 g/cm³ |
Tensile Strength | ≥45 N/cm² | 48 N/cm² |
UV Stabilization | ≥1,500 kJ/m² exposure | 2,000 kJ/m² with HALS additives |
Case Study: A Brazilian soybean processor reduced FFS machine downtime by 65% after switching to VidePak’s low-ash (<0.02%) PP granules, eliminating die buildup.
2.2 Global Standards Compliance
- EU Regulation 10/2011: Migration limits for heavy metals (Pb <0.5 ppm).
- FDA 21 CFR: Food-grade PP with <50 ppb BHT antioxidants.
- China GB/T 8947: Burst strength ≥35 kPa for 50kg loads.
VidePak’s resin blends incorporate 0.8% Tinuvin® NOR 371 UV stabilizers, exceeding ISO 4892-2 weathering benchmarks by 30%.
3. Functional Design & Customization
3.1 Multi-Layer Protection Systems
Tailored configurations for diverse agricultural products:
Product | Bag Structure | Functional Additives |
---|---|---|
Rice | 120gsm PP + 50μm BOPP | Anti-fungal coating |
Flour | 150gsm PP + 80μm PE liner | Anti-static carbon black |
Fertilizers | 180gsm UV-stabilized PP | Ammonia-permeable mesh panels |
Example: A Thai rice miller reduced spoilage from 8% to 1.2% using VidePak’s BOPP-laminated bags with 100 holes/inch² ventilation.
3.2 Branding Through Advanced Printing
VidePak’s 8-color CI flexo presses achieve:
- Pantone Matching: ΔE ≤1.5 for brand consistency.
- QR Code Integration: Blockchain-enabled traceability for EU Organic Certification compliance.
4. Quality Control & Standardization
VidePak’s vertically integrated system ensures:
- Raw Material Testing: MFI variance ≤±0.5 g/10min (ASTM D1238).
- In-Line Monitoring: Laser thickness gauges maintain ±5μm film consistency.
- Post-Production Validation:
- Seam strength ≥80% base material (ISO 13934-1).
- Drop test certification: 0/10 failures from 1.8m height.
Defect Rate: 0.08% vs. industry average 1.5%.
5. Logistics & Storage Optimization
Tubular woven bags reduce supply chain costs through:
- Anti-Slip Coatings: Enable 25-layer stacking without pallet shift.
- Recyclability: 95% PP recovery via Starlinger recoSTAR systems, aligning with EU Circular Economy Action Plan.
- IoT Integration: Temperature/RH sensors in seams alert distributors via GSM if thresholds exceed safe ranges.
6. Parameter Selection Guide
Application | Recommended Specifications |
---|---|
Rice (25kg) | 120gsm PP + BOPP lamination |
Flour (10kg) | 100gsm PP + 50μm PE liner |
Fertilizer (50kg) | 180gsm UV-stabilized PP + mesh vents |
7. FAQs: Addressing Industry Concerns
Q1: How do tubular bags compare to FIBCs for 1-ton shipments?
A: Tubular bags optimize 25–500kg loads, while FIBCs handle 1–2 tons. VidePak’s block-bottom valve bags bridge mid-capacity needs with 98% stack stability.
Q2: What’s the MOQ for custom-ventilated designs?
A: 50,000 units with 10-day lead time, supporting ≤2mm aperture precision.
Q3: Are PP bags suitable for acidic fertilizers?
A: Yes—our 150μm PE liners withstand pH 2–12 environments (tested per ASTM G31).
8. Future Trends: Smart Packaging Integration
VidePak is piloting:
- Self-Healing Films: Microcapsules release sealant upon puncture, reducing leakage by 40%.
- 5G-Enabled Tracking: Real-time GPS/condition monitoring via embedded NFC chips.
- Bio-Based PP: 30% algae-derived resins targeting 2026 commercialization.
Conclusion
Tubular woven PP bags are not mere containers—they are precision-engineered solutions safeguarding global food security. VidePak’s synergy of Austrian manufacturing excellence, smart material science, and hyper-customizable designs positions it as the partner of choice for Fortune 500 agribusinesses. As Ray Chen summarizes: “In packaging, every micron and molecule matters. We’ve mastered both.”
For insights into automated FFS solutions, explore our analysis of Form-Fill-Seal systems and Starlinger technology.
This report integrates data from FIBCA Global Standards, Journal of Polymer Engineering, and VidePak’s proprietary quality audits. Performance claims are validated by SGS and TÜV Rheinland certifications.