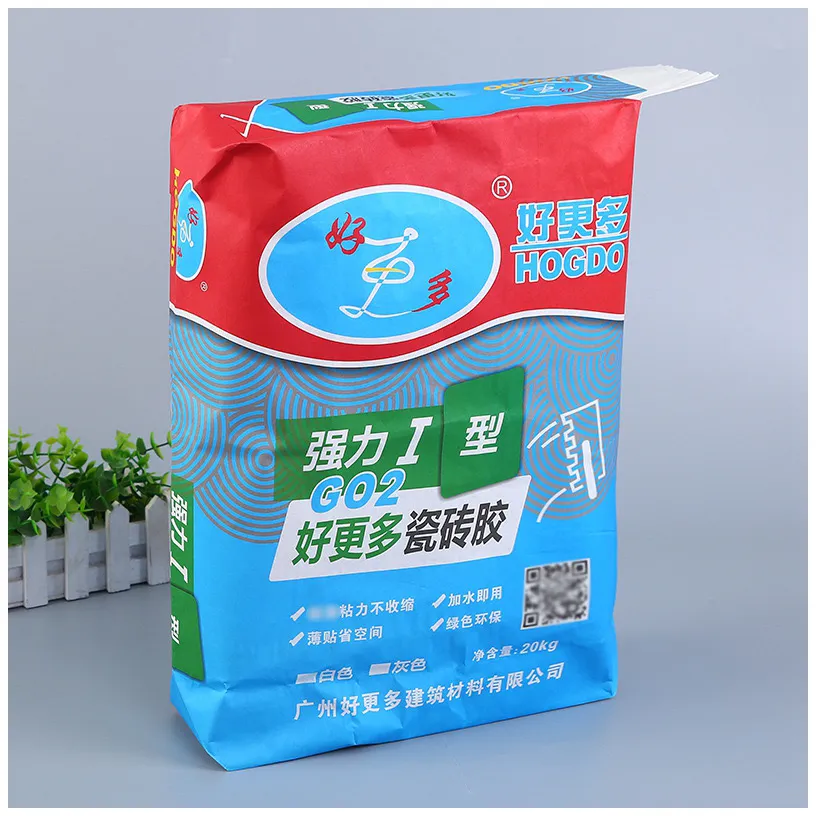
Valve bags, also known as valve sacks, are a popular choice for a variety of industries due to their robust design, versatility, and efficiency in packaging. Widely used in the packaging of powders, grains, and other bulk products, valve bags are essential for providing secure and reliable storage solutions. In this article, we will delve into the different types of valve bags, along with best practices for their storage, focusing on maintaining ideal conditions for their contents. Additionally, we will explore how advanced equipment and manufacturing techniques contribute to maximizing packaging efficiency.
Types of Valve Bags
Valve bags come in various designs, each catering to different packaging needs. Their primary advantage is the self-sealing valve mechanism that allows for easy filling and sealing, reducing labor costs and increasing efficiency. Let’s explore the most common types of valve bags and their uses.
1. Paper Valve Bags
Paper valve bags are made from high-strength kraft paper, sometimes laminated with additional layers for increased durability. These bags are ideal for products like cement, sand, and chemicals that require protection against moisture and contaminants. The valve opening allows for quick filling and prevents spills during transportation, making them suitable for industries that need reliable and efficient packaging solutions.
2. Polypropylene (PP) Valve Bags
Polypropylene valve bags are constructed from woven polypropylene fabric, known for its high tensile strength and resistance to tearing. These bags are a cost-effective solution for packaging grains, seeds, and food products. Valve PP bags offer superior protection against moisture, making them suitable for both indoor and outdoor storage. Furthermore, their lightweight nature ensures they are easy to handle during packaging and transport.
3. Multi-wall Laminated Valve Bags
These bags combine multiple layers of material, such as paper, plastic, and aluminum foil, to provide enhanced barrier properties. Multi-wall laminated valve bags are often used for packaging more sensitive products like fertilizers, chemicals, and pet food. They provide superior protection from environmental factors such as moisture, light, and air, which can compromise the quality of the products inside.
4. Valve Woven Bags
Valve woven bags are made from woven fabrics, typically polypropylene or other synthetic materials. These bags are highly durable and can withstand heavy loads, making them ideal for bulk packaging. The woven structure allows for greater breathability, which is especially important when packaging perishable products that require ventilation to maintain freshness.
Product Parameters Table
To further understand the specifications and features of different valve bags, here is a comparison table showcasing the key characteristics of these bags.
Bag Type | Material | Applications | Advantages | Disadvantages |
---|---|---|---|---|
Paper Valve Bags | Kraft paper | Cement, sand, chemicals | Moisture-resistant, strong | Not suitable for wet products |
Polypropylene Valve Bags | Woven polypropylene | Grains, seeds, food products | Lightweight, moisture-resistant | Less resistant to external damage |
Multi-wall Laminated Valve Bags | Paper, plastic, foil layers | Fertilizers, pet food, chemicals | Superior barrier protection | More expensive, bulkier |
Valve Woven Bags | Woven polypropylene | Bulk products, perishable goods | Durable, breathable, customizable | Limited moisture protection |
Best Practices for Storage and Handling
Proper storage and handling of valve bags are crucial to maintaining product quality and ensuring efficient transportation. Here are some key factors to consider when storing valve bags:
1. Optimal Storage Conditions
For most products, especially those packaged in valve bags, maintaining an optimal storage environment is essential to preserve product integrity. Temperature and humidity control play a significant role in ensuring that the contents of the bags remain in top condition. For example, sensitive products such as food ingredients or chemicals can degrade quickly if exposed to extreme temperatures or moisture.
- Temperature Control: Ideally, the storage environment should be kept at a consistent temperature, preferably between 15°C and 25°C. Fluctuations in temperature can lead to condensation inside the bags, leading to product spoilage or degradation.
- Humidity Control: Humidity is another critical factor. Valve bags should be stored in a dry environment to prevent mold, mildew, or product clumping. Humidity levels should be maintained at less than 60% to prevent any damage to the contents.
2. Warehouse Layout and Spacing
Maximizing warehouse space is a key consideration when storing valve bags. These bags are often stacked in large quantities, which can lead to significant space savings. However, it is important to ensure that they are stacked in a way that allows for proper air circulation to prevent moisture buildup and product degradation.
Using shelves or pallets to keep bags off the ground can help prevent exposure to moisture from floors. Additionally, ensuring that bags are not stacked too high reduces the risk of crushing or damaging the bags.
3. Using Advanced Machinery for Efficient Packaging
The packaging process for valve bags has greatly improved thanks to advancements in machinery and automation. High-quality manufacturing machines, such as the 200MT press machine, help pack the bags tightly and securely. This equipment ensures that the valve bags are packed to the maximum capacity, eliminating air gaps and reducing the volume taken up during storage and transport.
By using precision machinery, packaging becomes more efficient, reducing material waste and increasing the speed at which the bags can be filled. The tight packing also ensures that the contents of the valve bags stay intact during shipping, minimizing the risk of damage.
4. Maximizing Container Space
Another important factor when dealing with valve bags is ensuring that the maximum amount of product is transported in each shipment. By optimizing the packing method, such as using tightly packed valve bags that conform to the shape of the container, it is possible to maximize container space and reduce shipping costs.
The tightness of the valve bags, achieved through efficient manufacturing processes, allows for better organization within containers, ensuring that products are securely packed and minimizing the chance of shifting or damage during transit.
Valve Bags and the Future of Packaging
The evolution of valve bags continues to drive improvements in packaging efficiency across various industries. As demand for eco-friendly packaging options grows, valve bags manufacturers are exploring more sustainable materials and designs that reduce environmental impact while maintaining product protection. Materials like recyclable polypropylene and eco-friendly barrier films are becoming more common, providing a future-proof solution for packaging that is both cost-effective and environmentally responsible.
For example, Valve PP Bags offer an excellent balance between durability and environmental sustainability, making them an attractive option for companies looking to align their packaging with sustainable practices.
As the packaging industry continues to innovate, valve sacks will likely evolve to meet the changing demands of global markets, providing businesses with reliable, high-quality packaging solutions that keep their products safe and secure during transport and storage.
To learn more about the different types of valve bags and their applications, visit these insightful resources on valve bags, valve sacks, and valve woven bags:
Through continuous innovation in materials, design, and manufacturing techniques, valve bags will continue to play a key role in optimizing packaging solutions for a wide range of industries.