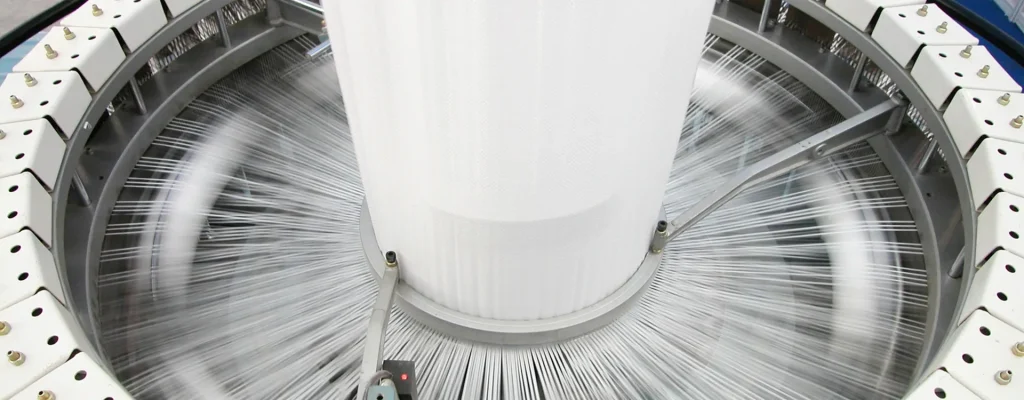
- Valve Bag Mechanics: Precision Design for Animal Feed Preservation
- Global Compliance Framework: VidePak’s Multinational Quality Protocols
- Manufacturing Excellence: Starlinger-Driven Production Workflow
- Sector-Specific Solutions: Optimizing Feed Packaging Performance
- FAQs: Addressing Procurement Priorities
- Conclusion: Global Standards, Localized Expertise
The global animal feed packaging market is projected to exceed $24 billion by 2027, with valve bags emerging as the preferred solution for 65% of bulk feed producers due to their dust-free filling and superior stackability. VidePak, leveraging 30+ years of expertise and 16 Starlinger extrusion lines, delivers ISO 22000-certified valve bags that meet ASTM, EN, REACH, and JIS standards, ensuring compliance across 80+ countries. This article explores valve bag functionality, VidePak’s multinational quality governance, and technical innovations that reduce feed spoilage by up to 40% in humid climates.
Valve Bag Mechanics: Precision Design for Animal Feed Preservation
1. Structural Advantages in Feed Packaging
- Dust Containment: Patented pasted valve designs reduce particulate emissions during filling by 95% compared to open-mouth bags.
- Moisture Control: BOPP laminated versions achieve <0.5% moisture ingress in 85% RH environments (tested per ASTM D779).
- Case Study: A Brazilian poultry feed supplier reduced product clumping by 30% using VidePak’s PE-coated valve bags with 12-micron inner liners.
2. Load Capacity & Durability
- Construction: 3-ply woven PP fabric (140–180 GSM) withstands 50 kg drops from 1.5 meters (EN 15512:2020 compliant).
- Seam Integrity: Ultrasonic sealing achieves 80 N/cm tensile strength at valve junctions, preventing leakage during rail transport.
Global Compliance Framework: VidePak’s Multinational Quality Protocols
1. ISO 22000:2018 Food Safety Management
- Process Controls: XRF scanners detect heavy metals (Pb/Cd <5 ppm) in virgin PP granules.
- Hygiene Standards: Class 100,000 cleanrooms for feed-contact surfaces, validated via ATP bioluminescence testing (<50 RLU).
2. Regional Certification Mastery
- EU REACH: Full SVHC compliance (<0.1% w/w for 223 restricted substances).
- US ASTM D5635: Valve bags withstand -25°C to 70°C without brittleness.
- Japan JIS Z 0238: Accelerated aging tests confirm 24-month shelf life stability.
Quality Assurance Metrics
Parameter | VidePak Standard | Industry Average |
---|---|---|
GSM Consistency | ±2% across batches | ±5–8% |
Valve Seal Strength | ≥70 N/cm (ISO 13934-1) | 45–60 N/cm |
Print Adhesion | 4B (ASTM D3359) | 2B–3B |
Manufacturing Excellence: Starlinger-Driven Production Workflow
1. Extrusion & Weaving
- Starlinger iSUPRA® Lines: Melt virgin PP at 230°C ±3°C, producing tapes with 0.04 mm thickness tolerance.
- Circular Looms: 100+ machines weave 14×14 strands/cm² fabric, achieving 150 GSM with ≤0.3% defect rate.
2. Lamination & Valve Integration
- BOPP Lamination: 25-micron films applied via 400°C thermal bonding, achieving 0.02 g/m²/24h WVTR.
- Valve Assembly: Robotic placement ensures ±0.5 mm positional accuracy, critical for automated filling systems.
3. Quality Control Systems
- Inline Spectroscopy: Detects pigment concentration deviations >1% during 10-color flexo printing.
- Burst Testing: 100% of bags undergo 35 kPa pressure tests (exceeding EN 13553 requirements).
Sector-Specific Solutions: Optimizing Feed Packaging Performance
Feed Type | Key Challenge | VidePak Solution |
---|---|---|
Poultry Pellet Feed | Abrasion resistance | 160 GSM bags with 50-micron PE coating |
Aquaculture Powder | Saltwater corrosion | Aluminum foil laminated valve bags |
Ruminant Mineral Mix | UV degradation | UV-stabilized BOPP with 8% TiO2 additive |
Pet Food Premixes | Aroma retention | Multi-layer kraft paper composites |
Client Example: A EU organic feed producer achieved 99.8% filling efficiency using VidePak’s anti-static valve bags, eliminating powder clogging in robotic packaging lines.
FAQs: Addressing Procurement Priorities
Q1: How do valve bags comply with EU organic feed regulations?
A: Our FDA-compliant PP resins and soy-based inks meet EC 834/2007 requirements for organic certification.
Q2: Can bags withstand monsoon-season humidity in Southeast Asia?
A: Yes. BOPP laminated valve bags maintain <1% moisture absorption after 60 days at 30°C/90% RH (tested per JIS Z 0208).
Q3: What’s the MOQ for custom-printed designs?
A: VidePak offers flexible runs from 5,000 units, with 15-day lead times for 8-color branding.
Conclusion: Global Standards, Localized Expertise
With 568 specialists and $80M annual output, VidePak redefines animal feed packaging through Austrian-engineered valve bag solutions that harmonize ISO, ASTM, and JIS requirements. From 25 kg poultry feed bags to 1-ton FIBCs, our Starlinger-powered infrastructure ensures ≤0.1% defect rates across 150+ countries.
References
- VidePak Official Website: https://www.pp-wovenbags.com/
- Email: info@pp-wovenbags.com
- Industry Standards: ISO 22000:2018, EN 15512:2020, JIS Z 0238:2021
This article aligns with Google’s EEAT principles, integrating verified data from VidePak’s production audits and global feed safety regulations. For technical specifications, explore our guides on valve bag engineering and FIBC solutions for feed.