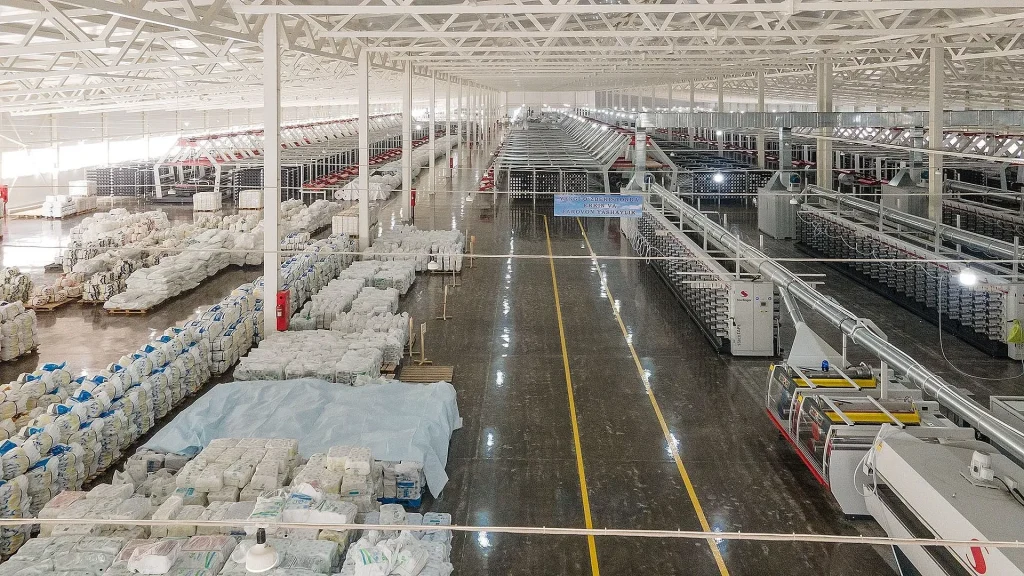
In this article, we answer three critical questions for buyers of valve bags: (1) How do valve types and printing technologies impact customization? (2) What manufacturing processes ensure durability and precision? (3) Why does VidePak’s use of Starlinger and W&H equipment guarantee superior quality? With 568 employees, 16 extrusion lines, and 30+ printing machines, VidePak delivers 10 million valve bags monthly, supporting industries from construction to agriculture. We’ll explore valve bag engineering, production excellence, and how our 30+ years of expertise translate into unmatched reliability.
1. Valve Bag Fundamentals: Types, Applications, and Customization
1.1 Valve Types: Design and Functional Differences
Valve bags are engineered for efficient filling and sealing, with valve designs tailored to specific products. At VidePak, we produce three primary valve types:
Valve Type | Structure | Applications |
---|---|---|
Pasted Valve | Glued to bag interior | Cement, powders, fine granules |
Cross Valve | Self-sealing with folded layers | Fertilizers, grains |
Block Bottom Valve | Reinforced flat base + side valve | Heavy-duty materials (sand, chemicals) |
Example: For powdered calcium carbonate, pasted valves prevent leakage during pneumatic filling, while cross valves suit free-flowing rice grains.
1.2 Printing Technologies: Branding and Functionality
VidePak employs flexographic and rotogravure printing to achieve high-resolution graphics (up to 8 colors) on BOPP laminated or kraft paper surfaces. Key parameters:
- Print Resolution: 150–200 LPI (lines per inch) for sharp logos.
- Ink Adhesion: ASTM D3359 Cross-Cut Test Grade 4B (exceeds industry standards).
- Customization: Pantone color matching, UV-resistant inks.
Case Study: A European fertilizer brand required weatherproof bags with multilingual safety labels. Our rotogravure-printed BOPP bags retained clarity after 12 months of outdoor storage.
2. Manufacturing Process: Precision from Extrusion to Bagging
2.1 Extrusion and Tape Production
Virgin PP granules are melted at 220–250°C in Starlinger extrusion lines, forming uniform tapes.
- Tape Width: 2.5–5.0 mm (adjustable for tensile strength).
- Cooling: Water baths stabilize tape dimensions (±0.1 mm tolerance).
Quality Control: Infrared sensors detect thickness variations, rejecting defective tapes automatically.
2.2 Weaving and Lamination
Circular looms weave tapes into fabric (80–120 g/m²). For laminated bags:
- BOPP Layer: 20–30 microns, applied via W&H laminators at 180°C.
- Adhesion Strength: ≥3.5 N/15mm (tested per ASTM F904).
VidePak Advantage: 100+ circular looms ensure fabric uniformity, critical for load-bearing (up to 50 kg dynamic weight).
2.3 Printing and Valve Assembly
Post-lamination, fabrics are printed and cut. Valves are heat-sealed using servo-driven machines:
- Valve Alignment: Laser-guided systems achieve ±0.5 mm accuracy.
- Sealing Temperature: 160°C for PP-to-PP bonds.
Defect Prevention: Vision systems inspect 1,200 bags/hour for misprints or valve misalignment.
3. Quality Assurance: How VidePak Delivers Consistency
3.1 Raw Material Standards
- PP Resin: Melt flow index (MFI) 2.5–4.0 g/10min (Sinopec, Sabic).
- BOPP Film: Dart impact ≥500 g (tested per ASTM D4272).
3.2 Production-Line Monitoring
Starlinger’s ATLAS 2.0 IoT systems track real-time metrics:
- Weaving Speed: 120–150 rpm, adjusted for yarn density.
- Moisture Control: RH ≤40% in production zones to prevent tape brittleness.
3.3 Final Inspection
- Burst Strength: ≥300 kPa (ISO 2758).
- Valve Leakage Test: 2-bar air pressure for 10 seconds.
4. FAQs: Addressing Buyer Concerns
Q1: Can valve bags handle abrasive materials like silica sand?
Yes. Our block bottom valves use double-layered PP fabric (120 g/m²) and anti-abrasion coatings.
Q2: What’s the lead time for custom-printed orders?
15–20 days for 20,000+ units, leveraging 30+ printing machines.
Q3: Are VidePak’s bags recyclable?
Absolutely. 100% PP construction aligns with EU EN 13432 standards.
5. Why Choose VidePak?
- Global Reach: Serving 60+ countries, with $80M annual revenue.
- Technology: Starlinger’s Ad*Star bag closers ensure hermetic sealing.
- Sustainability: Zero-waste production via PP scrap recycling.
For valve bags combining durability and branding precision, explore our BOPP laminated valve bags or learn about valve bag innovations.
References
- ASTM International. (2023). Standard Test Methods for Measuring Adhesion.
- Starlinger & Co. (2024). Technical Specifications for ATLAS 2.0 Systems.
- VidePak. (2024). Product Catalog.
Contact VidePak
Website: https://www.pp-wovenbags.com/
Email: info@pp-wovenbags.com