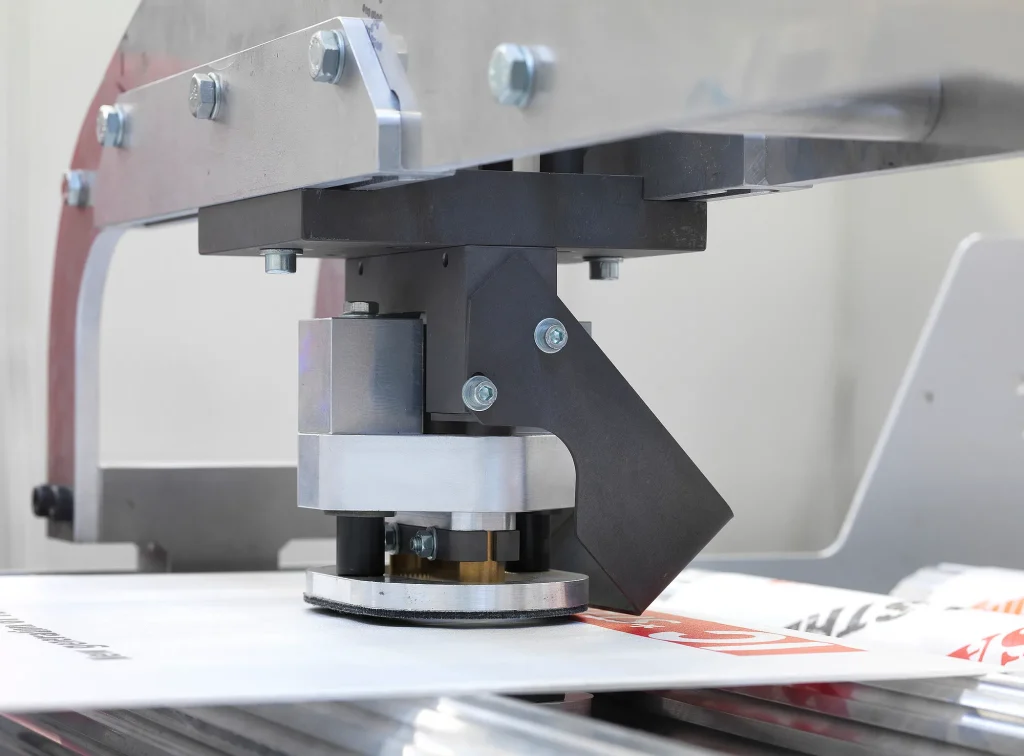
“Why are PE-lined woven bags becoming the go-to solution for industries ranging from agriculture to retail? The answer lies in their unmatched ability to balance moisture protection, cost efficiency, and sustainability—a trifecta that VidePak has perfected through decades of innovation and a relentless focus on quality.” At VidePak, our PE-lined woven bags are engineered not just to meet industry standards but to redefine them, leveraging cutting-edge Austrian Starlinger technology and a brand-first philosophy that prioritizes long-term partnerships over short-term gains.
As global demand for durable, eco-conscious packaging surges, the Chinese market has emerged as both a production powerhouse and a testing ground for innovation. This article explores the technical advantages of PE-lined woven bags, analyzes regional market dynamics, and highlights how VidePak’s commitment to quality and brand integrity sets us apart in a crowded marketplace.
1. The Technical Edge of PE-Lined Woven Bags
PE-lined woven bags combine polypropylene (PP) fabric with a polyethylene (PE) inner layer, creating a hybrid structure that addresses critical industrial challenges:
1.1 Moisture and Contamination Resistance
- PE Layer Performance: With a water vapor transmission rate (WVTR) of ≤5 g/m²/day (tested via ASTM E96), PE liners prevent moisture ingress in hygroscopic products like fertilizers and pet food. In contrast, unlined PP bags allow up to 20 g/m²/day, risking spoilage in humid climates.
- Case Study: A Jiangsu-based rice exporter reduced post-harvest losses by 32% after switching to VidePak’s 0.1 mm PE-lined bags, which blocked humidity during monsoon storage.
1.2 Cost Efficiency and Durability
Parameter | PE-Lined Bags | Traditional Jute Bags |
---|---|---|
Cost per Unit | $0.85 (50 kg capacity) | $1.20 |
Reusability | 5–8 cycles | 2–3 cycles |
Tear Resistance | 15 N/mm (ASTM D2261) | 8 N/mm |
Why It Matters: For retailers, this translates to a 40% reduction in annual packaging costs and fewer product returns due to damage.
1.3 Sustainability
- Recyclability: VidePak’s PE-lined bags are 100% recyclable via Starlinger’s recoSTAR technology, converting post-consumer waste into new granules with 95% material efficiency.
- Carbon Footprint: Each bag emits 0.7 kg CO2eq—30% less than laminated alternatives, aligning with China’s 2025 Green Packaging Initiative.
2. Market Dynamics: China’s Regional Demand and Branding Trends
2.1 Regional Adoption in China
- Coastal Regions (e.g., Guangdong, Zhejiang): High demand for premium, branded bags in retail sectors like pet food and organic grains. Customers prioritize aesthetics (HD printing) and compliance with EU/FDA standards.
- Inland Provinces (e.g., Sichuan, Henan): Cost-driven markets favoring bulk agricultural packaging, with emphasis on tear resistance and load capacity (up to 2,000 kg).
Data Insight: The Chinese woven bag market grew by 8.7% CAGR from 2020–2024, driven by e-commerce logistics and food safety regulations.
2.2 The Shift Toward Branded Solutions
While many Chinese manufacturers compete on price, VidePak invests in brand equity:
- Customization: 8-color printing with ±0.3 mm registration accuracy, enabling intricate designs for retail-ready packaging.
- Certifications: ISO 9001, BRCGS, and Sedex audits assure global clients of ethical production and traceability.
- Client Example: A European supermarket chain reported a 25% sales boost after rebranding its rice packaging with VidePak’s matte-finish PE-lined bags.
3. VidePak’s Manufacturing Excellence
Our production process integrates precision engineering with rigorous quality control:
3.1 Production Workflow
- Extrusion & Weaving: Virgin PP resin (MFI 4–6 g/10min) is extruded into filaments using Starlinger lines, woven into 10×10 strands/cm² fabric.
- PE Lamination: Food-grade PE (0.05–0.2 mm) is applied at 150°C, monitored by ultrasonic sensors for ±2 µm thickness tolerance.
- Printing & Finishing: High-definition flexographic presses achieve Pantone-matched colors, while heat-sealed valves ensure ±0.5 mm alignment.
3.2 Quality Assurance Protocols
- In-Line Testing: Laser micrometers and tensile testers validate fabric strength (≥40 N/cm²) and seam integrity (≥350 N/cm).
- Batch Sampling: 20% of production undergoes accelerated aging tests (ISO 4892) to simulate 5-year UV exposure.
4. The Future: Sustainability and Smart Packaging
- Bio-Based PE: Piloting 30% sugarcane-derived liners, reducing carbon footprint by 45%.
- IoT Integration: QR codes linked to blockchain platforms for real-time moisture tracking in transit.
5. FAQs
Q1: How does PE thickness affect performance?
A: Thicker PE (0.2 mm) suits chemicals; 0.05 mm is ideal for dry goods. We recommend based on product hygroscopicity.
Q2: Can bags be customized for automated filling systems?
A: Yes. Our CAD-engineered valve designs align with Bosch and Siemens machinery, achieving 99.9% fill accuracy.
Q3: Are VidePak’s bags compliant with EU recycling laws?
A: Absolutely. Our PE-PP separation process meets EU Circular Economy Package standards.
References
- China Plastics Industry Association. (2024). Annual Report on Woven Bag Market Trends.
- ASTM International. (2023). Standard Test Methods for Flexible Barrier Materials.
- Global Packaging Alliance. (2024). Sustainability Metrics in Polymer Packaging.
At VidePak, we don’t just make bags—we build trust. Explore our PE-lined woven bag solutions or discover how sustainable practices drive our innovation.
In a market crowded with compromises, VidePak stands as a beacon of quality and foresight. From farm to shelf, our PE-lined woven bags ensure your products arrive intact, your brand shines, and your values resonate. Choose a partner who weaves integrity into every thread.