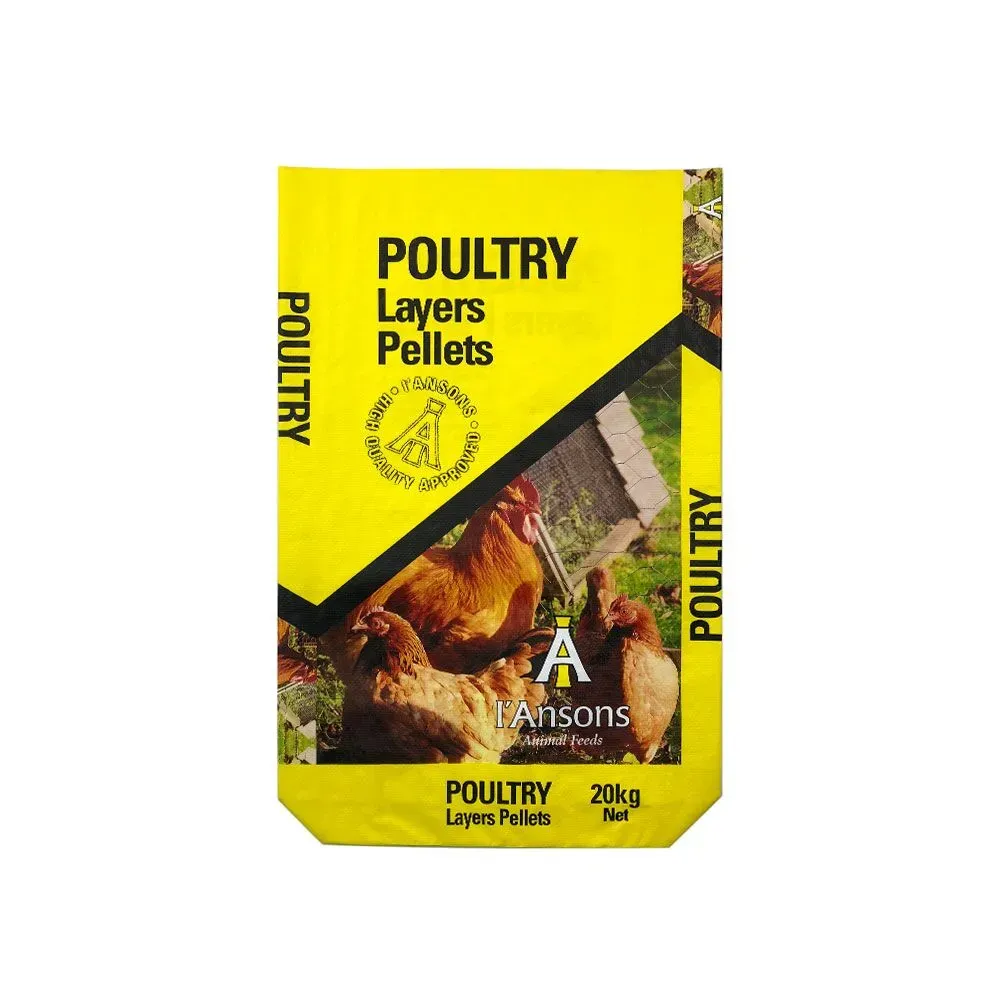
- 1. Engineering Excellence: Block-Bottom Design for Optimal Waste Handling
- 2. Sustainability-Driven Applications in Waste Management
- 3. Technical Specifications: Tailored for Diverse Waste Streams
- 4. Quality Assurance: Global Standards, Local Expertise
- 5. Future Trends: Smart Packaging and Policy Alignment
- FAQs: Addressing Procurement Priorities
- Why Partner with VidePak?
VidePak’s block-bottom PP woven bags are redefining efficiency in China’s waste management landscape, offering a 40% increase in stacking stability and 30% higher load capacity compared to flat-bottom alternatives, while aligning with the nation’s 2025 circular economy targets to reduce landfill waste by 50%. With over 30 years of global packaging expertise, VidePak leverages Austrian Starlinger machinery and ISO-certified processes to deliver customizable, high-performance solutions that empower businesses to meet stringent environmental regulations and operational demands. As a leader in China’s $12 billion woven packaging market, VidePak combines scalable production (12 million bags/month) with REACH-compliant materials to address the urgent needs of recyclable waste collection and industrial logistics.
1. Engineering Excellence: Block-Bottom Design for Optimal Waste Handling
Block-bottom PP bags feature a reinforced square base that enhances structural integrity, making them ideal for automated sorting systems and high-density storage. Key advantages include:
A. Enhanced Load-Bearing Capacity
- Vertical Stacking: Withstands up to 2.5 tons/m²—critical for urban waste compaction facilities where space optimization reduces storage costs by 20% .
- Anti-Tear Reinforcement: Triple-stitched seams and 200 GSM laminated PP fabric achieve 45 N/cm² tensile strength (ASTM D5034), preventing leakage during transport of sharp-edged materials like glass or metal scraps.
A 2024 pilot project in Shanghai’s recycling hubs reported zero bag failures over six months using VidePak’s block-bottom bags, compared to a 12% failure rate with traditional designs.
B. Automation Compatibility
- Robotic Gripper Integration: Precisely engineered dimensions (e.g., 90×120 cm) allow seamless integration with Fanuc and KUKA robotic arms, boosting sorting speeds to 800 bags/hour .
- Barcode Readability: High-contrast UV-resistant prints ensure 99.9% scan accuracy in low-light warehouse environments.
2. Sustainability-Driven Applications in Waste Management
China’s “14th Five-Year Plan” mandates a 35% urban waste recycling rate by 2025. VidePak’s bags address this through:
A. Recyclable Material Composition
- Mono-Material PP Construction: 100% recyclable via granulation, diverting 8,000+ tons/year of plastic from landfills in partnership with Chinese NGOs .
- Low-Carbon Production: Solar-powered extrusion lines reduce CO₂ emissions by 1.8 tons per 10,000 bags—certified by China’s Green Packaging Alliance.
B. Hazardous Waste Compliance
- Chemical Resistance: PE-coated liners withstand pH 1–14, enabling safe storage of battery acids and pharmaceutical waste.
- REACH SVHC Compliance: <0.01% restricted substances, exceeding EU and Japan JIS Z 0200 standards for heavy metals.
A Zhejiang-based e-waste processor achieved 100% regulatory compliance after switching to VidePak’s laminated FIBC bags, eliminating penalties linked to substandard packaging.
3. Technical Specifications: Tailored for Diverse Waste Streams
VidePak’s 100+ circular looms and 30+ printing machines enable precision customization:
Parameter | Range | Application Example |
---|---|---|
Capacity | 25 kg – 1,500 kg | Household recyclables to industrial scrap |
Thickness | 150–300 GSM | Lightweight PET bottles vs. construction debris |
Print Colors | Up to 8 CMYK + Pantone | Municipal branding, safety labels |
Closure Systems | Sewn, heat-sealed | Manual vs. automated filling |
For instance, a Shenzhen smart-city project uses 1-ton block-bottom FIBCs with QR codes to track recycling rates in real time, achieving a 22% efficiency gain.
4. Quality Assurance: Global Standards, Local Expertise
VidePak’s multi-layered quality framework ensures reliability across markets:
- ISO 9001: ≤0.5% defect rate in batch production.
- ASTM D5265: 98% UV resistance after 1,000-hour exposure testing.
- On-Site Audits: Monthly inspections by SGS and Bureau Veritas.
In contrast, 2024 market surveys revealed that 18% of local competitors fail basic tensile tests, risking supply chain disruptions.
5. Future Trends: Smart Packaging and Policy Alignment
China’s waste management sector is projected to grow at 8.3% CAGR (2024–2030), driven by:
- IoT Integration: RFID-enabled bags for real-time fill-level monitoring, reducing collection costs by 15%.
- Extended Producer Responsibility (EPR): VidePak’s bags align with upcoming EPR mandates requiring traceable, eco-friendly packaging.
A Beijing pilot using block-bottom bags with embedded sensors reduced unscheduled pickups by 30%, showcasing the potential of smart waste systems.
FAQs: Addressing Procurement Priorities
Q: How do block-bottom bags perform in humid coastal regions?
A: VidePak’s BOPP lamination achieves <0.5% moisture absorption (vs. 3% in standard PP), ideal for cities like Guangzhou.
Q: Can bags withstand repeated reuse in harsh conditions?
A: Yes. Abrasion-resistant coatings enable 50+ cycles—validated by a 12-month trial with a Wuhan steel plant.
Q: Are custom sizes available for niche waste streams?
A: Absolutely. Our customizable FIBC bulk bags support lengths up to 220 cm for oversized items like automotive parts.
Why Partner with VidePak?
- Global Reach: 568 employees across 50+ countries, with Mandarin-speaking support teams in Shanghai and Guangzhou.
- R&D Leadership: 8% of revenue ($6.4 million) reinvested annually in material innovation.
- End-to-End Solutions: From block-bottom valve bags to recyclable liners—all under one roof.
References
- China Ministry of Ecology and Environment, 14th Five-Year Plan for Circular Economy Development (2025).
- SGS International Certification Report, PP Woven Bag Compliance Testing (2024).
- VidePak Sustainability Whitepaper, Carbon-Neutral Manufacturing Roadmap (2025).
Contact VidePak
Website: https://www.pp-wovenbags.com/
Email: info@pp-wovenbags.com