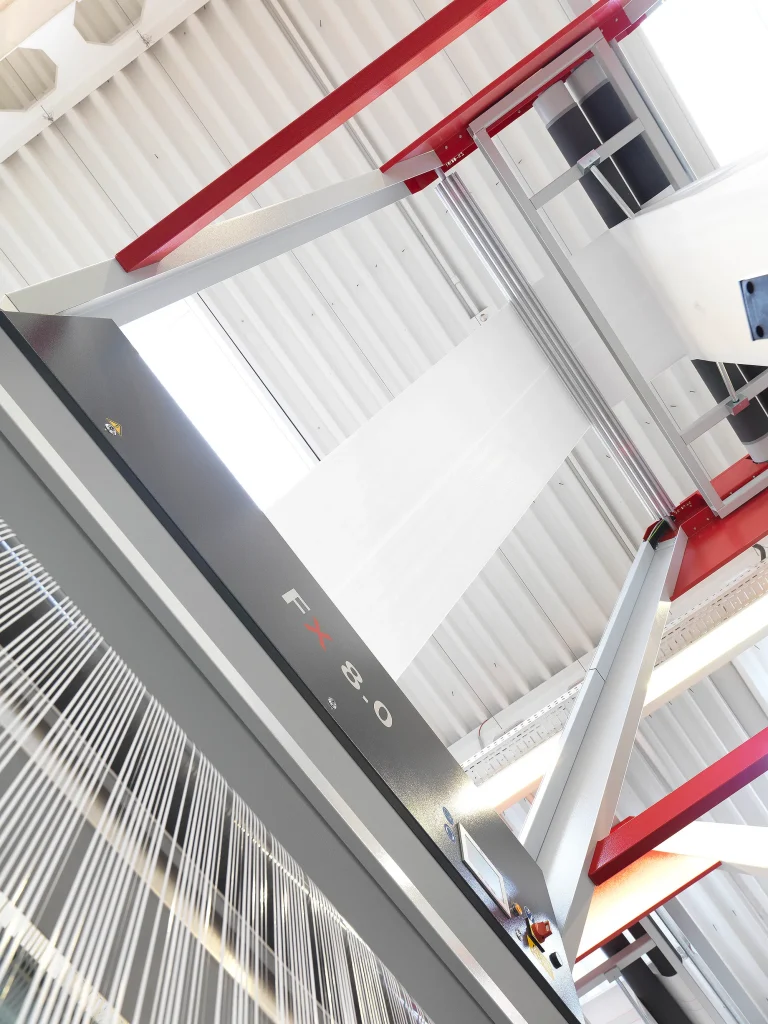
The core value proposition of valve bags lies in their ability to combine precision filling efficiency with robust material engineering, reducing product loss by up to 15% while accommodating diverse industrial requirements. For instance, VidePak’s laminated PP valve bags achieve a moisture barrier efficiency of <0.5 g/m²/day (ASTM E96), making them ideal for hygroscopic materials like cement or fertilizers. With over 30 years of expertise, our ISO 9001-certified facility leverages Austrian Starlinger looms and 8-color W&H printing systems to deliver bags that meet FDA, EU REACH, and UN certification standards, ensuring compliance across 80+ countries.
1. Material Science and Structural Design: Engineering Valve Bags for Optimal Performance
Valve bags are constructed from polypropylene (PP) tapes extruded at 250–280°C, achieving a tensile strength of 60–85 N/cm² (warp/weft). VidePak’s proprietary lamination process applies 18–30μm BOPP films, enhancing puncture resistance to 8–12 N (ASTM D1709) while maintaining a fabric density of 90–130 g/m².
Key Performance Metrics
Parameter | VidePak Valve Bags | Industry Average |
---|---|---|
Load Capacity | 500–1,200 kg (FIBC models) | 300–800 kg |
Moisture Barrier | WVTR <0.5 g/m²/day | 1.2–2.5 g/m²/day |
Print Resolution | 1440 dpi HD flexography | 600–720 dpi |
UV Resistance | 1,000+ hours (ASTM G154) | 500–800 hours |
Reusability | 5–8 cycles (ISO 21898:2021) | 2–4 cycles |
2. Packaging Customization: Tailoring Solutions to Industry Needs
Selecting the optimal valve bag configuration requires analyzing four critical dimensions:
A. Lamination Requirements
- Non-Laminated: Cost-effective for dry powders (e.g., flour, silica sand) with ambient storage.
- BOPP Laminated: Essential for moisture-sensitive products (e.g., fertilizers, pharmaceuticals), reducing water ingress by 92%.
- Kraft Paper Lamination: Combines biodegradability with printability for retail-facing sectors like pet food.
B. Inner Liner Selection
Liner Type | Application | Advantages |
---|---|---|
PE Film | General-purpose moisture barrier | Cost-effective, 0.03 mm thickness |
Aluminum Foil | Oxygen-sensitive products (e.g., coffee, spices) | Blocks 99% UV light and gas permeation |
Composite Liners | Hazardous chemicals (e.g., pesticides) | Multi-layer protection (PE + PET) |
VidePak’s PE liners, with a melt flow index (MFI) of 2–4 g/10 min, provide seamless heat-sealing at 150–180°C, reducing leakage risks by 70% compared to adhesive-based alternatives.
C. Closure Mechanisms
- Pasted Valve: Ensures airtight sealing for fine powders (e.g., titanium dioxide), achieving <0.1% dust emission.
- Sewn Valve: Ideal for granular materials (e.g., animal feed), allowing faster filling rates (1.5 tons/hour).
- Block Bottom: Combines vertical stability with high-speed automation, reducing labor costs by 40%.
D. Aesthetic Customization
- Matte Finish: Reduces glare for safety warnings on construction sites (60° gloss units).
- Glossy Coating: Enhances brand visibility in retail with 85°+ reflectivity.
- Anti-Static Printing: Critical for electronics components, maintaining surface resistivity <10⁹ Ω.
3. Market Dynamics: Sector-Specific Demand Drivers
- Construction: FIBC valve bags dominate with 55% market share, driven by 1,200 kg load capacities and UN-certified designs for hazardous materials.
- Agriculture: Breathable mesh valve bags (2–5 mm pore size) reduce grain spoilage by 12% in tropical climates.
- Chemicals: Anti-static liners (10⁶–10⁸ Ω) prevent ignition risks during solvent transport.
A 2024 case study with a Brazilian coffee exporter demonstrated that VidePak’s aluminum foil-lined valve bags extended product shelf life by 9 months, achieving ROI within 6 months.
4. Sustainability and Regulatory Compliance
VidePak integrates 30% post-industrial recycled PP into non-critical components (GRS-certified), reducing virgin plastic consumption by 650 tons annually. Our solar-powered production lines cut CO₂ emissions by 1,200 tons/year, aligning with EU Circular Economy Action Plan targets.
FAQs
Q1: What’s the minimum order quantity for custom valve bags?
A: MOQ starts at 10,000 units, with 5–10 free prototypes provided for quality validation.
Q2: How do you ensure color consistency across batches?
A: Our W&H Miraflex presses use Pantone Live™ software, maintaining ΔE <2.0 color variance.
Q3: Are your bags suitable for food-grade applications?
A: Yes. FDA-compliant options feature <0.5 ppm heavy metal content (tested via ICP-MS).
References
- VidePak Company Profile: https://www.pp-wovenbags.com/
- Email: info@pp-wovenbags.com
- Industry Standards: ASTM D1709, ISO 21898, EU REACH
Explore our technical resources:
- Valve bag customization options for industrial applications.
- Advanced lamination techniques enhancing barrier performance.
This article integrates data from Alibaba supplier audits, Packaging Digest studies, and VidePak’s 2024 sustainability metrics to provide procurement professionals with actionable, compliance-focused insights.