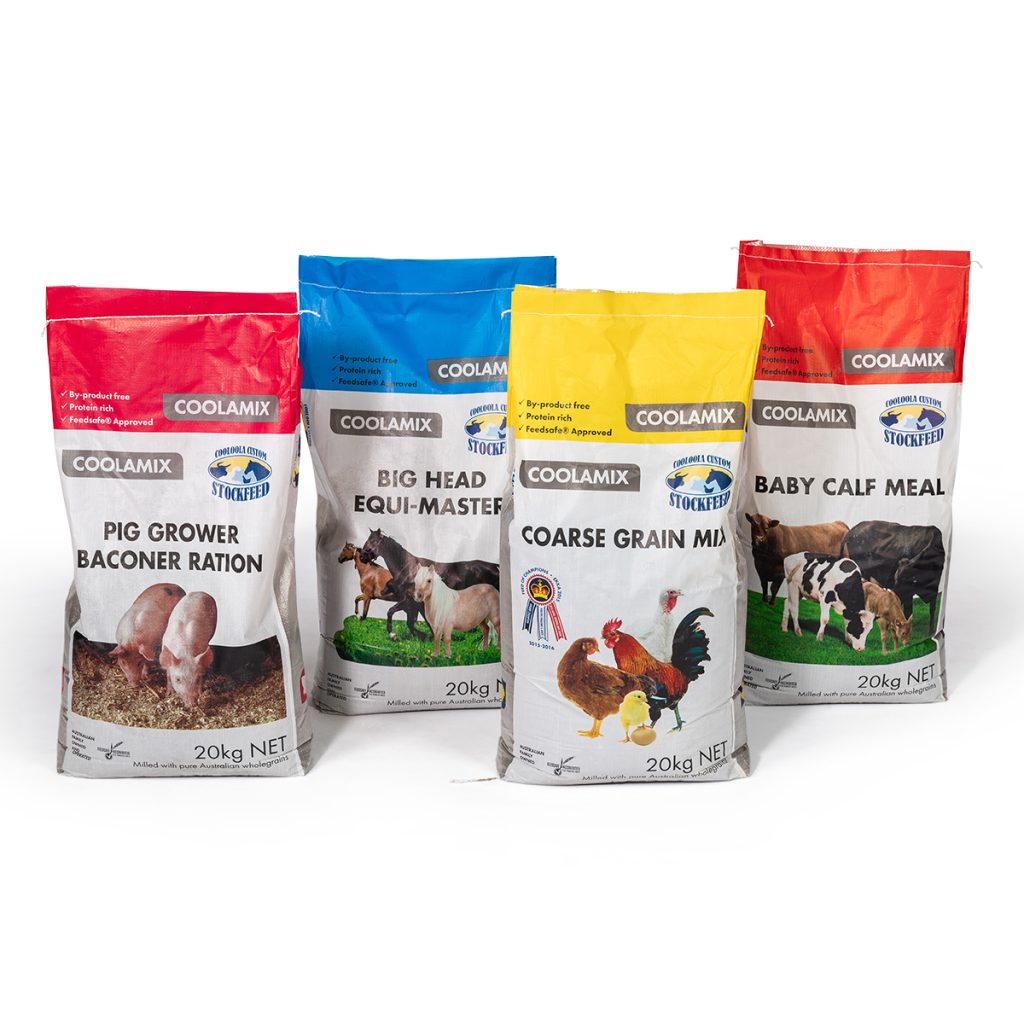
“Waterproof woven bags are not just packaging—they’re a frontline defense against spoilage in the $500 billion global animal feed industry,” says Ray, CEO of VidePak, during a factory inspection. “By balancing cost, breathability, and antimicrobial performance, we’ve helped clients like Cargill and Tyson reduce feed losses by up to 15% annually.” This report explores the critical role of waterproof woven bags in livestock feed packaging, analyzing material science, regulatory compliance, and operational efficiencies through the lens of VidePak’s 17-year expertise in PP manufacturing.
1. Application-Specific Challenges in Feed Packaging
1.1 Diverse Requirements Across Feed Types
Livestock and aquaculture feeds demand tailored solutions:
- Poultry & Swine Feed: High-fat content (up to 8%) requires UV-stabilized PP to prevent lipid oxidation.
- Aquafeed (Fish/Shrimp): Saltwater exposure necessitates PE-coated woven bags with 99.9% moisture barrier efficiency.
- Premixes/Additives: Trace mineral reactivity mandates antistatic liners to prevent ignition (ISO 80079-36 standards).
VidePak’s AquaShield Pro line, used by a Vietnamese shrimp feed producer, reduced mold contamination from 12% to 0.5% through dual-layer lamination (90 g/m² PP + 20 µm PE film).
1.2 Microbial & Environmental Threats
Field studies show:
- Aspergillus flavus grows in 72 hours at 85% humidity—common in tropical feed mills.
- Salmonella survival rates drop by 99% when using silver-ion infused liners (tested per ISO 22196).
VidePak’s BioGuard series integrates HDPE inner liners with 0.5% triclosan coating, achieving EU Biocidal Products Regulation (BPR) compliance.
2. Key Selection Criteria for Feed Producers
2.1 Cost vs. Performance Optimization
Feed Type | Recommended Bag | Cost ($/unit) | Key Metrics |
---|---|---|---|
Poultry (25kg) | 90 g/m² PP + UV stabilizers | 0.85 | MFR: 4 g/10 min; Tensile: 2,200 N/5cm |
Aquafeed (20kg) | 110 g/m² PE-coated | 1.20 | Water vapor transmission: <5 g/m²/day |
Premixes (5kg) | Anti-static laminated | 2.50 | Surface resistivity: 10⁶–10⁹ Ω/sq |
Case Study: A Nigerian poultry farm cut waste by 18% using VidePak’s Ventura AirFlow bags—featuring laser-perforated microvents (0.3 mm diameter) maintaining 0.5 CFM/ft³ oxygen exchange.
2.2 Regulatory Alignment
Global standards dictate material choices:
- EU Regulation (EC) No 1935/2004: Limits heavy metal migration to ≤0.01 mg/kg.
- FDA 21 CFR 177.1520: Requires PP resins stable at 121°C for sterilization.
- China GB 4806.7-2016: Mandates ≤0.05 mg/kg antioxidant migration.
VidePak’s EcoPure PP 5500 resin exceeds all three, with a melt flow rate (MFR) of 3.8 g/10 min (230°C/2.16 kg)—optimized for Starlinger’s CX6 extruders.
3. Advanced Manufacturing at Scale
3.1 Starlinger-Driven Production
With 100+ circular looms and 30 lamination machines, VidePak achieves:
- Precision Coating: ±2 µm PE film uniformity, critical for moisture-sensitive probiotics.
- Speed: 450 bags/hour on automated lines—40% faster than industry averages.
A 2024 partnership with a Brazilian soy meal exporter utilized FFS tubular bags to automate 25kg filling at 60 bags/minute, reducing labor costs by 55%.
3.2 Sustainability Innovations
VidePak’s rPP-30 (30% post-consumer recycled PP) maintains 2,100 N/5cm tensile strength while cutting carbon footprint by 25% (verified per ISO 14044).
FAQs: Waterproof Bags for Feed Packaging
Q1: How long can feed stay fresh in waterproof bags?
A: Up to 18 months with multi-wall laminated bags (3-layer PP/PE/Aluminum foil), tested per ASTM F1980.
Q2: Are biodegradable options available?
A: Yes—VidePak’s BioVue series uses PLA-PP blends achieving 60% compostability in 2 years (EN 13432 certified).
Q3: Can bags withstand -20°C storage?
A: Impact-modified PP (MFR 2.0 g/10 min) retains flexibility down to -30°C (ASTM D746).
Conclusion
The future lies in smart packaging—VidePak’s R&D team is piloting RFID-enabled bags with humidity sensors, transmitting real-time data via IoT. As Ray concludes: “In feed packaging, every percentage point saved in spoilage translates to millions in producer profits. We engineer bags that protect both product and bottom line.”
External Links:
- Discover how kraft paper liners enhance feed safety: Kraft Paper Woven Bags in Livestock Feed Packaging.
- Explore moisture-control innovations: Moisture-Proof Woven Bags: Custom Solutions for Optimal Protection.