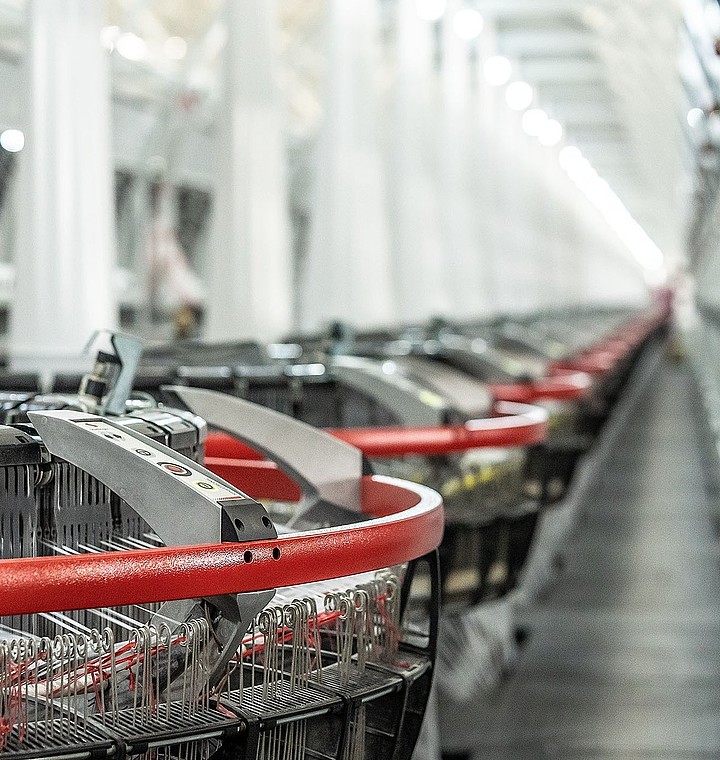
When considering packaging solutions, the materials and processes used in manufacturing can significantly impact both the cost-effectiveness and the sustainability of your operation. Among the options available, HDPE fabric bags (High-Density Polyethylene) are becoming a popular choice for a range of industries, including agriculture, chemicals, and construction. These bags not only offer various advantages over other materials but also ensure the protection of the contents, while being cost-efficient and eco-friendly.
In this article, we will delve into the benefits of using HDPE fabric bags, particularly in comparison to other fabric options such as PP fabric bags, and also explore the impact of advanced packaging technology in optimizing the efficiency of the entire packaging process. This includes the use of heavy-duty packaging machines and solutions like pallets and shrink-wrap, which together help improve packaging, transportation, and logistics.
The Advantages of Using HDPE Fabric Bags
HDPE fabric bags offer a number of advantages when it comes to durability, cost-effectiveness, and versatility. They are often used as an alternative to more conventional fabric types like woven polypropylene (PP) fabric bags or Kraft paper woven bags. Here’s a breakdown of why HDPE stands out:
- Strength and Durability:
HDPE is known for its high strength-to-density ratio. This makes HDPE fabric bags significantly more durable than other alternatives such as woven fabric sacks made from PP. HDPE fibers are tightly woven, creating a fabric that can withstand high tensile forces, heavy loads, and extreme environmental conditions. Whether for bulk packaging of industrial materials, agricultural products, or food items, HDPE fabric bags hold up much better under stress compared to their counterparts. - Lightweight Yet Sturdy:
Despite their strength, HDPE fabric bags are relatively lightweight, which contributes to lower shipping costs without sacrificing the durability needed for transporting heavy loads. This is particularly beneficial in industries such as construction and agriculture, where large quantities of products need to be transported efficiently. - Weather Resistance:
Unlike paper or other organic materials, HDPE fabric bags are highly resistant to moisture, UV rays, and various chemicals. This makes them ideal for both indoor and outdoor storage and transportation. For example, HDPE fabric bags are often used for storing fertilizer, grain, and sand, where moisture protection is a necessity. The resistance to weather conditions also ensures that the bags maintain their integrity during transit and storage, even in harsh climates. - Eco-Friendly Option:
HDPE fabric bags are recyclable, which makes them a sustainable option in industries where environmental impact is a concern. In comparison, materials like paper or standard PP fabric bags are less eco-friendly in the long run. Given that HDPE is made from recyclable plastic, these bags can be reused or repurposed, contributing to waste reduction and circular economy practices. - Customizable Options:
Similar to PP fabric bags, HDPE fabric bags can be custom-designed with various printing options for branding or identification. This is especially beneficial for industries where brand recognition is important, or for businesses that need to meet regulatory packaging standards.
Table 1: Comparison of HDPE Fabric Bags with Other Materials
Property | HDPE Fabric Bags | PP Fabric Bags | Kraft Paper Bags |
---|---|---|---|
Strength | Very strong, tear-resistant | Strong but less than HDPE | Moderate strength, prone to tearing |
Weight | Lightweight | Lightweight | Heavier compared to synthetic options |
Moisture Resistance | Excellent (waterproof) | Moderate | Poor, vulnerable to moisture |
UV Resistance | High | Moderate | Poor |
Recyclability | Fully recyclable | Fully recyclable | Not recyclable in all cases |
Customization | High (printing, size, design) | High (printing, size, design) | Moderate (limited design options) |
Environmental Impact | Low (eco-friendly) | Moderate (plastic waste) | Higher (paper production) |
Why Advanced Packaging Machines Enhance Efficiency
Another critical component of the packaging process is the machinery used to pack and ship products. At VidePak, we use a 200-ton packaging machine to compress and pack our woven fabric bags efficiently. This heavy-duty machine not only increases production speed but also ensures that the bags are packed tightly and securely, optimizing the space within containers. Let’s explore why this is an essential advancement for the packaging industry.
- More Efficient Space Utilization:
Traditional packaging methods often result in wasted space in containers. However, with a 200-ton packaging machine, the ability to tightly compress the woven fabric sacks maximizes space, allowing more products to be shipped within the same container. This reduces shipping costs, particularly when dealing with large quantities of materials that need to be transported over long distances. - Reduced Packaging Time:
Manual packaging or using older, less efficient machines often slows down production. However, modern machines like the 200-ton press significantly reduce the time needed to pack each individual product, enabling companies to meet tight deadlines without compromising on quality. - Better Protection for Products:
The tight compression applied by the machine ensures that the fabric woven bags do not suffer from damage during shipping. This is especially crucial when transporting fragile or sensitive items. The packaging also minimizes the risk of contamination, which is vital in industries like food processing and chemicals. - Automated and Reliable:
With automated systems, the packing process is far more consistent. The uniformity ensures that the products inside each woven fabric bag are not subject to human error, which can lead to inconsistencies in weight, size, or presentation. This is an essential feature for industries requiring strict standards.
Protection During Transportation with Pallets and Shrink-Wrap
In addition to using advanced packaging machines, securing the packaged products for transport is equally important. At VidePak, we ensure the highest protection by employing the use of pallets and shrink-wrap in conjunction with our HDPE fabric bags.
- Use of Pallets:
By placing woven fabric bags on sturdy pallets, we ensure that the products are easier to handle and can be moved efficiently in warehouses or during loading/unloading. The pallets also prevent the bags from being directly exposed to dirt, moisture, or other environmental factors. - Shrink-Wrap for Secure Protection:
After the fabric woven bags are loaded onto pallets, they are wrapped in shrink-wrap, which helps hold everything in place and protects the bags from shifting or sustaining damage during transit. This method is especially useful when transporting bags that are prone to movement or deformation. - Enhanced Protection During Transit:
With the combination of pallets and shrink-wrap, the transportation of goods becomes much more secure. The goods are less likely to suffer from physical damage, contamination, or environmental exposure. This solution is widely used for bulk shipping of various materials, including grains, chemicals, and construction materials, ensuring that they arrive at their destination in pristine condition.
Conclusion
The choice of packaging materials, like HDPE fabric bags, and the use of advanced machines and methods such as a 200-ton packaging press, palletizing, and shrink-wrapping, can significantly improve the efficiency of the entire supply chain. These innovations provide greater protection for products, reduce costs, and help companies meet modern sustainability standards.
For further information about the benefits and applications of woven fabric bags, you can explore this article on industrial woven packaging bags and learn more about our approach to customized fabric woven bags.