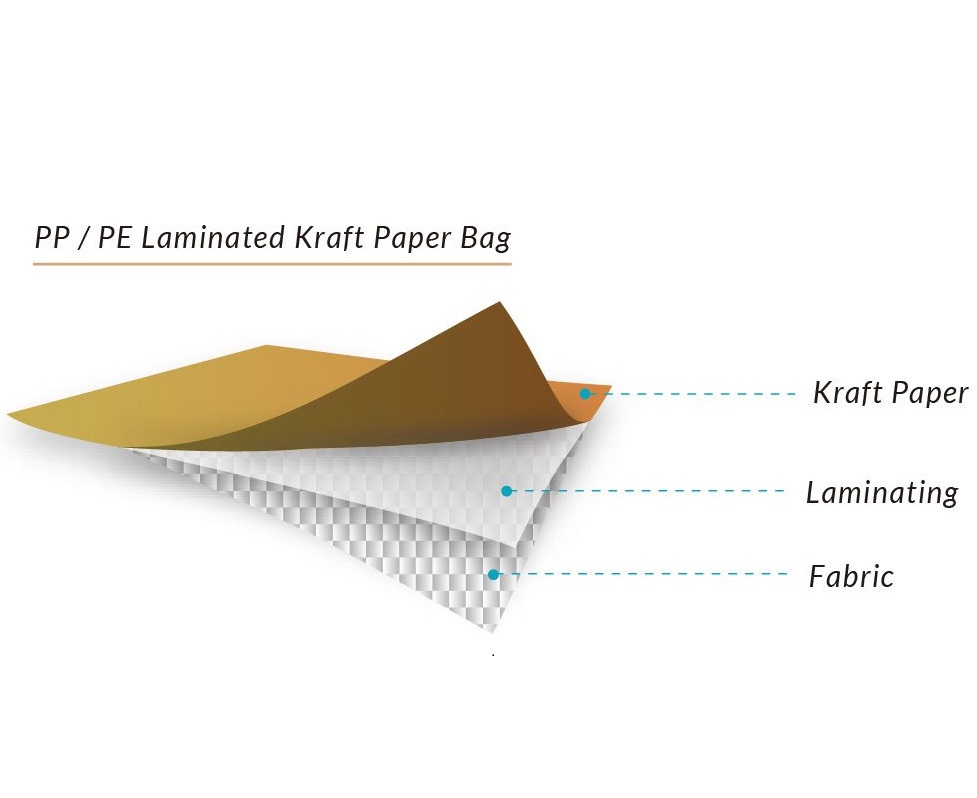
- 1. Enhanced Durability and Strength
- 2. Superior Protection Against Environmental Factors
- 3. Customization and Flexibility
- 4. Cost-Effectiveness
- 5. Environmental Benefits
- 1. Fine Filaments: Strength and Precision
- 2. Coarse Filaments: Durability and Economy
- 1. Starlinger Circular Looms
- 2. W&H Extrusion Lines and Printing Machines
- Frequently Asked Questions
In the world of packaging, the demand for stronger, more durable, and versatile bags continues to grow. Among the various types of woven bags available, multi-wall woven bags have gained significant traction in a wide array of industries, from agriculture to construction. These bags offer superior protection, customization, and cost-efficiency. But what exactly makes multi-wall woven sacks stand out, and why are laminated woven bags often the preferred choice for many businesses?
To answer these questions, it’s important to understand the unique benefits provided by multi-wall woven bags and the technology behind their creation, particularly when it comes to laminated PP bags. Let’s explore the reasons behind choosing these packaging solutions, particularly when high-performance materials like multi-wall woven bags are involved.
1. Enhanced Durability and Strength
One of the most significant benefits of multi-wall woven bags is their durability. These bags typically consist of multiple layers of woven fabric, usually made of polypropylene (PP) or polyester (PET), combined with a laminated layer for added strength and protection. This design allows multi-wall woven bags to withstand rough handling, transportation, and harsh weather conditions.
The lamination process adds a crucial layer of protection, especially for products that require additional shielding from moisture, dust, or contaminants. For instance, laminated woven bags are particularly effective in protecting agricultural goods or chemicals that are sensitive to external elements.
2. Superior Protection Against Environmental Factors
The multi-layer construction of laminated PP bags offers more than just durability; it also provides excellent protection against moisture, UV light, and physical damage. In industries where moisture resistance is essential—such as for storing grains or fertilizers—multi-wall woven sacks with a laminated layer serve as a safeguard against water infiltration, ensuring that products remain dry and uncontaminated during storage and transportation.
The added lamination not only protects the product inside but also helps to extend its shelf life by reducing the risk of spoilage or degradation.
3. Customization and Flexibility
When it comes to packaging, customization is key, and multi-wall woven bags shine in this area. Whether you need a specific size, a customized print design, or special closures like valves or open tops, these bags can be tailored to meet a wide range of requirements.
Laminated woven bags provide the perfect canvas for printing high-quality graphics, branding, and logos. This is a critical feature for companies looking to enhance their product visibility and appeal. With high-quality printing capabilities, businesses can create vibrant, eye-catching designs that make their products stand out on the shelves or during shipping.
4. Cost-Effectiveness
Another important reason for the growing preference for multi-wall woven bags is their cost-effectiveness. Despite their strength and customization options, these bags are relatively inexpensive compared to other types of packaging materials. The use of woven polypropylene (PP), a cost-effective material, combined with the lamination process, makes multi-wall woven bags a smart choice for businesses looking to balance quality and cost.
5. Environmental Benefits
Sustainability is at the forefront of modern packaging considerations, and laminated woven bags offer significant environmental benefits. The multi-layered construction of these bags allows for better recycling rates compared to single-layer alternatives. By using polypropylene, a recyclable material, multi-wall woven bags can be reused and repurposed for other packaging needs, helping businesses reduce their environmental footprint.
The Choice Between Fine and Coarse Filaments: How They Affect Performance
In addition to the advantages of multi-layered constructions, the choice of filament type—fine or coarse—also plays a critical role in the performance of multi-wall woven bags. Both fine and coarse filaments have distinct characteristics that make them suitable for specific applications.
1. Fine Filaments: Strength and Precision
Fine filaments, typically ranging from 0.10mm to 0.20mm in diameter, are well-known for their high tensile strength and uniformity. The use of fine filaments in multi-wall woven bags allows for greater precision in the weaving process, producing bags with tight, closely knit structures. This can be particularly beneficial when creating laminated PP bags where high resistance to punctures, tears, or abrasions is essential.
Fine filaments also contribute to higher fabric density, which results in smoother surfaces that are easier to print on, making them ideal for packaging solutions that require custom branding. They are commonly used for packaging fine powders, grains, or products where dust resistance and clean presentation are critical.
2. Coarse Filaments: Durability and Economy
On the other hand, coarse filaments, which have a larger diameter (usually over 0.20mm), are thicker and less dense than their fine counterparts. These filaments are stronger and can bear heavier loads, making them ideal for packaging heavier products.
In multi-wall woven bags for construction materials, chemicals, or fertilizers, coarse filaments provide the extra durability needed to hold large, bulk quantities of products. While they may not be as smooth as fine filaments, they excel in applications that demand load-bearing strength over aesthetics.
The use of coarse filaments in combination with laminated woven bags enhances the bag’s overall durability, particularly when it comes to heavy-duty use in harsh environments.
The Importance of Equipment in Fine and Coarse Filament Production
The performance and quality of multi-wall woven bags are not solely dependent on the material choice but also on the equipment used in their manufacturing. At VidePak, we employ state-of-the-art equipment from Starlinger (Austria) and W&H (Germany) to ensure that every woven bag meets the highest standards of quality and precision.
1. Starlinger Circular Looms
Starlinger is known for its advanced circular looms, which are essential for creating tightly woven fabrics from both fine and coarse filaments. These looms ensure that the filament strands are properly aligned and woven together to produce bags with the necessary strength, flexibility, and durability. The precision provided by Starlinger looms also minimizes production defects and enhances the performance of multi-wall woven bags, especially when it comes to high-stress applications like transporting heavy-duty products.
2. W&H Extrusion Lines and Printing Machines
When it comes to producing laminated woven bags, the extrusion lines and printing machines from W&H play a crucial role. W&H’s co-extrusion lines allow for the lamination of multiple layers, creating bags that are not only durable but also resistant to moisture and UV degradation. Their printing technology ensures that even complex designs can be printed with high accuracy, providing businesses with the ability to create customized branding solutions on multi-wall woven sacks.
The combination of these high-tech machines allows VidePak to produce superior quality laminated PP bags that meet diverse packaging needs while maintaining cost-efficiency.
Product Comparison and FAQs
Below is a quick comparison between fine and coarse filaments, and the impact they have on the performance of multi-wall woven bags:
Feature | Fine Filament | Coarse Filament |
---|---|---|
Diameter | 0.10mm – 0.20mm | >0.20mm |
Strength | High tensile strength | Stronger, load-bearing |
Applications | Lightweight products, high-end packaging | Heavy-duty products, construction |
Surface Smoothness | Smooth, ideal for printing | Rougher, less ideal for printing |
Durability | Good for puncture resistance | Best for impact resistance |
Frequently Asked Questions
1. What are the main applications for multi-wall woven bags?
Multi-wall woven bags are used in a variety of industries, including agriculture, chemicals, food packaging, and construction. They are ideal for products that need extra durability, protection from moisture, or custom branding.
2. Can laminated woven bags be customized for different uses?
Yes, laminated woven bags are highly customizable. Businesses can choose different sizes, closure types (valve or open mouth), and print designs to meet specific packaging needs.
3. What makes Starlinger and W&H equipment stand out in woven bag production?
The combination of Starlinger’s circular looms and W&H’s extrusion and printing lines ensures high precision and consistency, which is critical for producing durable, high-quality multi-wall woven bags and laminated woven bags.
4. Are multi-wall woven sacks environmentally friendly?
Yes, multi-wall woven sacks made from laminated PP bags are recyclable and can be reused for other packaging needs, making them an environmentally friendly option.
For more insights on the advancements in laminated woven bags, check out our detailed exploration on multi-wall woven bags and laminated woven bags.