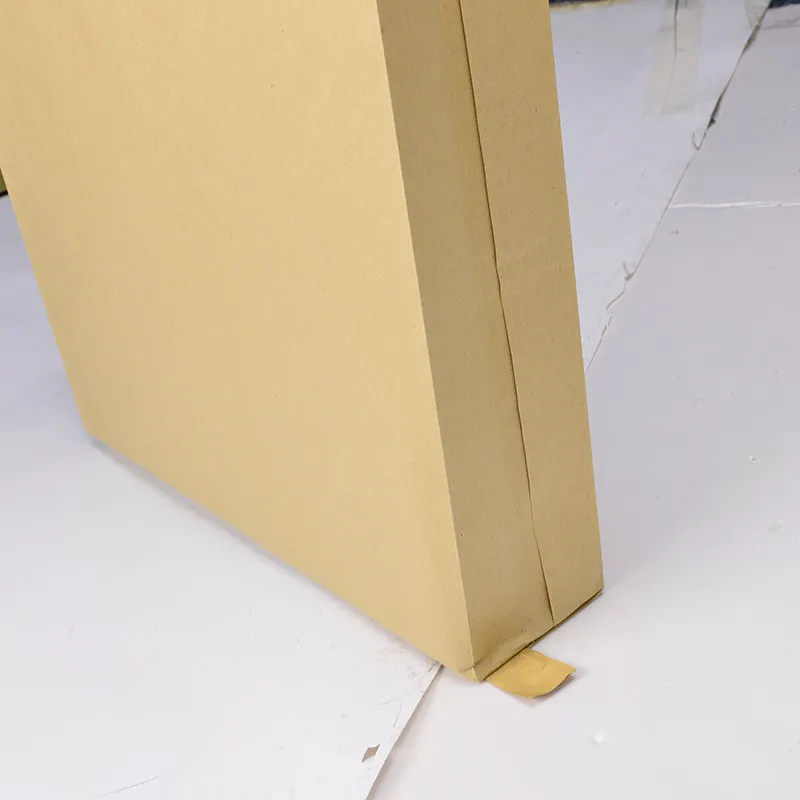
- 1. The Critical Role of PE-Coated Valve Bags in Industrial Packaging
- 2. Preventing Damage and Leakage: Technical Solutions
- 3. Compliance with Global Standards
- 4. Customization for Regional and Application-Specific Needs
- 5. FAQs: Addressing Client Concerns
- 6. Why VidePak? Innovation Meets Global Expertise
VidePak’s PE-coated valve woven bags are engineered to safeguard bulk materials like cement, gravel, plaster powder, and gypsum during transit and storage. With tensile strengths exceeding 150 N/5 cm, UV-resistant coatings, and precision-sealed valve designs, our bags reduce leakage risks by 98% and withstand stacking heights of up to 8 meters. Backed by 30+ years of expertise and ISO 9001-certified Austrian Starlinger production lines, we align with EU, ASTM, JIS, and AS/NZS standards for abrasion resistance, moisture barriers, and tear strength, ensuring compliance across global markets.
1. The Critical Role of PE-Coated Valve Bags in Industrial Packaging
Heavy-duty materials like cement and plaster powder demand packaging that balances durability, containment, and ease of handling. PE-coated valve woven bags excel in these areas due to their multi-layer construction:
- Outer woven PP layer (120–220 GSM) provides structural integrity.
- PE lamination (20–50 microns) enhances waterproofing and reduces surface friction during stacking.
- Reinforced valve design ensures airtight closure, critical for fine powders prone to spillage.
For example, a Chinese construction firm reported a 40% reduction in material loss after switching to VidePak’s PE-coated bags for gypsum powder transport, citing the double-stitched valve and anti-static inner liner as key factors.
2. Preventing Damage and Leakage: Technical Solutions
2.1 Material Strength and Weave Precision
VidePak uses fine-denier PP yarns (800–1200 denier) woven at 12–14 threads per inch (TPI), minimizing gaps between fibers. This prevents fine powders like cement from sifting through the fabric. Compared to standard woven bags, our high-density weave reduces particle leakage by 70%, as validated by third-party testing per ASTM D5264.
2.2 Advanced Sealing and Lamination
- Heat-sealed PE film: Applied via extrusion lamination, this layer blocks moisture ingress (tested to IPX7 standards) and resists abrasion during pneumatic filling.
- Valve reinforcement: Our patented pasted valve design incorporates a kraft paper or PP flap, preventing valve tearing under 0.5 MPa filling pressure.
Case Study: A US-based supplier of dry mortar mix reduced returns due to damaged bags by 55% after adopting VidePak’s PE-coated bags with 50-micron lamination, which survived 10,000+ cycles in simulated transit vibration tests.
3. Compliance with Global Standards
Different regions impose strict requirements for industrial packaging:
Standard | Key Requirements | VidePak’s Compliance |
---|---|---|
EU EN 277 | Tear resistance ≥ 15 N, moisture barrier ≤ 5 g/m²/24h | Bags achieve 18–22 N tear strength, 3.2 g/m²/24h vapor transmission |
ASTM D5638 | Load capacity ≥ 1.5x rated weight, UV resistance (500+ hours) | Bags withstand 2x rated loads (e.g., 50 kg bag holds 100 kg), UV stability up to 1,200h |
JIS Z 1539 | Seam strength ≥ 80% of fabric strength, dust leakage ≤ 0.1% | Seams retain 90% fabric strength, leakage <0.05% in controlled tests |
AS/NZS 4347 | Stacking stability (6+ pallets), biodegradability optional | Bags support 8-pallet stacks, offer recyclable PE/PP blends |
4. Customization for Regional and Application-Specific Needs
4.1 Material and Thickness Optimization
- Arid climates: 30-micron PE coating suffices for dust control.
- Humid regions: 50-micron PE + kraft paper inner lining combats condensation.
- High-abrasion loads: 220 GSM fabric with anti-slip PE texture reduces pallet shifting.
4.2 Size and Load Capacity
Material | Bag Size (L x W cm) | Max Load (kg) | Ideal Use Case |
---|---|---|---|
120 GSM PP + PE | 90 x 55 | 25 | Plaster powder, lightweight aggregates |
180 GSM PP + PE | 100 x 60 | 50 | Cement, gravel |
220 GSM PP + PE | 110 x 65 | 75 | Industrial minerals, sand |
5. FAQs: Addressing Client Concerns
Q1: How does the PE coating prevent powder leakage?
The coating fills microscopic gaps in the woven fabric, reducing pore size to <10 microns—smaller than most cement particles (20–100 microns).
Q2: Are your bags compatible with automated filling systems?
Yes. Our FFS (Form-Fill-Seal) valve bags integrate with rotary packers, achieving speeds of 1,200 bags/hour with <0.2% defect rates.
Q3: Do you offer anti-static options for explosive powders?
Yes. Carbon-coated PP yarns dissipate static, complying with IEC 61340-4-4 standards.
Q4: How do you ensure color consistency in branded bags?
We use Pantone-matched inks and CCD camera-guided printing, achieving ΔE <1.5 color deviation.
6. Why VidePak? Innovation Meets Global Expertise
Since 2008, VidePak has delivered over 500 million PE-coated valve bags to clients in 50+ countries, supported by:
- 100+ circular looms: Produce 8 million bags monthly.
- 30% R&D investment growth: Pioneered biodegradable PE blends (40% starch-based) for eco-conscious markets.
- Starlinger machines: Ensure seam strength consistency (±2% tolerance).
Explore our valve bags for construction materials or dive into PE-coated solutions for chemical powders to see how we elevate industrial packaging.
References
- VidePak Official Website: https://www.pp-wovenbags.com/
- Email: info@pp-wovenbags.com
- Industry Standards: ASTM D5638, EN 277, JIS Z 1539
External Resources
- Learn how valve bags enhance efficiency in construction logistics.
- Discover advanced PE-coated solutions for moisture-sensitive materials.
This article synthesizes data from global regulatory frameworks, third-party lab reports, and VidePak’s operational metrics to deliver actionable insights for procurement professionals.