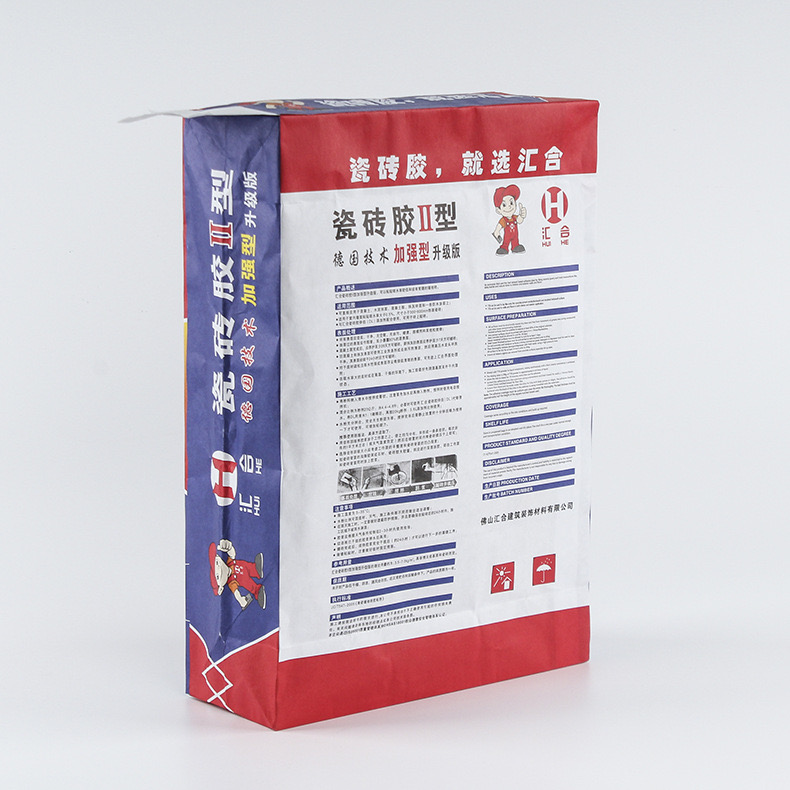
Packaging plays a crucial role in ensuring the safety, durability, and usability of products during transportation and storage. For businesses looking to transport granular or powdery substances like cement, chemicals, or grains, the choice of packaging material is especially important. Among the various packaging solutions, PE Coated Valve Woven Bags have become a popular choice. In this article, we will discuss why customers opt for PE Coated Valve Woven Sacks, how they differ from BOPP Laminated Bags, and explore the significance of fine and coarse yarn selection in bag manufacturing.
What Are PE Coated Valve Woven Bags?
PE Coated Valve Woven Bags are commonly used in industries such as construction, chemicals, agriculture, and food products. These bags are designed with a woven polypropylene (PP) fabric that is coated with a layer of polyethylene (PE) for added durability, moisture resistance, and a higher level of protection for the contents inside. The valve opening at the top of the bag allows for easy filling of the bag and ensures a tightly sealed package once it’s filled. This combination of woven PP fabric and PE coating makes them strong, reliable, and ideal for packing a wide variety of materials.
Why Customers Choose PE Coated Valve Woven Bags
- Moisture Resistance: The PE coating provides excellent moisture protection. This makes the bags ideal for packaging products that may be sensitive to moisture, such as fertilizers, cement, or food products like rice and sugar.
- Cost-Effective Solution: The production process of PE Coated Valve Woven Bags is often more economical than other types of packaging, such as paper or aluminum bags. The use of PP and PE is cost-effective while maintaining strength and durability.
- Customizability: These bags can be customized in terms of size, shape, and printing, allowing businesses to enhance their branding and ensure that packaging fits their specific needs.
- Strength and Durability: The combination of woven PP fabric and the PE coating results in a robust packaging solution that can withstand the rigors of transportation and handling without tearing or losing shape.
Differences Between PE Coated Valve Woven Bags and BOPP Laminated Bags
When considering packaging solutions, many customers often find themselves weighing the differences between PE Coated Valve Woven Bags and BOPP Laminated Bags. These two types of packaging may seem similar at first glance, but they have distinct characteristics that make them suitable for different applications.
Feature | PE Coated Valve Woven Bags | BOPP Laminated Bags |
---|---|---|
Material | Woven polypropylene (PP) coated with polyethylene (PE) | Woven polypropylene (PP) coated with biaxially oriented polypropylene (BOPP) film |
Moisture Resistance | High, due to PE coating | Moderate, due to the properties of BOPP |
Durability | High, with added protection from external elements | High, but less resistant to water and moisture compared to PE-coated bags |
Customization | Can be customized with simple printing | Offers higher-quality printing options due to the BOPP film’s smooth surface |
Applications | Suitable for heavy-duty materials, such as cement, chemicals, and food products | Typically used for retail products, like pet food, seeds, and grains |
Cost | More affordable due to simpler manufacturing | Higher cost due to BOPP lamination process |
Sustainability | Generally more environmentally friendly | BOPP is more recyclable but may not offer the same eco-benefits as PE-coated bags |
While BOPP Laminated Bags offer superior printing quality and are better suited for consumer-facing packaging, PE Coated Valve Woven Bags are generally more affordable, durable, and better for heavy-duty, industrial applications.
For more details on the benefits and versatility of PE Coated Valve Woven Bags, visit this link.
The Importance of Fine and Coarse Yarn in Valve PP Bags
The strength and reliability of Valve PP Bags are not only a result of the materials used but also the selection of yarn type—fine yarns or coarse yarns—and the weaving technology behind them. The quality and strength of woven bags depend on how these yarns are produced and processed.
Fine Yarn vs. Coarse Yarn: Key Differences
- Fine Yarn: Fine yarns have a smaller diameter and are often used to create fabrics with a finer weave. They provide a smoother surface and are ideal for applications where printability and a sleek finish are important. Fine yarn bags can handle light to medium-duty applications but may not be as durable as coarse yarn bags for heavy-duty uses.
- Coarse Yarn: Coarse yarns are thicker, offering greater tensile strength. Bags made from coarse yarn are better suited for heavy-duty applications where the bag must withstand more stress and pressure. They are commonly used for bulk products like chemicals, feed, or cement.
The Role of Starlinger and W&H Equipment in Yarn Selection
At VidePak, we pride ourselves on using world-class manufacturing technology to ensure the highest standards of quality and durability in our woven bags. We have partnered with top-tier equipment manufacturers like Starlinger, based in Austria, and W&H (Windmöller & Hölscher), based in Germany, to optimize our production processes and offer the best quality products.
- Starlinger Equipment: Starlinger is known for its innovative technology in the field of woven fabric production. Their machinery is essential for creating the perfect yarns for woven bags, ensuring that our bags have the required strength, flexibility, and durability. The use of Starlinger circular looms ensures precise weaving patterns that allow for the customization of fine or coarse yarns.
- W&H Equipment: W&H specializes in extrusion and lamination systems that are key in enhancing the properties of woven fabric. Their advanced extrusion lines allow us to create high-quality polyethylene coatings for our PE Coated Valve Woven Bags, ensuring moisture resistance and enhanced durability.
The combination of these cutting-edge machines guarantees that our Valve Woven Bags—whether made with fine yarns or coarse yarns—offer superior performance for all kinds of industrial applications.
To learn more about the role of machinery and technology in enhancing packaging, explore our Valve PP Bags production.
Conclusion
When it comes to choosing the right packaging solution, both PE Coated Valve Woven Bags and BOPP Laminated Bags have their respective advantages. PE Coated Valve Woven Bags stand out due to their strength, durability, and cost-effectiveness, particularly for heavy-duty and industrial applications. At the same time, the selection of yarn—fine or coarse—greatly affects the final product’s performance. Through the use of state-of-the-art equipment from Starlinger and W&H, VidePak ensures that its bags meet the highest standards in the industry, providing customers with reliable and high-quality packaging solutions.