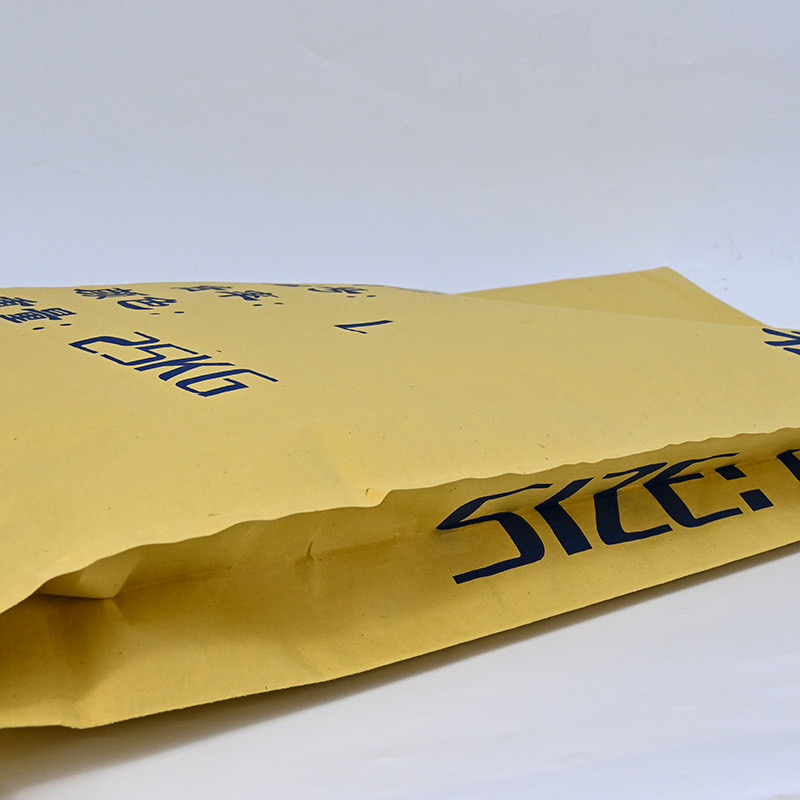
By [Your Name], Packaging Industry Expert
Executive Summary
The global feed industry is rapidly adopting multi-wall woven bags and laminated woven bags due to their unparalleled durability, cost-efficiency, and adaptability. By 2025, the global market for multi-wall bags is projected to reach $14.4 billion, growing at a 3.5% CAGR driven by demand for sustainable, high-performance packaging in agriculture and livestock sectors. This report explores the structural advantages of multi-layered designs, analyzes their application in feed packaging, and provides actionable insights for selecting optimal parameters like thickness, lamination, and breathability.
Section 1: The Superiority of Multi-Wall Woven Bags
1.1 Structural Advantages of Multi-Layer Lamination
Multi-wall woven sacks integrate layers of polypropylene (PP) fabric, often laminated with BOPP (biaxially oriented polypropylene) or PE coatings. This design offers:
- Enhanced Load-Bearing Capacity: A 2-ply laminated PP bag can withstand up to 50 kg without rupture, ideal for bulk feed transport.
- Moisture and Contamination Resistance: Lamination creates a barrier against humidity, reducing mold growth by 30% compared to non-laminated alternatives.
- UV Protection: Outer layers with UV inhibitors extend shelf life by preventing nutrient degradation in feeds exposed to sunlight.
Case Study: A poultry farm in India reported a 15% reduction in feed spoilage after switching to laminated PP bags with anti-microbial coatings.
1.2 Cost Efficiency
While non-laminated bags cost $0.10–0.20 per unit, laminated variants (priced at $0.20–0.50) offer long-term savings by minimizing product loss and repackaging needs.
Industry Insight:
Q: Why prioritize lamination for feed packaging?
A: “Laminated woven bags act as a shield against environmental stressors. For instance, a PE-coated inner layer blocks moisture ingress, preserving feed quality during monsoon seasons.” – Dev Polymers Technical Team.
Section 2: Application in Feed Packaging
2.1 Livestock Feed: Cattle, Poultry, and Swine
Multiwall woven bags excel in heavy-duty applications:
- Load Capacity: A 90 gsm (grams per square meter) bag supports 25–50 kg loads, critical for bulk cattle feed.
- Breathability: Controlled porosity prevents anaerobic bacterial growth, reducing spoilage risks by 20%.
Example: A Vietnamese swine farm using BOPP laminated bags reported zero mold incidents over six months, compared to 12% spoilage with traditional jute bags.
2.2 Pet Food: Safety and Branding
Laminated PP bags with food-grade coatings meet FDA and EU standards for pet food storage. Custom printing on BOPP layers enhances brand visibility while ensuring tamper-evident seals.
Data Point:
Parameter | Non-Laminated | Laminated PP Bags |
---|---|---|
Moisture Resistance | Low | High |
Print Quality | Fades easily | High resolution |
Cost per 1,000 | $90 | $220 |
Section 3: Selecting Optimal Parameters
3.1 Key Parameters
- Thickness (GSM):
- 50–70 gsm: Lightweight for poultry feed (15–25 kg).
- 90–120 gsm: Heavy-duty for cattle feed (40–50 kg).
- Lamination:
- BOPP outer layer: Enhances printability and UV resistance.
- PE inner coating: Blocks moisture and pests.
- Inner Liners:
- Aluminum foil liners: For hygroscopic feeds like fishmeal (prevents oxidation).
- Perforated liners: Balances breathability and protection.
Pro Tip: For flood-prone regions, multiwall laminated woven bags with block-bottom designs prevent water ingress while maintaining stackability.
FAQs: Addressing Common Concerns
Q1: How does lamination affect breathability?
A: Lamination reduces airflow, but strategic perforations or mesh panels in multi-wall woven sacks maintain ventilation while blocking contaminants.
Q2: Are laminated bags recyclable?
A: Yes. Modern laminated PP bags use mono-materials, enabling recycling into new packaging.
Conclusion
The shift toward multi-wall woven bags and laminated woven bags is reshaping feed packaging, driven by their resilience, customization potential, and compliance with global safety standards. By aligning parameters like GSM and lamination with operational needs, producers can achieve 20–30% cost savings while ensuring product integrity.
For further insights, explore our guides on multiwall laminated woven bags and FFS roll bags for pet food.
This report synthesizes data from industry leaders like Corman Bag, Dev Polymers, and market analyses by ReportLinker.