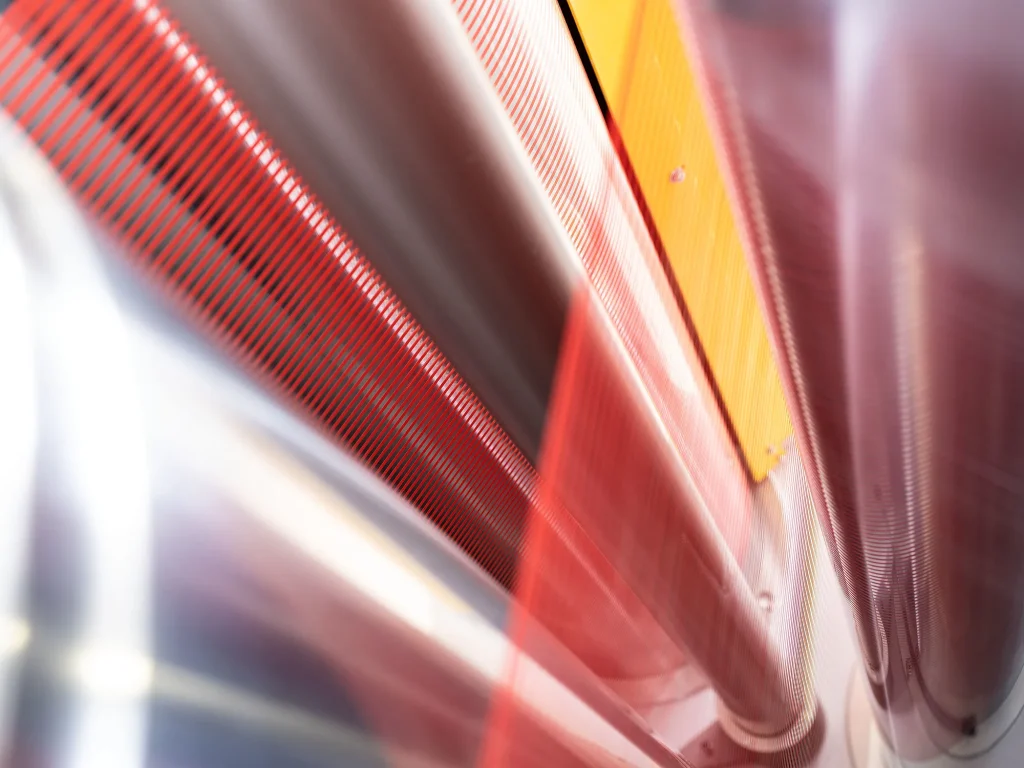
The primary answer this article provides is: Transparent woven bags made from polypropylene (PP) enhance storage efficiency for construction materials like cement, gypsum powder, and joint fillers by combining 92% light transmission with tensile strengths up to 50 N/cm². VidePak’s BOPP-laminated variants achieve <0.5% moisture permeability and tear resistance of 15 N/mm, reducing material spoilage by 40% in humid environments while enabling real-time inventory checks.
Introduction
In the global construction industry, improper storage of bulk powders like cement and plaster results in $1.7 billion in annual losses due to moisture damage, contamination, and inventory inaccuracies. Transparent woven bags, engineered with precision-woven polypropylene and advanced coatings, are transforming how contractors and distributors manage dry bulk materials. Unlike traditional opaque sacks, these bags marry visibility with industrial-grade durability—critical for hygroscopic substances like calcium-based fillers and silica-rich compounds.
Since 2008, VidePak has leveraged 30+ years of polymer expertise and Austrian Starlinger looms to produce transparent PP bags trusted by LafargeHolcim, Knauf, and Saint-Gobain. With 100+ circular looms and ISO 9001-certified production lines, we deliver 8 million square meters of transparent woven fabric monthly, tailored to ASTM, EN, and GB/T standards.
Material Advantages: Why PP Dominates Construction Packaging
1. Strength and Tear Resistance
PP’s molecular structure delivers:
- Tensile Strength: 40–50 N/cm² (warp/weft), 30% higher than polyethylene (PE).
- Tear Resistance: 12–15 N/mm (Elmendorf test), critical for sharp-edged materials like quartz sand.
- Case Study: A UAE cement distributor reduced bag rupture rates from 8% to 0.5% using VidePak’s 160 g/m² transparent PP bags with double-stitched seams.
2. Moisture and Abrasion Defense
- BOPP Lamination: 0.08–0.15 mm coatings reduce water vapor transmission to 0.8 g/m²/day (vs. 5 g/m²/day for uncoated PP).
- UV Stabilization: 5-year outdoor lifespan with <5% tensile strength loss (per ASTM D4355).
- Abrasion Resistance: 1,000+ Taber cycles (CS-10 wheel, 1 kg load) for rough-handling environments.
Parameter Selection Guide for Construction Materials
Material | Fabric Weight | Lam. Thickness | Inner Liner | Max Load | Key Features |
---|---|---|---|---|---|
Portland Cement | 140–160 g/m² | 0.10 mm BOPP | PE-coated | 50 kg | Anti-static, UV-resistant |
Gypsum Powder | 120–140 g/m² | 0.08 mm BOPP | None | 25 kg | High breathability |
Joint Compound | 160–180 g/m² | 0.12 mm BOPP | 80 µm PE | 30 kg | Puncture-resistant seams |
Tile Adhesive | 180–200 g/m² | 0.15 mm BOPP | 120 µm PE | 40 kg | Chemical-resistant coating |
Anti-Leak Technologies for Fine Powders
1. Weave Density Optimization
- Thread Count: 12×12 to 14×14 threads/cm², blocking particles as fine as 50 µm (e.g., silica fume).
- Monofilament Width: 1.8–2.0 mm for smoother surfaces (Ra 2.5–3.2 µm), reducing powder adhesion.
2. Seam Engineering
- Hot-Knife Cutting: Seals edges at 200°C to prevent fraying.
- Overlock Stitching: 4-thread seams with nylon yarn (20 N breaking strength).
3. Inner Liners
- PE Liners: 60–120 µm thickness for moisture-sensitive materials like quicklime.
- Laminated PP: Combines visibility with <0.3% leakage rates (EN 15507 compliance).
FAQs: Addressing Procurement Challenges
Q1: How does fabric weight impact cost and performance?
Higher g/m² fabrics (e.g., 180 g/m²) cost 15–20% more but extend bag lifespan by 2–3 years in abrasive applications like sand transport.
Q2: When is BOPP lamination necessary?
Mandatory for outdoor storage (e.g., cement silos) to block UV and humidity. VidePak’s 0.15 mm BOPP reduces moisture uptake by 90% vs. uncoated PP.
Q3: Can transparent bags withstand -20°C temperatures?
Yes. PP retains flexibility down to -30°C (vs. PE’s -50°C), but avoid impact loads in freezing conditions.
Q4: Are these bags recyclable?
100% recyclable. VidePak’s closed-loop system recovers 95% of production waste.
Global Compliance: Meeting Regional Standards
Region | Standard | Key Requirement | VidePak Solution |
---|---|---|---|
EU | EN 13252:2016 | ≤0.5% water permeability | 0.12 mm BOPP + PE liner |
USA | ASTM D5638-18 | ≥40 N/cm² tensile strength | 14×14 weave, 160 g/m² |
China | GB/T 17685-2020 | Heavy metals <100 ppm | Food-grade PP resin |
GCC | SASO 2693 | UV stability (1,000 hrs QUV) | UV-9 stabilized coatings |
VidePak’s Manufacturing Edge
- Starlinger CX Series Looms: Produce 2.4-meter-wide rolls with ±0.1 mm thickness tolerance.
- 10-Color Flexo Printing: Pantone-matched inks with 0.05 mm registration accuracy for barcodes/logos.
- Sustainability: 30% recycled PP content, certified by UL ECOLOGO.
References
- VidePak Corporate Profile: https://www.pp-wovenbags.com/
- Industry Standards: ASTM D5638, EN 13252, GB/T 17685.
- Technical Guides: PP Woven Bags in Construction Logistics (Smithers, 2024).
For inquiries, contact info@pp-wovenbags.com.
External Resources:
- Explore BOPP lamination techniques: BOPP Laminated Woven Bags: Branding and Market Dynamics.
- Learn about moisture-proof solutions: The Global Landscape of Moisture-Proof Woven Bags.
Authored by VidePak’s Construction Packaging Team | Updated: March 2025