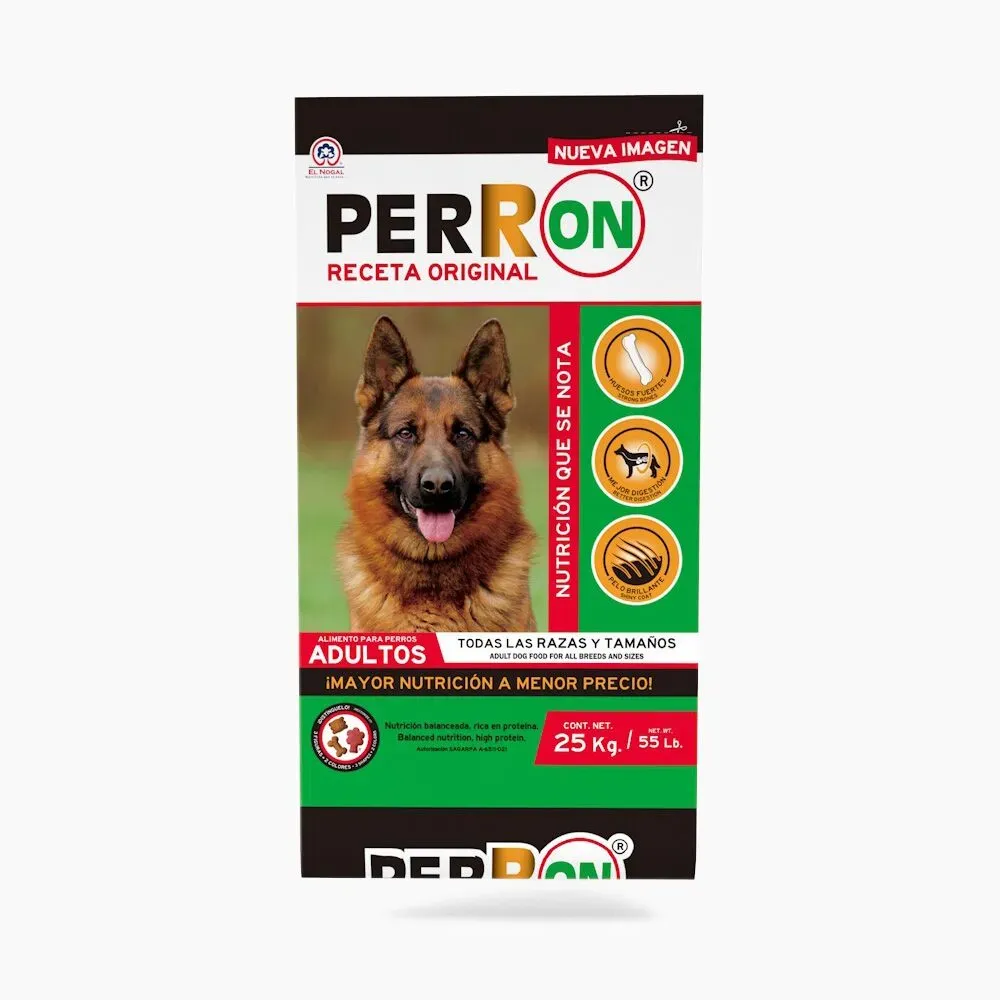
Woven bags with PE (Polyethylene) liners are widely used across industries for their excellent durability, moisture resistance, and flexibility. The addition of an inner liner enhances the bag’s protective properties, ensuring that sensitive materials remain safe from contamination, moisture, and external factors during transportation and storage. In this article, we will delve into the key characteristics of woven bags with PE liners and explore the advanced manufacturing process behind these high-performance packaging solutions, which involves world-renowned equipment from Starlinger.
What Are Woven Bags with PE Liners?
Woven bags with liners are polypropylene (PP) woven sacks that include an additional inner lining, usually made from PE. This liner provides an extra layer of protection and is particularly useful for packaging materials that require a high level of moisture resistance and protection from external elements, such as chemicals, grains, cement, and other sensitive goods.
Key Features of Woven Bags with PE Liners
- Durability: The woven structure of the outer PP material offers strong tensile strength and puncture resistance, making these bags ideal for heavy-duty applications.
- Moisture Resistance: The inner PE liner provides a barrier that protects the contents from moisture, ensuring the integrity of sensitive products.
- Versatility: These bags are widely used in various industries, including agriculture, chemicals, food, and construction.
- Customizability: Woven bags with liners can be tailored to different sizes, thicknesses, and additional features, such as printing and closures.
Parameter | Description |
---|---|
Material | Outer: PP Woven, Inner: PE Liner |
Weight Capacity | 10kg to 100kg, depending on size and material thickness |
Moisture Barrier | High moisture resistance due to the PE liner |
Lamination | Optional lamination for added strength and moisture control |
Printing Options | Up to 8-color printing using advanced printing technology |
Available Sizes | Customizable as per client requirements |
UV Resistance | Optional UV treatment to prolong life under sunlight |
Benefits of PE Liners in Woven Bags
PE liners are crucial for industries that require moisture protection, such as those handling powdered materials, grains, or chemical products. Below are some of the major benefits of using woven bags with PE liners:
- Protection Against Moisture: The PE liner serves as a reliable moisture barrier, preventing the contents from getting damp or spoiled. This is particularly important for industries such as agriculture, where grains, seeds, or fertilizers need to stay dry.
- Improved Product Integrity: The liner reduces the risk of contamination and preserves the quality of the contents. For instance, in the chemical industry, the liner helps keep potentially corrosive materials isolated from the external environment.
- Enhanced Versatility: Woven bags with liners are suitable for a variety of applications due to their customizable nature. Whether it’s a food-grade application or industrial use, these bags can be modified to meet specific requirements, including size, material thickness, and additional features like valve tops or bottom closures.
- Increased Load Capacity: The combination of a woven structure and a PE liner ensures that the bags can carry heavier loads without compromising on structural integrity. Depending on the application, these bags can safely transport weights ranging from 10 kg to 100 kg or more.
Manufacturing Process: Ensuring Quality with Starlinger Equipment
One of the significant factors contributing to the reliability and efficiency of woven bags with PE liners is the advanced manufacturing process. At VidePak, we utilize state-of-the-art machinery from Starlinger, a globally recognized equipment supplier for producing woven bags. Starlinger’s high-tech solutions allow us to achieve superior product quality and production efficiency.
1. Extrusion and Taping (Laying the Foundation)
The manufacturing process begins with extrusion, where polypropylene granules are melted and stretched to form tapes. These tapes are then wound onto bobbins, which are used in the next step of weaving. Starlinger’s extrusion technology ensures consistent tape width and thickness, vital for achieving uniformity and durability in the final woven fabric.
2. Circular Weaving (Building the Woven Structure)
In the weaving stage, the PP tapes are fed into circular looms to create a woven fabric. Starlinger’s circular weaving machines are known for their precision and high speed, producing woven fabrics with minimal defects and consistent quality. The circular looms allow for continuous weaving, resulting in a seamless woven bag structure that offers enhanced strength and flexibility.
3. Lamination and PE Liner Insertion (Adding the Protective Layer)
Once the woven fabric is produced, it undergoes lamination if required. Laminating the woven structure provides additional protection against moisture and increases the bag’s durability. After lamination, the PE liner is inserted. This liner acts as a second layer of defense, providing waterproofing properties.
Starlinger’s cutting-edge lamination equipment ensures that the PE liner is securely and precisely inserted into the woven bags, offering excellent bonding between the layers and ensuring that the liner does not shift or detach during use.
4. Printing (Customization for Branding and Identification)
Printing plays a significant role in making these bags functional and appealing. Starlinger’s printing machines allow us to print up to 8 colors, including complex designs and logos, on both the woven and laminated layers. Using systems that support CMYK, Pantone, and RAL color systems, the printing is not only high-quality but also durable, ensuring that logos and other designs do not fade quickly.
5. Final Processing (Cutting, Stitching, and Packaging)
Once the PE liners are inserted and the bags printed, the next step involves cutting the woven fabric into desired sizes. Starlinger’s automated cutting and stitching systems ensure precise cuts and secure stitching, leading to bags that are reliable and can withstand heavy loads.
Each bag is inspected for quality control, ensuring that the seams are strong, the liner is properly inserted, and the printing is clear. Quality checks include mechanical stress tests, moisture barrier assessments, and visual inspections to confirm the bag meets industry standards.
Quality Control: Ensuring Consistency and Durability
From raw material procurement to the final product, quality control plays a critical role in our production process. We source only high-quality PP and PE granules to ensure that the bags offer consistent strength and flexibility.
- Raw Material Inspection: We conduct thorough checks on the incoming polypropylene and polyethylene granules. This includes testing for tensile strength, moisture content, and melt flow index, which are critical for maintaining the quality of the woven fabric and PE liner.
- In-process Monitoring: Throughout the production process, our systems continuously monitor tape thickness, fabric weave tightness, and liner insertion quality to ensure that each step meets strict standards.
- Final Product Testing: The final woven bags with liners are subjected to a series of tests, including load-bearing capacity, moisture resistance, and print durability tests, to ensure they perform well under real-world conditions.
Conclusion: A High-Performance Packaging Solution
Woven bags with PE liners represent a versatile and high-performance solution for industries requiring durable, moisture-resistant packaging. Whether you’re handling agricultural products, chemicals, or construction materials, these bags offer the reliability and protection needed to ensure product safety.
At VidePak, our commitment to quality and innovation is backed by the latest equipment from Starlinger, ensuring that every bag we produce meets the highest standards of strength, durability, and customizability. From precise lamination to high-quality printing, we provide solutions tailored to the specific needs of different industries while maintaining rigorous quality control.
By combining advanced technology, superior raw materials, and strict quality standards, we continue to offer premium woven bags with PE liners that cater to the ever-evolving demands of the market.
Keywords in Action
- Woven Bags with Liner
- Woven sacks with Liner
- Aluminum Liner Bags
- Liner PE Bags
- Woven bags with liner
- Woven Bags with PE Liner