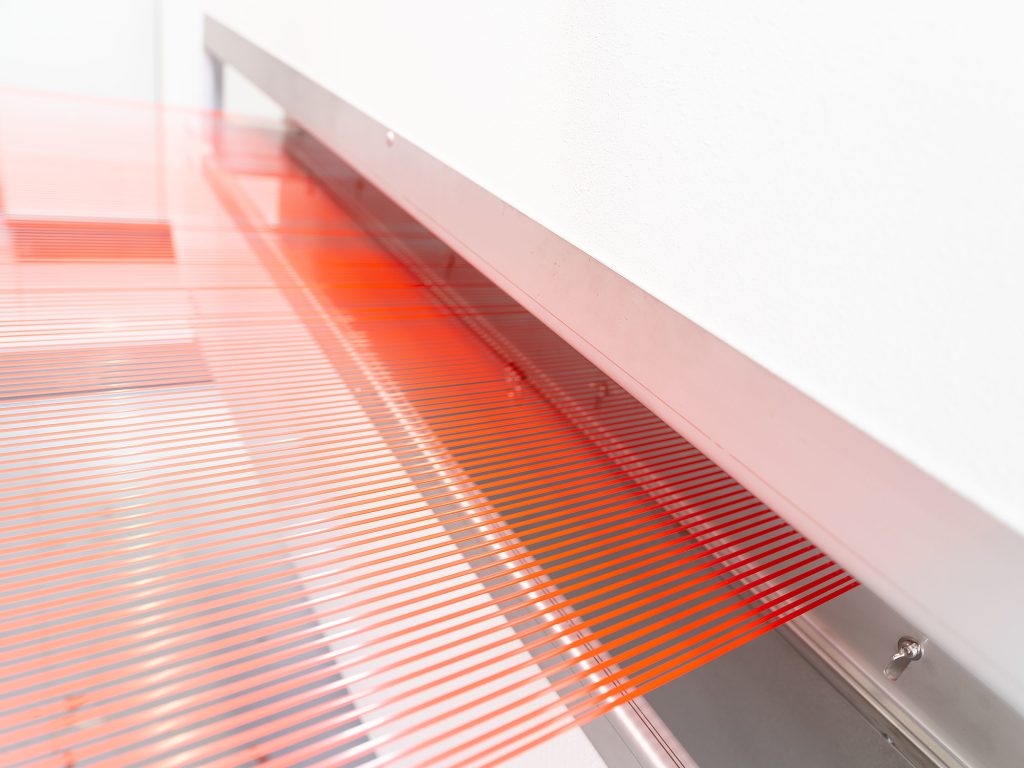
Introduction
The construction industry relies on robust and efficient solutions for transporting and storing materials like cement, sand, and aggregates. Woven fabric bags, enhanced by advanced production technologies from Starlinger and W&H, have become indispensable for their durability, flexibility, and sustainability. This report highlights the critical role of woven fabric bags in modern construction, focusing on the precise production techniques that ensure their superior performance.
Advantages of Woven Fabric Bags
1. Exceptional Durability
Woven fabric bags are designed to withstand heavy loads and harsh conditions. Their strength is achieved through the precise control of extrusion and stretching processes, ensuring the polypropylene fibers are of uniform quality.
- How It Works: Starlinger’s extrusion lines maintain optimal temperatures to create consistent polypropylene filaments. If the temperature is too high, the filaments become brittle; too low, and the material lacks the required tensile strength. The resulting fibers can support significant loads without tearing, crucial for transporting materials like cement or gravel.
2. Customization for Specific Needs
Woven fabric bags can be tailored to meet diverse construction requirements, including UV resistance for outdoor storage and anti-slip coatings for safer handling.
- Example of Use: UV-resistant woven bags are particularly valuable for storing cement outdoors, where exposure to sunlight can degrade standard packaging. VidePak incorporates lamination technology from W&H to create protective layers that ensure content integrity.
3. Cost Efficiency
Lightweight yet strong, woven fabric bags reduce logistics costs by enabling more efficient stacking and transport. Their reusability further enhances cost-effectiveness compared to single-use packaging.
The Role of Advanced Technology in Quality
Temperature Control in Extrusion
Extrusion is the process where polypropylene is melted and shaped into filaments. Precise temperature management is crucial to produce fibers with consistent strength and flexibility.
- Why It Matters: Temperature fluctuations can result in weak or uneven fibers, compromising the bag’s overall durability. By using Starlinger’s high-precision equipment, VidePak ensures stable extrusion processes, producing filaments that meet strict quality standards.
Stretching Ratios in Drawing
The stretching process determines the fibers’ elongation properties, balancing flexibility and rigidity. Accurate control of draw ratios ensures the fabric is robust yet malleable enough to resist tearing during use.
- Impact on Performance: Over-stretched fibers become brittle, while under-stretched ones lack the necessary strength. VidePak uses W&H systems to optimize this process, creating woven fabrics that excel in heavy-duty applications.
Performance Metrics
Metric | Significance | How It’s Ensured |
---|---|---|
Tensile Strength | Prevents tearing under heavy loads. | Precise extrusion and stretching control. |
UV Resistance | Protects against sunlight degradation. | High-quality lamination technology. |
Moisture Resistance | Keeps contents dry and secure. | Optional internal liners and coatings. |
Cost Efficiency | Minimizes transportation and handling expenses. | Lightweight, stackable design. |
VidePak’s Commitment to Excellence
VidePak stands out in the competitive Chinese market by prioritizing quality and sustainability. Unlike manufacturers focused solely on cost-cutting, VidePak invests in advanced equipment and sustainable practices to produce woven fabric bags that exceed industry expectations.
- Technological Edge: Starlinger’s and W&H’s machinery enables precise control of every production stage, from extrusion to lamination. This ensures that each bag delivers consistent performance and durability.
- Sustainability in Focus: By using recyclable polypropylene and minimizing production waste, VidePak aligns with global environmental goals. Learn more about VidePak’s commitment to eco-friendly packaging.
Addressing Common Questions
1. Why are woven fabric bags ideal for the construction industry?
Their high tensile strength and customization options make them suitable for transporting heavy and varied materials like cement and sand.
2. How does advanced technology enhance their quality?
Precision equipment from Starlinger and W&H ensures uniform filament strength and accurate lamination, resulting in durable and reliable bags.
3. Are woven fabric bags environmentally friendly?
Yes, they are made from recyclable polypropylene and designed for reuse, significantly reducing environmental impact.
4. Can these bags be customized for different applications?
Absolutely. Features like UV resistance, anti-slip coatings, and moisture-proof liners make them adaptable to diverse needs.
Future Trends in Construction Packaging
- Automation in Production: Increasing demand for high-quality packaging will drive the adoption of fully automated systems, improving consistency and efficiency.
- Sustainability as a Standard: Recyclable materials and energy-efficient production practices will become industry norms.
- Branding Opportunities: Custom-printed woven bags will gain popularity, enabling businesses to enhance brand visibility while maintaining functionality.
Conclusion
Woven fabric bags have revolutionized material transport and storage in the construction industry by combining durability, efficiency, and sustainability. Backed by advanced technologies from Starlinger and W&H, VidePak’s woven fabric bags set the standard for quality and reliability.
With a commitment to innovation and environmental responsibility, VidePak continues to lead the market, offering solutions that meet the evolving needs of modern construction. Explore more about VidePak’s innovative solutions.