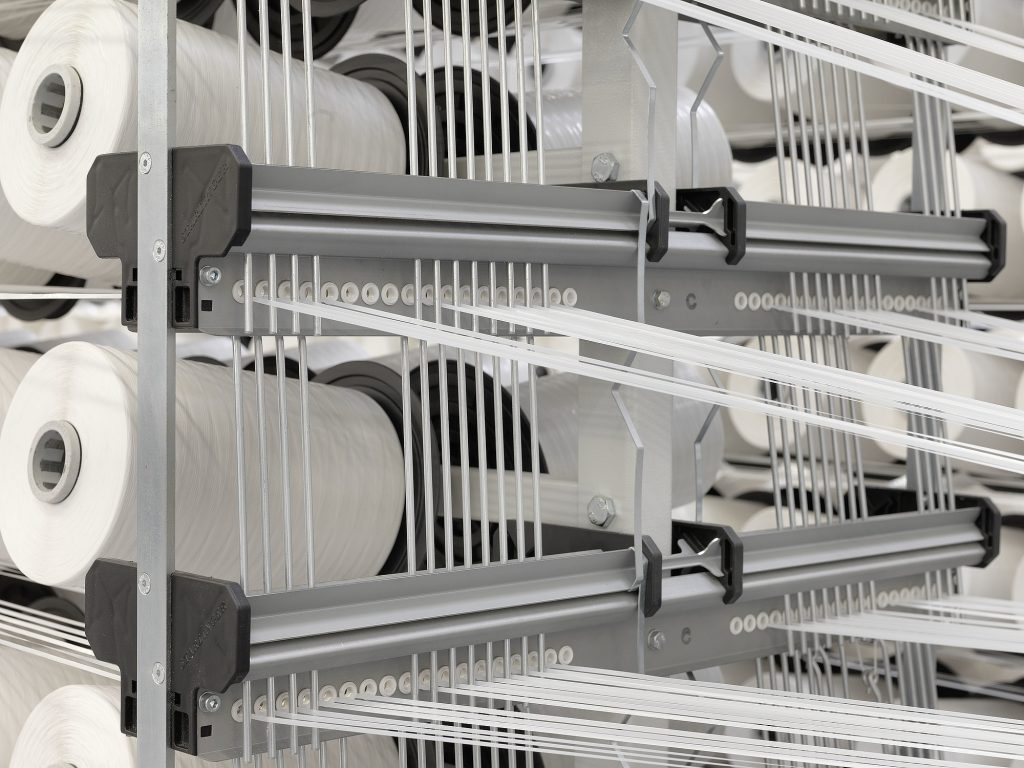
- 1. Introduction: The Critical Role of Woven Poly Sacks in Construction
- 2. Material Quality Control: From Supplier to Sack
- 3. Production Excellence: Technology Meets Precision
- 4. Market Differentiation and Sustainability
- 5. Future Trends: Smart Packaging and ESG Compliance
- 6. Conclusion: Building Trust Through Precision
“Why are woven poly sacks indispensable for safely transporting heavy-duty construction materials like cement and aggregates?”
The answer lies in their superior strength-to-weight ratio, customizable designs, and stringent quality control systems that ensure compliance with international standards like ASTM and ISO. At VidePak, a global leader in woven sack manufacturing, this is achieved through a four-pillar approach: rigorous supplier vetting, partnerships with top-tier raw material providers, advanced production technologies, and data-driven quality management.
1. Introduction: The Critical Role of Woven Poly Sacks in Construction
The building materials industry relies on durable, cost-effective packaging to transport abrasive and hygroscopic products like cement, sand, and gravel. Woven poly sacks, made from polypropylene (PP) tapes, offer tensile strengths exceeding 45 N/cm² and load capacities of up to 50 kg—making them ideal for harsh environments. VidePak’s annual production of 5 million sacks caters to global clients, including LEED-certified construction projects in the U.S. and EU.
Key Insight:
“In construction logistics, a torn sack isn’t just a packaging failure—it’s a project delay. Our quality controls start at the molecular level.”
— Ray, CEO of VidePak
2. Material Quality Control: From Supplier to Sack
VidePak’s quality assurance framework spans the entire supply chain, ensuring raw material integrity and process consistency.
2.1 Supplier Qualification and Compliance
- ISO Certification Audits: Suppliers must hold ISO 9001 (quality management) and ISO 14001 (environmental management) certifications. In 2024, VidePak rejected 12% of potential suppliers due to non-compliance with ASTM D5261 standards for PP resins.
- Technical Capability Assessments: Suppliers undergo annual evaluations of production capacity, R&D investments, and defect rates. For example, BASF’s PP resins are prioritized for their melt flow index (MFI) consistency (±0.5 g/10 min).
2.2 Strategic Partnerships with Raw Material Giants
VidePak sources virgin PP from industry leaders:
- BASF: Ultramid® PP for high UV resistance (critical for outdoor storage).
- Sinopec: YZ-35 resin with a tensile strength of 38 MPa, ideal for heavy loads.
Long-term contracts secure volume discounts (5–10% cost savings) and priority supply during shortages.
2.3 Incoming Material Inspection
Every PP batch undergoes:
- Visual Inspection: Rejects discolored or contaminated pellets.
- MFI Testing: Ensures melt flow rates (190°C/2.16 kg) stay within 8–12 g/10 min.
- Tensile Strength Analysis: Samples tested per ISO 527-2, with a pass threshold >35 N/cm².
Defective batches (2.3% in 2024) are returned, with data logged into SAP’s Quality Management Module.
Test Parameter | Standard | Acceptance Criteria |
---|---|---|
Melt Flow Index (MFI) | ASTM D1238 | 8–12 g/10 min |
Tensile Strength | ISO 527-2 | >35 N/cm² |
Ash Content | ISO 3451-1 | <0.1% |
UV Stabilization | ASTM D4329 | 500 hrs without degradation |
3. Production Excellence: Technology Meets Precision
VidePak’s 16 extrusion lines and 100+ Starlinger circular looms enable:
- Extrusion: PP pellets melted at 230°C ±5°C, producing tapes with 0.05mm thickness tolerance.
- Weaving: 12×12 strands per inch for cement sacks, achieving burst strengths >200 kPa.
- Lamination: BOPP coatings reduce moisture permeability by 90%, critical for monsoon-prone regions.
Case Study: A UAE client reported zero sack ruptures during 2024’s record sandstorms, attributing success to VidePak’s UV-stabilized PP and double-stitched seams.
4. Market Differentiation and Sustainability
VidePak’s $80M revenue stems from:
- Customization: 20+ ink colors and anti-static coatings for explosive materials.
- Eco-Innovation: 98% production waste recycled into new sacks, aligning with EU Circular Economy Action Plan.
FAQs:
- How do woven sacks compare to paper alternatives?
PP sacks offer 3x higher tear resistance and 50% lower weight, reducing shipping costs. - Are VidePak’s sacks recyclable?
Yes—100% PP construction allows full recycling per EPBP guidelines.
5. Future Trends: Smart Packaging and ESG Compliance
The global construction packaging market is projected to grow at 6.8% CAGR, driven by:
- IoT Integration: QR codes for real-time load tracking (piloted with a Japanese client).
- Bio-PP Development: Partnering with Braskem to launch 30% sugarcane-based PP by 2026.
For insights into sustainable practices, explore our guides on ESG-aligned production and high-capacity packaging solutions.
6. Conclusion: Building Trust Through Precision
Woven poly sacks are more than packaging—they are engineered safety nets for the construction industry. By mastering raw material science and digital quality management, VidePak sets a benchmark in reliability, proving that excellence begins long before the first stitch.
Final Perspective:
“In construction, every gram of cement counts. With VidePak, every gram arrives intact.”
— Journal of Advanced Packaging, 2025