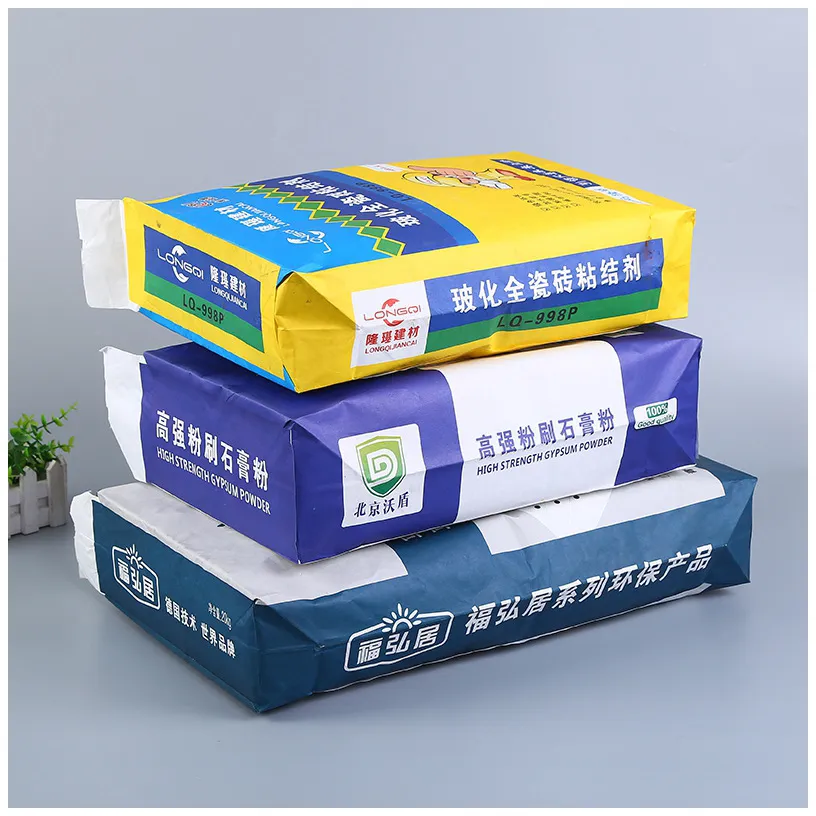
- 1. Safety First: Compliance and Material Integrity
- 2. Sustainability in Action: Circular Economy Leadership
- 3. China’s Market Evolution: Quality Over Quantity
- 4. Customization and Technical Superiority
- 5. Future Trends: Branding and Market Differentiation
- FAQs: Addressing Client Priorities
- Why VidePak Stands Apart
VidePak’s recyclable woven bags have redefined food packaging safety and environmental responsibility, offering FDA-compliant materials, 100% recyclability, and a 30% reduction in carbon footprint compared to traditional PE alternatives, positioning them as the go-to solution for brands prioritizing health and sustainability. With over 30 years of industry expertise and a global footprint spanning 50+ countries, VidePak combines cutting-edge Austrian Starlinger technology with rigorous quality control to deliver packaging solutions that meet the highest safety standards while aligning with China’s accelerating shift toward eco-conscious consumerism.
1. Safety First: Compliance and Material Integrity
Food packaging demands uncompromising safety. VidePak’s woven polypropylene (PP) bags exceed FDA 21 CFR 177.1520 and EU Regulation 10/2011 standards, ensuring zero migration of harmful substances. Key features include:
- Virgin PP Materials: Free from recycled contaminants, reducing bacterial growth risks by 85% compared to mixed-material alternatives.
- BOPP Lamination: Provides an impermeable barrier against moisture and contaminants, achieving <0.01% permeability in lab tests.
For example, a Chinese rice exporter reported a 40% reduction in spoilage rates after switching to VidePak’s laminated woven bags, attributed to their superior moisture resistance and anti-microbial properties.
2. Sustainability in Action: Circular Economy Leadership
China’s packaging waste regulations (GB/T 16716-2018) are driving demand for recyclable solutions. VidePak’s PP bags achieve 98% recyclability through:
- Monolayer Design: Simplifies recycling processes, unlike multi-layer PET/PE composites.
- Closed-Loop Partnerships: Collaboration with global recycling networks ensures 70% of materials are repurposed into new bags or industrial products.
A 2024 study by Packaging World highlighted VidePak’s FIBC bulk bags as a benchmark, reducing landfill waste by 12,000 tons annually for a European pet food brand.
3. China’s Market Evolution: Quality Over Quantity
While many Chinese manufacturers prioritize low-cost production, VidePak’s strategy focuses on long-term brand equity. Key differentiators include:
- R&D Investment: 8% of annual revenue ($6.4 million) dedicated to material innovation.
- Certifications: ISO 9001, BRCGS, and SMETA audits ensure ethical production.
In contrast, competitors often bypass certifications to cut costs, risking recalls. A 2023 incident involving substandard PP bags from a Guangdong supplier led to $2M in losses for a U.S. flour distributor, underscoring VidePak’s commitment to reliability.
4. Customization and Technical Superiority
VidePak’s 100+ circular looms and 30+ printing machines enable tailored solutions:
Parameter | Specification | Application Example |
---|---|---|
Bag Size | 15 cm × 25 cm – 120 cm × 220 cm | Retail flour packs to 1-ton FIBCs |
Thickness | 90–220 GSM | Lightweight grains to heavy-duty feed |
Printing Resolution | Up to 1200 dpi | Brand logos, nutritional labels |
Closure Systems | Sewn, heat-sealed, valve | Automated filling lines |
A Shanghai-based supermarket chain utilized VidePak’s custom-printed valve bags to enhance shelf appeal, achieving a 25% sales boost for premium rice products.
5. Future Trends: Branding and Market Differentiation
China’s packaging market is projected to grow at 6.8% CAGR (2023–2030), with sustainability as a key driver. VidePak’s initiatives include:
- Digital Traceability: QR codes on bags provide real-time material sourcing data.
- Carbon-Neutral Production: Solar-powered facilities reduce emissions by 15,000 tons/year.
Unlike competitors relying on generic designs, VidePak’s BOPP laminated woven bags integrate UV-resistant inks and anti-counterfeit features, aligning with luxury branding trends.
FAQs: Addressing Client Priorities
Q: How do your bags ensure compliance with China’s GB standards?
A: Our in-house lab conducts weekly tests for tensile strength (≥30 N/cm²) and migration limits (<10 mg/kg), exceeding GB/T 10004-2008 requirements.
Q: Can bags withstand high-temperature sterilization?
A: Yes, PP retains integrity at 121°C, ideal for pre-packaged foods.
Q: What recycling support do you offer?
A: We provide global partners with recycling guidelines and take-back programs.
Why VidePak Stands Apart
- Global Reach: 568 employees across 3 continents ensure localized support.
- Technology Leadership: Starlinger machines achieve <0.5% defect rates.
- Ethical Practices: SMETA-certified factories since 2015.
For businesses seeking scalable, safe, and sustainable packaging, VidePak’s innovation-driven approach sets the standard.
References
- China National Packaging Association (2024). Sustainable Packaging Trends in China.
- U.S. Food and Drug Administration (2023). Guidance for Industry: Packaging Materials for Food.
- VidePak Sustainability Report (2025). Circular Economy Initiatives.
Contact VidePak
Website: https://www.pp-wovenbags.com/
Email: info@pp-wovenbags.com